4 Units of 280kw 8bar PM Screw Air Compressor in Power Plant
Currently, more than 36% of the world’s power generation capacity comes from thermal power plants, 85% of which is generated from coal.
Compressed air for power plants is used for coal handling, operation of pneumatic instruments connected to boilers, turbines, generators, dust collectors and ash handling systems.
The air system of a power plant is divided into instrument air and service air. As the name implies, instrumentation air is used to operate pneumatic instruments where the quality of the instrumentation air is critical; it needs to meet ISO 8573 Class-1 standards, thus ensuring pulsation-free emission air. This air passes through the solenoid valves of various pneumatic controllers, thus precisely controlling valve operation.
The air system of a power plant is divided into instrument air and service air. As the name implies, instrumentation air is used to operate pneumatic instruments where the quality of the instrumentation air is critical; it needs to meet ISO 8573 Class-1 standards, thus ensuring pulsation-free emission air. This air passes through the solenoid valves of various pneumatic controllers, thus precisely controlling valve operation.
Air is required for cleaning, purging filters and transporting ash. Although service air quality requirements are not as stringent as instrumentation air, some power plants use a single compressed air solution for both service air and instrumentation air, thereby alleviating the need for spare parts and associated inventory.
Depending on the application of compressed air in a power plant, the required pressure can vary. Typically, the pressure range is 7 to 8 bar (low volume, high pressure) for instrumentation air and 3 to 5 bar (high volume, low pressure) for conveying/ ash removal handling systems. Depending on the application, the compressor design may also change to suit the flow and pressure requirements.
Power plants are classified according to the amount of power generated in megawatts. Conventional power plants have a capacity of between 250 and 500 MW.
With recent developments, current power plants are designed to generate up to 1,200 MW of capacity. These power plants are called ultra-supercritical power plants.
With advances in technology, these plants occupy the same space as conventional power plants, thus saving space and utilities, while saving on operating costs.
Over the years, technological advances have led to the optimization of operating costs for power plants around the world. Screw air compressors and centrifugal air compressors have received strong interest due to their high reliability and low operating costs. Centrifugal air compressors in particular have been adopted in applications requiring large volumes of air in excess of 3500 Nm3/hr, thus justifying capital costs and reducing the number of compressors required while increasing plant efficiency.
Variable frequency screw compressors are the preferred solution for applications with high load fluctuations. Under highly variable loads, these compressors are highly adaptable and ensure consistent pressure, which is critical for the operation of pneumatic valves and actuators in power plants.
As global industry expands and a growing population will drive demand for electricity. This will lead to an expansion of power plant capacity worldwide. Due to lower operating costs and consistent performance, compressed air technology is being widely adopted in this sector, saving costs while extending the life of the machines.
Currently, more than 36% of the world’s power generation capacity comes from thermal power plants, 85% of which is generated from coal.
Compressed air for power plants is used for coal handling, operation of pneumatic instruments connected to boilers, turbines, generators, dust collectors and ash handling systems.
The air system of a power plant is divided into instrument air and service air. As the name implies, instrumentation air is used to operate pneumatic instruments where the quality of the instrumentation air is critical; it needs to meet ISO 8573 Class-1 standards, thus ensuring pulsation-free emission air. This air passes through the solenoid valves of various pneumatic controllers, thus precisely controlling valve operation.
The air system of a power plant is divided into instrument air and service air. As the name implies, instrumentation air is used to operate pneumatic instruments where the quality of the instrumentation air is critical; it needs to meet ISO 8573 Class-1 standards, thus ensuring pulsation-free emission air. This air passes through the solenoid valves of various pneumatic controllers, thus precisely controlling valve operation.
Air is required for cleaning, purging filters and transporting ash. Although service air quality requirements are not as stringent as instrumentation air, some power plants use a single compressed air solution for both service air and instrumentation air, thereby alleviating the need for spare parts and associated inventory.
Depending on the application of compressed air in a power plant, the required pressure can vary. Typically, the pressure range is 7 to 8 bar (low volume, high pressure) for instrumentation air and 3 to 5 bar (high volume, low pressure) for conveying/ ash removal handling systems. Depending on the application, the compressor design may also change to suit the flow and pressure requirements.
Power plants are classified according to the amount of power generated in megawatts. Conventional power plants have a capacity of between 250 and 500 MW.
With recent developments, current power plants are designed to generate up to 1,200 MW of capacity. These power plants are called ultra-supercritical power plants.
With advances in technology, these plants occupy the same space as conventional power plants, thus saving space and utilities, while saving on operating costs.
Over the years, technological advances have led to the optimization of operating costs for power plants around the world. Screw air compressors and centrifugal air compressors have received strong interest due to their high reliability and low operating costs. Centrifugal air compressors in particular have been adopted in applications requiring large volumes of air in excess of 3500 Nm3/hr, thus justifying capital costs and reducing the number of compressors required while increasing plant efficiency.
Variable frequency screw compressors are the preferred solution for applications with high load fluctuations. Under highly variable loads, these compressors are highly adaptable and ensure consistent pressure, which is critical for the operation of pneumatic valves and actuators in power plants.
As global industry expands and a growing population will drive demand for electricity. This will lead to an expansion of power plant capacity worldwide. Due to lower operating costs and consistent performance, compressed air technology is being widely adopted in this sector, saving costs while extending the life of the machines.
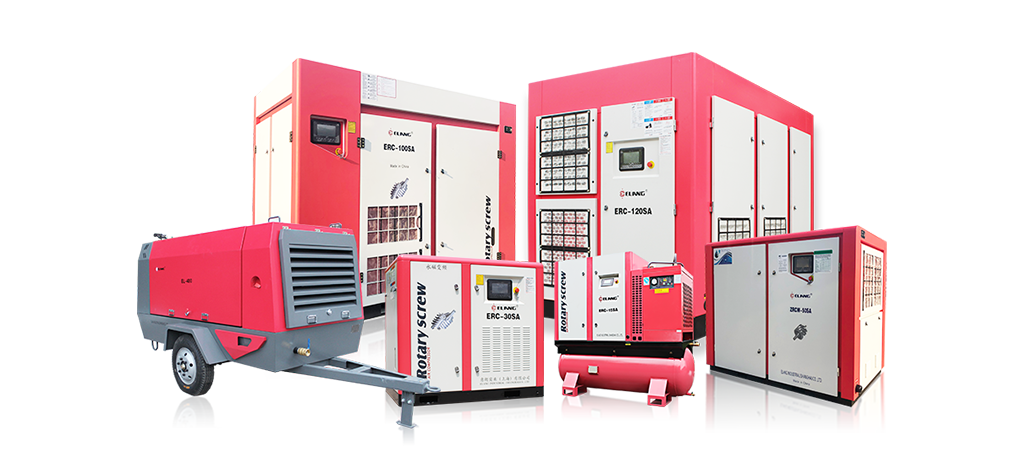