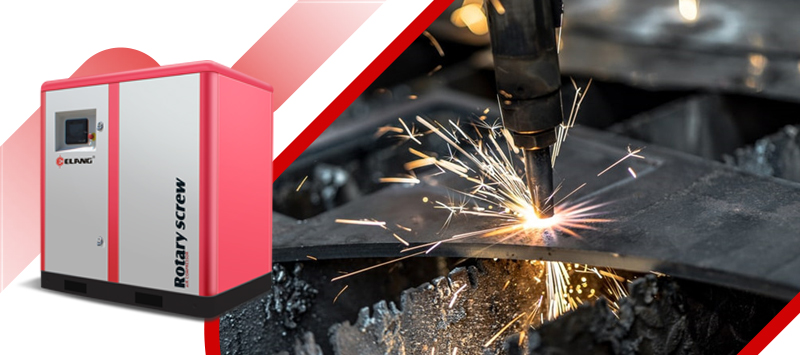
Plasma cutting is a metal processing method that utilizes high-temperature plasma to cut metal materials. It is an important metal cutting technique widely used in metal fabrication, manufacturing, automotive, aerospace, and other industries.
The gas requirements for plasma cutting
The gas requirements for plasma cutting typically involve two aspects: cutting gas and assist gas.
Cutting gas
Common cutting gases include oxygen, nitrogen, and air. These gases serve the following purposes in the plasma cutting process:
Oxygen (O2): Widely used for cutting carbon steel and alloy steel. It reacts with the metal in the cutting area, causing oxidation reactions and providing an oxidizing agent to facilitate metal melting and gas blowing.
Nitrogen (N2): Primarily used for cutting stainless steel and aluminum. Its main role is to cool and clean the cutting area, reduce oxidation reactions, and prevent oxidation of stainless steel and aluminum.
Air: It can be used as an economical cutting gas, consisting of a mixture of oxygen and nitrogen. However, air may not be suitable for some specific applications due to the presence of other components such as moisture and impurities.
Assist gas
In some cases, plasma cutting may require the use of assist gases, such as:
Oxidizers: Used to enhance the action of oxygen during the cutting process, improving cutting speed and quality. Common oxidizers include methane (CH4) and acetylene (C2H2).
Argon (Ar): Used to shield the plasma arc and cool the electrode. Argon stabilizes the arc and provides a cooling effect to prevent electrode overheating.
The selection of appropriate cutting and assist gases depends on the type of material being cut, the thickness, and the desired cutting quality. When using gases, it is important to ensure their purity and quality meet the manufacturer’s recommendations and requirements. Additionally, safety considerations such as proper ventilation and monitoring for gas leaks should be observed to ensure safe operation. It is advisable to consult the guidelines and recommendations provided by the plasma cutting machine manufacturer when selecting and using gases.
The requirements for an air compressor in plasma cutting systems
Pressure requirement
Plasma cutting requires high-pressure gas as the cutting medium. The specific pressure requirement depends on the specifications and requirements of the cutting machine. Typically, the working pressure ranges from 100 psi to 135 psi, and the output pressure can be adjusted using a pressure regulator. Large automatic plasma cutting systems within the range of 130 to 800 amps may require a pressure of 115 psi (8 bar) or higher. Therefore, when selecting an air compressor, it is necessary to ensure that it can provide sufficient pressure output to meet the requirements of the cutting machine.
Flow rate requirement
Plasma cutting requires a significant amount of gas flow to maintain the plasma arc and high-speed airflow during the cutting process. As a rule of thumb, the selected flow rate should be at least 1.5 times the consumption rate of the plasma cutting machine. It is also important to ensure that the hoses or pipes used are rated for the system’s handling pressure, have a diameter large enough to accommodate the required flow rate, and do not corrode or generate excessive moisture within the pipeline. The orifice size of all connections used should match the inner diameter of the hoses or pipes. Flow rate requirements can vary depending on the system. Based on your system requirements, you will need a flow rate between 3.5 scfm (99 liters/minute) and 6.7 scfm (189 liters/minute). Therefore, when selecting an air compressor, it is crucial to ensure that it can provide sufficient gas flow to meet the requirements of plasma cutting.
Stability and reliability
Plasma cutting requires a high level of stability and reliability from the air compressor. A consistent and reliable gas supply is essential to ensure cutting quality and efficiency. Therefore, it is crucial to choose an air compressor with good stability and reliability.
Air quality
Plasma cutting has certain requirements for gas purity and oil content. Some cutting processes require high-purity gas with strict limitations on oil content. The design and layout of the compressed air system have a significant impact on the amount of retained moisture and its final destination in the system. In this regard, it is advisable to consider an air compressor system equipped with gas filters and oil separators, and to use air filtration devices to remove water, oil, and debris from the air supply. Place them as close as possible to the plasma cutting system. In most cases, a standard coalescing filter with an automatic drain is sufficient. If cutting in high humidity environments, a refrigerated air dryer should be considered.
When choosing an air compressor suitable for a plasma cutting machine, factors such as pressure, flow rate, stability, and air quality need to be considered. It is best to refer to the recommendations and requirements of the plasma cutting machine manufacturer to ensure that the selected air compressor meets the technical requirements and performance needs of plasma cutting.