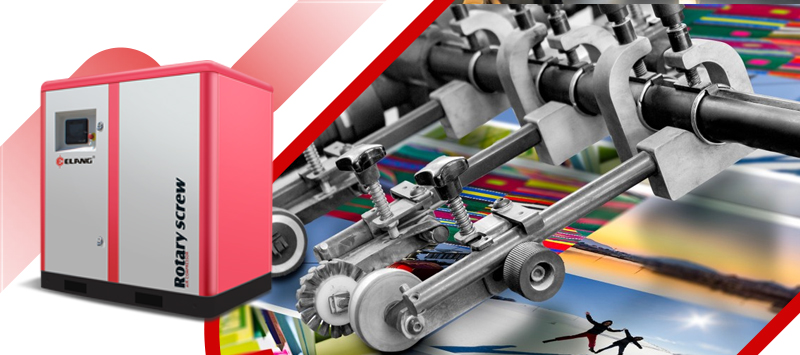
Paint sprayers are widely used in various industries for different applications that demand efficient and precise paint application. These industries include the automotive industry, construction and architectural industry, furniture manufacturing, and various other industries. Nevertheless, to meet the requirements of these highly specialized tasks, it is essential to have an appropriate air compressor that can deliver the necessary pressure and compressed air volume.
Which industries require the use of screw compressors for spray painting?
Screw compressors excel in spray applications that demand high airflow and consistent pressure. They are essential in industries such as automotive manufacturing, aerospace, and large-scale industrial production, where the requirements for spray painting are stringent. Conversely, for most applications like wall or vehicle painting, where the spray gun’s air consumption is relatively low, typically ranging from 7-15 cfm, a small piston compressor is usually adequate for the job. Consequently, screw compressors find widespread application in industries that undertake extensive spray painting tasks on a large scale.
Automotive Industry
The automotive industry extensively utilizes spray painting for vehicle bodies, parts, and components. Screw compressors are indispensable in automotive painting facilities, where large volumes of compressed air are needed to power paint guns and ensure smooth and uniform paint coverage.
Aerospace and Aviation Industry
Aircraft manufacturing and maintenance involve intricate and precise spray painting processes. Screw compressors provide the necessary high flow rates and stable pressure required for painting aircraft surfaces, ensuring excellent paint adhesion and a flawless finish.
Industrial Manufacturing
Various industrial manufacturing sectors, such as machinery, equipment, and metal fabrication, rely on spray painting for product finishing. Screw compressors offer the capacity to meet the high air demand of industrial spray painting booths, enabling consistent and efficient paint application on a large scale.
Furniture Manufacturing
Furniture production involves painting surfaces to enhance their aesthetics and protect them from wear and tear. Screw compressors deliver the air volume and pressure required for spray guns in furniture painting workshops, ensuring even paint distribution and a professional-looking finish.
Construction and Architectural Industry
Spray painting is commonly used in construction projects and architectural applications, such as painting walls, ceilings, and structural elements. Screw compressors provide the necessary air power for paint sprayers, allowing for efficient and uniform paint coverage on large surfaces.
Marine Industry
Shipbuilding and maintenance often involve extensive surface preparation and painting. Screw compressors are utilized to provide the required air supply for marine painting applications, ensuring the durability and protection of vessels against harsh marine environments.
What are the requirements of screw compressors in the painting industry?
Flow requirement
The spray painting process requires a significant amount of compressed air flow to provide stable spraying operations. When selecting a screw compressor, it is important to ensure that it can deliver sufficient flow to meet the requirements of the spray painting equipment. The required flow range should be determined based on the consumption rate of the spray gun and the operational needs. If the CFM rating of the compressor is not higher than the CFM requirement specified on the spray gun, the spray coverage will be inconsistent and unstable.
Pressure requirement
Spray painting operations require a certain level of pressure to achieve uniform and high-quality spraying results. When selecting a screw compressor, it is essential to ensure that it can provide stable working pressure and meet the pressure range required by the spray painting equipment. The ideal PSI requirement in spray painting can sometimes rise to 40 PSI or higher in certain cases.
Stability and reliability
Spray painting operations have high requirements for the stability and reliability of the air compressor, as a continuous and stable supply of compressed air is crucial for spray painting quality. When purchasing a screw compressor, it is important to choose a brand and model that has good stability and reliability.
Noise control
In the workplace, reducing noise is crucial for the health and working environment of employees. Choosing a screw compressor with a low-noise design can help reduce noise pollution and its impact on workers.
Maintenance and After-sales Service
In the printing industry, it is important to pay attention to regular maintenance when using air compressors, such as timely removal of dust and timely replacement of precision filters. The lifespan of precision filters is generally around 2000 hours, but it may be slightly shorter in the printing industry. When choosing manufacturers or suppliers, it is necessary to consider the after-sales service and support they provide, including repair services, spare parts availability, and technical support.
Elang’s tailored air solutions have become an indispensable asset in resolving air supply challenges in the painting industry. With a focus on meeting high air demand, maintaining stable pressure, enhancing reliability and performance, reducing noise emissions, and providing comprehensive after-sales support, Elang enables painting professionals to achieve efficient and high-quality paint application. By choosing Elang, businesses in the painting industry can optimize their operations, enhance productivity, and deliver exceptional results.