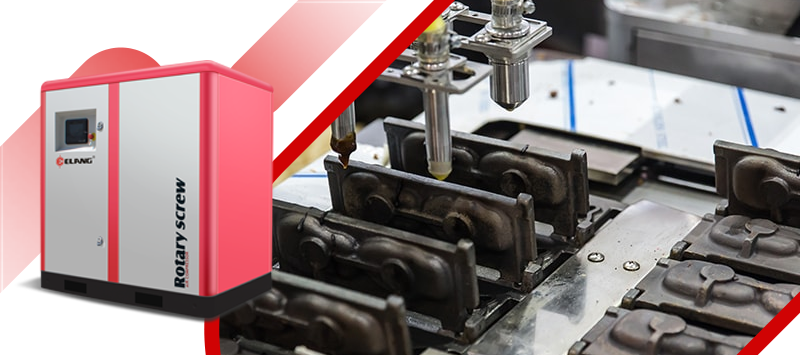
Injection molding industry is an important industry in every country. Its products cover industries as toy mold, shoe mold, container mold, plastic wood mold, tube embryo mold, aviation mold, clothing mold, automobile mold, agricultural tool mold and so on. These industries all need air compressors.
How is the air compressor applied in the injection molding industry?
Injection molding is the process of injecting the plasticized plastic in the melt state (i.e. viscous flow state) into the closed mold cavity with the help of the push force of the screw (or plunger), and obtaining the product after curing. Injection molding is a cycle process, each cycle mainly includes: quantitative feeding – melting and plasticizing – pressure injection – mold filling and cooling – mold opening and parts pick-up. Take out the plastic parts and then close the mold for the next cycle.
What role does the air compressor play in the working process of the injection molding machine?
For injection molding machines with non-hydraulic systems, in each cycle, there are two steps to use the air compressor: pressure injection, mold opening and parts pick-up.
In addition, air compressors and air blow guns are also needed for injection molding machines to prevent rust.
In the injection molding process, there is also a very important technology in the compressed air process, that is, gas-assisted injection molding technology. Basically all thermoplastics used for injection molding and general engineering materials (such as PS, HIPS, PP, ABS…) are suitable for gas-assisted technology. At present, gas-assisted technology is widely used in various plastic products, such as televisions, refrigerators, air conditioners or audio enclosures, automotive plastic products, home appliances, daily necessities, toys, etc. This technology also takes advantage of the compressed air characteristics of an air compressor, which can effectively improve the efficiency and quality of injection molded products.
Elang air compressor has always been known in the industry for its energy-saving, low noise, environmentally-friendly, high quality and stable running. The matching use of injection molding machines is in line with the current new trend of energy saving and environmental protection. The injection molding machine itself is also a high-energy machine, and the energy saving effect of the two is more obvious.
Comparing with other brands of air compressors, Elang’s air compressors highlight its name as the “best partner” in the following aspects:
1. The commonly used pressure range of injection molding machine is about 8bar (0.8Mpa).
In the pressure injection process, the compressed air fluctuation range is stable, and it can even be adjusted at any time to achieve the molding effect of different parts of the mold. Elang energy saving PM VSD air compressor provides the constant working pressure and has an optimized effect in the air volume range, which is very suitable for the working of the injection molding machine.
2. The compressed air must be clean and no-pollution to the mold.
Elang has many experience to providing many well-known injection molding machine manufacturers, the after treatment equipment for multiple links of injection molding machines has become the standard system of Elang air compressors to provide the clean air to injection molding machines.
3. The air delivery must be durable and uninterrupted for the mold clamping device and mold opening and taking part.
This requires the air compressor to have a strong air end. Elang air compressor adopts air end with excellent technology and quality, and with the various technical improvements made by Elang for matching injection molding machine, to provide stable and continuous air delivery for the whole system.
4. Energy saving and environmental protection.
Now the new environmental protection policy promulgated by the government has been officially implemented in china, it is a general trend to save the energy. Elang air compressors are well-known in the industry for energy-saving and low noise. From a long-term perspective, the injection molding machine equipped with Elang PM variable frequency air compressors will achieve considerable savings.
Elang, as a leading provider in the industry, offers highly professional air solutions specifically designed for injection molding machines.
With extensive expertise and experience, Elang understands the unique requirements of the injection molding process and the critical role that air compressors play in ensuring its efficiency and success. Elang’s air solutions are tailored to meet the specific needs of injection molding machines, delivering optimal performance and reliability.
In addition to providing reliable and efficient air compressors, Elang also offers comprehensive after-sales support, including maintenance services, spare parts availability, and technical assistance. This ensures that customers can rely on Elang’s expertise and assistance throughout the lifespan of their injection molding machines.