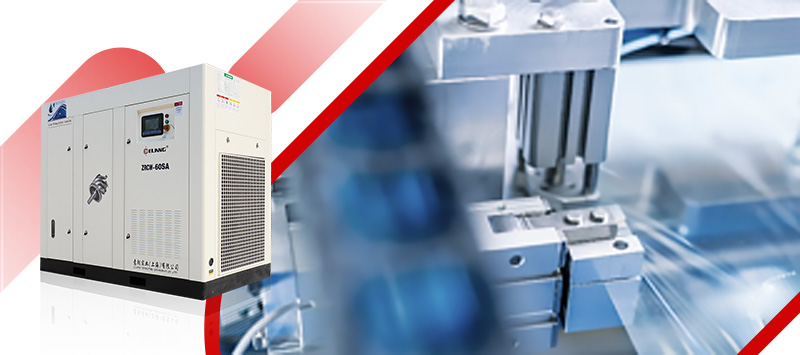
Air compressors are commonly utilized in the packaging industry due to the prevalence of pneumatic controls in packaging machines.
How to Select a Right Air Compressor for a Food Packaging Machine?
1. Please verify the compressed air pressure and flow rate needed for the production line.
It is necessary to confirm the pressure and flow of compressed air required by the production line, as well as the pressure and flow of nitrogen, and then select the air compressor and the matching of the nitrogen generator based on this information.
The pressure of compressed air is generally in three levels of 8, 10, and 13bar. Generally, at a pressure of 8bar, the power consumption per cubic meter of compressed air is about 5.5-6.5kW. It is recommended that the air output of the air compressor is 1.2–2 times larger than the air consumption. That is to say, if the air consumption is 1m3/min, the air output of the air compressor should be between 1.2—2m3/min as much as possible. This is mainly taking into account the air supply guarantee during the shutdown interval of the standby machine and the air compressor maintenance. Note that the air consumption of compressed air here should include the air consumption of the nitrogen generator.
2. The working pressure of the air compressor is determined by the nitrogen generator.
The methods of nitrogen generators now mainly include membrane nitrogen production and molecular sieve nitrogen production. Relatively speaking, the pressure of membrane nitrogen production can be very high, and the nitrogen pressure can reach 400-500 bar. At the same time, the membrane life is relatively long. Long, more suitable for occasions where the gas storage volume is limited and the use pressure is high. The advantage of molecular sieve nitrogen production is that the equipment is small in size, but the life of molecular sieve is relatively low, and molecular sieve needs to be replaced in one year on average. The pressure of compressed air required for general molecular sieve nitrogen production is at least 10bar, usually 13bar, and the pressure of compressed air required for membrane nitrogen production is recommended to be 13bar;
3. Recommendations regarding the configuration of a gas storage tank.
Whether membrane nitrogen production or molecular sieve nitrogen production requires a pre-compressed air treatment system, including water removal, drying, filtration, etc., water removal generally uses ordinary gas-water separators, and drying generally has a refrigerated type. Dryers and adsorption dryers, the dew point of refrigerated dryers after drying can generally reach 10℃, the dew point of adsorption dryers after drying can generally reach -30℃, and the filtration accuracy before nitrogen production should not be less than 0.01 micron The accuracy of other air points depends on the specific requirements. The food industry generally needs to reach 0.001 microns, and is filtered through deodorization, degreasing, and sterilization. If the compressor only uses nitrogen gas for the nitrogen making mechanism, there is no need to add a gas storage tank between the compressor and the nitrogen making machine, but the processing capacity of the air compressor and the nitrogen making machine should correspond to each other, and the difference should not be too large. The gas output of the air compressor should be slightly larger than the gas consumption of the nitrogen generator. It is recommended to add a nitrogen storage tank to the nitrogen after the nitrogen generator. If only part of the compressed air produced by the air compressor is used by the nitrogen generator, an air storage tank must be added before the nitrogen generator. Generally, the volume of the gas storage tank is 0.06–0.1 times the compressed air production volume. The recommended upper limit is conducive to energy saving, but it should not be too large, otherwise the waste will be very serious.
The gas storage tank is mainly used to stabilize the pressure, and it is also a means to maximize the energy efficiency of the air compressor or the nitrogen generator. The cost is not very high. As long as the electricity bills saved each year are relatively objectively used, it is relatively objective.
Today’s packaging machinery has many starting components and pneumatic control solenoid valves, which require compressed air produced by an air compressor to drive, such as vacuum fixtures equipped with robotic arms, and automatic shrink film packaging machines are a kind of pneumatic components and machinery. It is an automatic packaging equipment controlled by PLC and other peripheral circuits. The executive element of the equipment is a cylinder, which is controlled by a two-position five-way solenoid valve to move forward and backward. The working position of the cylinder is detected by a magnetic switch and a proximity switch. Feedback to the PLC, and the PLC sends control commands to the solenoid valve of the corresponding cylinder through the program to control the action of the cylinder.
Elang air compressors make a valuable contribution in these areas as well. With their high efficiency performance, ultra-energy-saving design, and fully automatic control system, Elang air compressors enable unattended operation, making them ideal for integration with various packaging machinery. Manufacturers and users alike choose Elang for their compressed air system needs. Additionally, Elang’s comprehensive after-sales service provides users with the confidence to rely on Elang air compressors for their packaging operations.