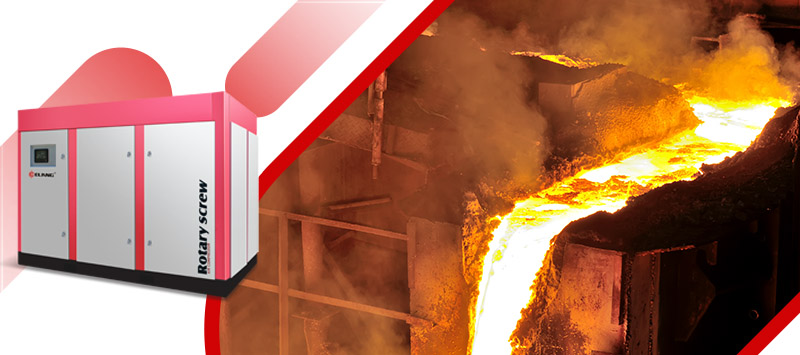
Iron and steel industry refers to the production of pig iron, steel, steel, industrial pure iron and ferroalloy industry, is one of the basic industries of all industrialized countries in the world.
The equipment used by the new iron and steel enterprises is the most advanced equipment, and some old iron and steel enterprises need to carry out equipment transformation, in order to improve the production efficiency of enterprises, so that the old enterprise coruscated with new vitality.
In this process, the compressor is indispensable everywhere.The use of compressed air in steel companies is included in all production processes.
As a large market demand for air compressors, how should the iron and steel industry configure air compressors?
General air compressor station configuration of iron and steel enterprises: air compressor types generally include centrifugal, screw and so on.0.38mpa, 0.5mpa for steelmaking, continuous casting, 0.8mpa for power/instrument, 1.3mpa for blast furnace coal injection. Air compressor station is generally configured with 2-8 units of screw compressors, most of which are less than 10 – 40m3/min. Screw air compressor is mainly used as the auxiliary air source of centrifugal air compressor.
Compressed air plays a significant role in iron and steel enterprises, with its distribution primarily focused on areas such as sintering, raw material handling, coke ovens, and blast furnaces. In the steelmaking process, compressed air is utilized for continuous casting, converter pneumatic operations, purging, and mist cooling during casting.
Within the hot rolling mill, compressed air is employed in mill and furnace pneumatic equipment, as well as for cold rolling purging. It is also used for strip cleaning, pickling, continuous winding, and various pneumatic equipment in addition to hot-dip galvanizing processes. Furthermore, blast furnaces and coal injection for combustion require a substantial amount of compressed air.
Regarding the quality requirements of compressed air in iron and steel enterprises, they are generally not excessively demanding. While some compressed air used in instrumentation may require refrigerated dryers for precise treatment, most of the compressed air does not necessitate highly accurate processing.
In response to the extensive needs of the iron and steel industry, ELANG’s two-stage permanent magnet machine has gained high acclaim due to its large gas volume and low energy consumption. Similarly, the ELANG two-stage screw air compressor provides larger airflow, ensures stable operation, produces less noise, and is thus the preferred choice for the iron and steel industry, even when compared to other compressors with the same power.