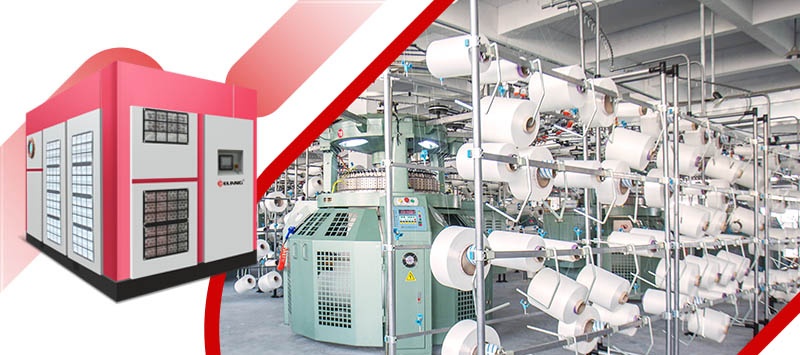
Compressed air is an important power source for the production of modern textile enterprises. There are many processes in textile production, and the requirements for compressed air in each process are different. Therefore, how to reasonably select and match the air compressor to make the compressed air meet the production process needs of each process is an important factor related to whether the production of modern textile enterprises can be carried out normally. The selection of air compressor should ensure to meet the different requirements for compressed air of various process equipment in textile production.
1. Air jet looms are the equipment with the largest air consumption in the textile industry. At the same time, compressed air is also needed for air wrapping machines and texturing machines; Compressed air is also needed for chip drying and transportation in the chemical fiber industry.
2. To ensure the quality of compressed air, not only weft insertion can be normal, but also the stable operation of air-jet loom and the hygienic condition of operating environment should be ensured. Generally, the compressed air source that meets the requirements of air-jet loom can be used by the process equipment of each textile process as long as it meets the needs of service pressure. By referring to the use requirements of various air-jet looms, the quality indexes of compressed air required mainly include:
Effectively remove liquid water and gaseous water as much as possible, and the pressure dew point value is below 8 ℃;
Pure and oil-free clean air;
Remove 0.1 μ Dust and toner particles above;
The textile industry has a large production scale. If the compressed air transmission distance is long, it is necessary to configure the calculated pipeline and select the model with corresponding exhaust pressure. Generally speaking, the power of air compressor used in knitting, spinning and air-jet loom is slightly different.
According to the characteristics of long running time, large gas consumption, low air pressure and many cotton wadding in the textile industry, combined with the requirements of stable air source, clean and oil-free, the permanent magnet single-stage low-speed low-pressure series, permanent magnet two-stage low-pressure series and intelligent permanent magnet variable-frequency screw air compressor launched by Elang are ideal choices. In the post-treatment equipment, precision filter and cold dryer are configured for purification treatment, Only in this way can we ensure the stability of production and minimize the harm to textile equipment products.
Whether you are adding a new air compressor or replacing and transforming an old air compressor, from the energy consumption test of the old model, the site selection of the air compressor room, pipeline layout, model configuration, post-treatment equipment combination, Elang customizes the aerodynamic scheme for enterprises in the textile industry, which is installed and debugged by a professional installation technical team.