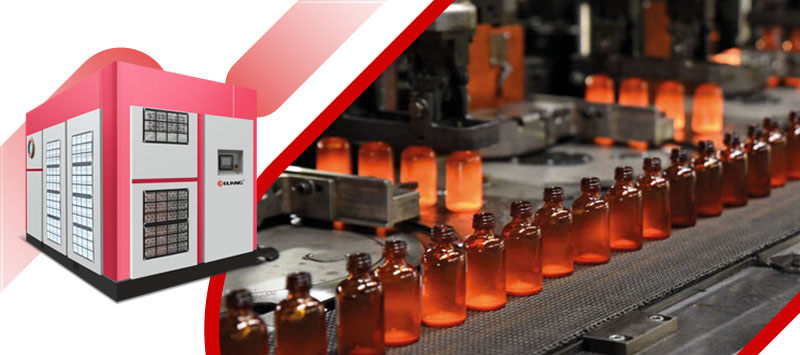
In the realm of plane glass manufacturing, compressors play a pivotal role in ensuring the efficient and seamless production of this versatile material. Compressors drive pneumatic machinery, facilitating the transfer of raw materials, maintaining optimal temperatures, and enabling the formation and cutting processes.
What are the uses of air compressors in plane glass manufacturing?
Raw Material Transfer
The production of plane glass begins with the extraction of sand from large silos. Compressors, particularly rotary screw compressors, provide the necessary compressed air to power pneumatic machinery that transports the sand from the silos to the adjacent glass factory. This streamlined transfer process ensures a steady supply of raw materials for glass production, enhancing efficiency and reducing downtime.
Melting and Mixing
Once the raw materials, including sand, are delivered to the glass factory, they undergo a melting and mixing process. The mixed raw materials, including silica sand, pass through a series of tank chamber funnels. Compressors drive conveyors, guiding the mixture from one chamber to another. The compressed air generated by the compressors helps create a controlled and consistent flow of materials, ensuring uniform melting and thorough mixing.
Forming and Shaping
In the forming stage, the molten material is transformed into glass. Compressors continue to play a crucial role in this process. Pneumatic tools, powered by compressors, are used to cool the molten glass to the ideal temperature for shaping. Compressed air aids in reducing the temperature, making the glass plate firm and facilitating its manipulation into various forms, such as flat sheets or unique shapes for glass bottles.
Cooling and Hardening
After the glass is shaped, it undergoes a cooling process to achieve its desired properties. The high initial temperature of the glass makes it flexible and susceptible to distortion. Compressors, along with pneumatic blowers, are employed to blow compressed air onto the glass surface, rapidly reducing its temperature. This controlled cooling ensures the glass plate hardens evenly, becoming transparent, flat, and rigid.
Cutting and Finishing
Once the glass has cooled and hardened, it is ready for the cutting stage. Compressors continue to power the pneumatic machinery used for precise cutting and shaping of the glass. The compressed air enables the smooth operation of cutting tools, ensuring accurate and clean cuts, whether it is piece by piece or continuous cutting for large glass sheets.
Compressors are integral to the plane glass production process, facilitating the efficient transfer of raw materials, controlling temperatures, and powering pneumatic tools and machinery. They contribute to the overall speed, precision, and quality of glass production, enabling manufacturers to meet the growing demand for flat glass in various industries. By recognizing the crucial role of compressors, we appreciate their significance in making glass production a seamless and sustainable process.
How to configure the air compressor in the plane glass industry?
Configuring the air compressor in the plane glass industry requires careful consideration of various factors to ensure optimal performance and efficiency.
Determine Air Demand
Assess the air demand requirements of the plane glass production process. Consider factors such as the size of the glass factory, the number and types of pneumatic tools and machinery, and the expected production volume. This analysis will help determine the required capacity and pressure of the air compressor.
Select the Right Compressor Type
Based on the air demand assessment, choose the appropriate type of compressor for the plane glass industry. Common types include rotary screw compressors and reciprocating compressors. Rotary screw compressors are often preferred due to their continuous operation, higher efficiency, and lower maintenance requirements.
Size the Compressor
Properly sizing the compressor is crucial to meet the specific air demand of the glass production process. Consider factors such as the required air pressure, flow rate, and duty cycle. Oversized compressors can lead to energy wastage, while undersized compressors may result in insufficient air supply and decreased productivity.
Install an Air Receiver Tank
Install an air receiver tank in the compressed air system. The receiver tank acts as a buffer, storing compressed air and helping to stabilize pressure fluctuations. This ensures a steady and consistent air supply, reducing strain on the compressor and promoting efficient operation.
Consider Air Treatment
Plane glass production often requires clean and dry compressed air to avoid any contamination or damage to the glass. Incorporate appropriate air treatment equipment such as filters, dryers, and condensate management systems to remove moisture, oil, and particulate matter from the compressed air.
Plan Piping and Distribution
Design an efficient compressed air piping system that ensures proper air distribution to various points of use. Use materials and sizes suitable for the required flow rates and minimize pressure drops. Consider implementing isolation valves and pressure regulators at critical points to optimize air supply to specific processes.
Implement Controls and Monitoring
Integrate control systems to monitor and manage the air compressor operation. Use sensors, pressure gauges, and energy management systems to track performance, detect any abnormalities, and optimize energy consumption. Regularly monitor and maintain the compressor to ensure its efficiency and longevity.
Regular Maintenance and Training
Establish a maintenance schedule for the air compressor, including regular checks, lubrication, and filter replacements. Train personnel on proper operation, maintenance, and safety procedures to maximize the lifespan and performance of the compressor.
By following these steps and considering the specific requirements of the plane glass industry, you can effectively configure the air compressor system to support efficient and reliable glass production processes.