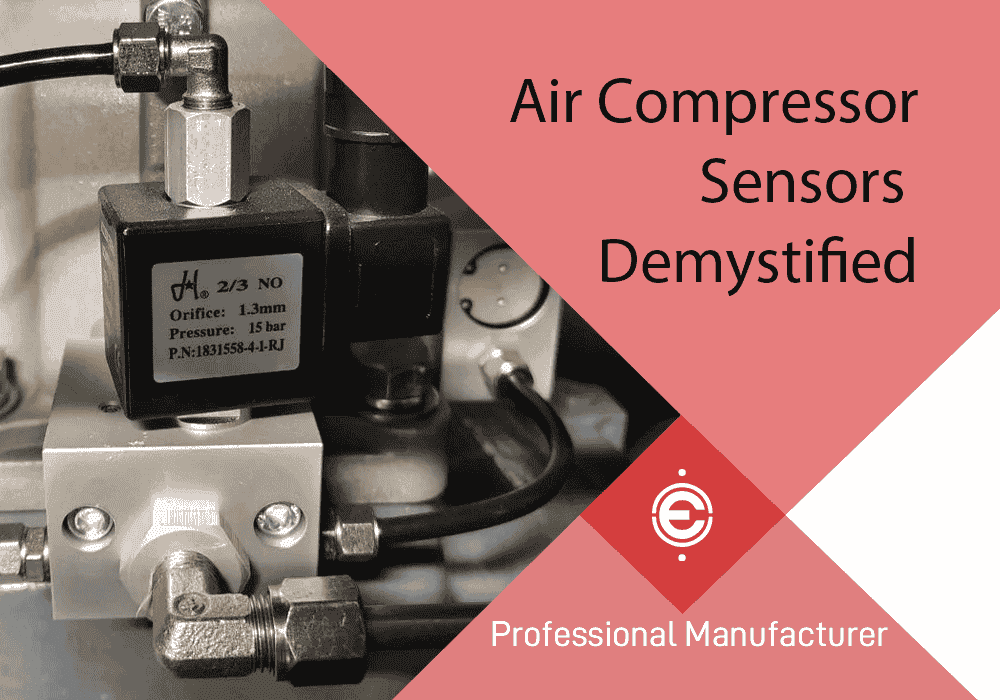
- Air Compressor Sensors
- Why Are Sensors the “Eyes and Ears” of an ?
- What Exactly Are These Little Helpers—Air Compressor Sensor—Busy Doing?
- Temperature Sensors: The “Thermometer” Doctor for the Machine
- Pressure Sensors: The “Scales of Justice” for Air Pressure
- Differential Pressure (ΔP) Sensors: The Filter’s “Health Alarm Clock”
- Vibration Sensors: The Fault-Finding “Sherlock Holmes”
- Current / Voltage Sensors: The air compressor Motor’s “Minder”
- Level Sensor: The Oil Tank’s “Dry-Run Prevention Alarm”
- Dew Point Sensor: The Air’s “Dryness Quality Inspector”
- How Do All These Sensors Work Together to Handle Big Tasks?
- The Investment Case for Sensors: Short-Term Cost, Long-Term Protection!
- Final Reminder:
Discover how air compressor sensors transform screw compressors from blind operators to intelligent systems. Temperature, pressure, vibration, and other air compressor sensors act as the machine's "eyes and ears," enabling real-time monitoring, predictive maintenance, and 30%+ energy savings. This article reveals why these unassuming components are critical for reliability, cost reduction, and seamless industrial operations.
Air Compressor Sensors
These unassuming little components(air compressor sensors) are far from decorative; they are highly effective efficiency managers and money-saving experts.
Why Are Sensors the “Eyes and Ears” of an Screw Air Compressor?
Think of it this way: Older air compressors were like driving blindfolded, relying solely on experience to guess conditions, only hitting the brakes when a problem occurred. But with air compressor sensor, it’s like equipping the machine with an intelligent navigation system. They continuously monitor every internal state, providing early warnings of risks, enabling the compressor to run as smoothly as a seasoned driver navigating the road!
What Exactly Are These Little Helpers—Air Compressor Sensor—Busy Doing?
Temperature Sensors: The “Thermometer” Doctor for the Machine
What they manage: Monitor lubricating oil and discharge air temperature, essentially taking the machine’s temperature.
Importance: High oil temperature causes oil to “deteriorate,” drastically increasing wear on critical components like the airend (akin to unlubricated gears). High discharge temperature can cause downstream dryers to go on “overheat shutdown.” Once these air compressor sensors sound an alarm, the system instantly initiates cooling – faster than a human can react!
Pressure Sensors: The “Scales of Justice” for Air Pressure
What they measure: Intake pressure, discharge pressure, and the pressure differential (ΔP) across the internal oil-air separator.
Why it matters: Unstable discharge pressure makes the production line “breathe” erratically. A large pressure differential signals that the filter element needs replacing; neglecting it wastes electricity noticeably. These air compressor sensors, when used in conjunction with a frequency converter, provide “air on demand”, directly eliminating the energy (and cost) wasted by idling!
Differential Pressure (ΔP) Sensors: The Filter’s “Health Alarm Clock”
Responsibility: Monitor whether air filters and oil filters are clogged.
Importance: A clogged air filter makes the machine “struggle to breathe,” reducing power and increasing energy consumption. A clogged oil filter causes lubricant to get “lost,” doubling wear on the airend. This air compressor sensor signals exactly when it’s time to change your filter – not too early, not too late – saving money and protecting your machine!
Vibration Sensors: The Fault-Finding “Sherlock Holmes”
Capability: Detect the vibration “rhythm” of the airend and motor.
Importance: Small issues like bearing wear or loose bolts first “reveal” themselves through vibration changes. Like a detective, this air compressor sensor picks up on anomalies, ensuring small problems are fixed before they become big (and expensive) problems!
Current / Voltage Sensors: The air compressor Motor’s “Minder”
What they monitor: Ensure the motor’s current and voltage levels are normal.
Critical Role: Abnormal current can overload and burn out the motor. Unstable voltage is like making the motor “drink cold water” – harmful. They protect core components and enable precise energy consumption calculation, making energy management crystal clear!
Level Sensor: The Oil Tank’s “Dry-Run Prevention Alarm”
Responsibility: Keep an eye on whether there’s enough lubricating oil in the tank.
Importance: Unnoticed low oil leads to the airend running “dry,” causing damage with repair costs that could make you cry! This air compressor sensor acts as a safety latch, instantly calling for “refill!” when oil is low.
Dew Point Sensor: The Air’s “Dryness Quality Inspector”
Responsibility: Measure the dryness level of the compressed air (via dew point temperature).
Importance: Excessively humid air corrodes pipelines, affects painting quality, and can even cause equipment to “rust and shut down.” It ensures the air delivered to the workshop is more reliable than desiccant!
How Do All These Sensors Work Together to Handle Big Tasks?
Elang’s intelligent control system acts like the “central brain,” aggregating and analyzing all sensor data:
Visible Energy Savings: Pressure sensors report demand; the controller commands the frequency converter for “air-on-demand.” The energy wasted by traditional machines constantly “gasping” (loading/unloading) is now entirely saved!
Smarter Maintenance: Records trends in temperature and vibration. For example, if vibration gradually increases, the system prompts “check bearings,” transforming reactive breakdown repairs into proactive maintenance, cutting downtime losses by half!
Effortless Management: Remotely monitor pressure, temperature, and energy costs via mobile phone. Export reports for crystal-clear visibility – clearer than flipping through logbooks!
The Investment Case for Sensors: Short-Term Cost, Long-Term Protection!
Save on Electricity: Frequency conversion control delivers immediate energy savings; the reduced electricity bill quickly “pays back” the sensor investment.
Longer Machine Life: Early anomaly detection extends the lifespan of the airend and motor, lengthening intervals between major overhauls.
Less Downtime: Predictive maintenance prevents sudden machine “strikes,” directly eliminating production line stoppage losses.
Lower Maintenance Costs: Change filters based on actual need – no waste. Fix small problems early – avoid major repair bills.
Stable Production: Stable air pressure, dry air, reliable air supply – leading to stable product quality!
Final Reminder:
These sensors act like an “intelligent neural network” for your air compressor, transforming it from “working blindly” to “operating intelligently.” Elang’s commitment to investing in core functionality aims to make your equipment economical to run, long-lasting, and worry-free. Choosing Elang means choosing a “compressed air solution that saves you money by itself” – you focus on production, leave efficiency and costs to us!