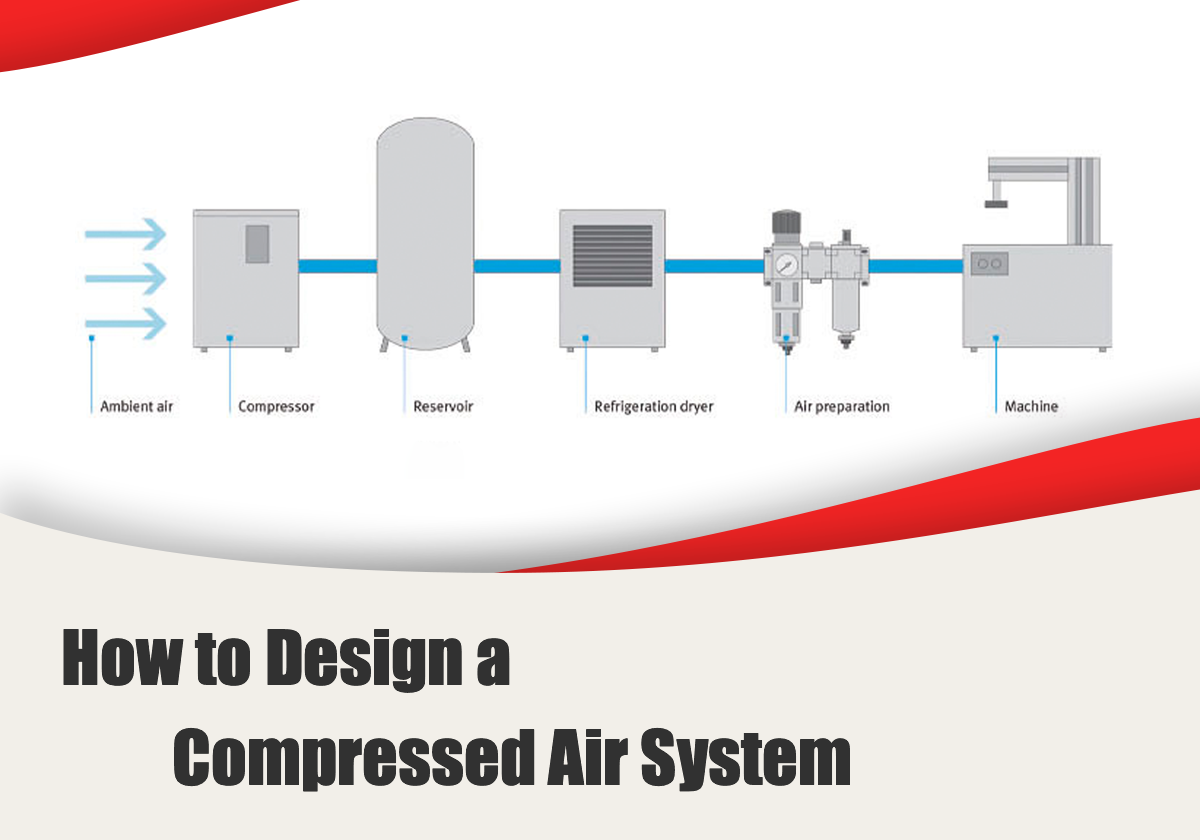
This article will guide you through the fundamental steps of designing a compressed air system, from assessing needs to selecting system components, and ensuring maximum energy efficiency, offering a comprehensive compressed air system design guide.
Compressed air system design is key to significantly enhancing production efficiency and saving substantial amounts on operational costs for businesses. Compressed air is an indispensable power source in industries such as manufacturing, construction, or energy. Therefore, designing a system that meets current needs while being adaptable to future expansions presents a challenge for engineers and project managers alike.
1. Components of a Compressed Air System
A basic compressed air system consists of compressed air equipment, after treatment equipment, and conveying pipes, as shown below:
-
Compressed Air Equipment
Compressed air equipment, which include various types of air compressors, serves as the device for generating compressed air. Among the most common types of air compressors are the single screw, double screw, reciprocating piston, centrifugal models, and so on.
-
After Treatment Equipment
After treatment equipment includes the devices that dry, purify, and regulate the pressure of compressed air produced by compressed air equipment, ensuring it meets the quality requirements by end-users. These devices, which vary in function and features, should be configured flexibly according to the specific air demand. They include dryers, filters, air tanks, oil-water separators / gas-water separators, components of after treatment system, pressure regulating valves, drain valve and more.
-
Pipeline System
In industrial and mining factories, a more complete compressed air system consists of an integrated subsystem of components, which include air compressors, purification equipments, control devices, piping systems, pneumatic tools, pneumatic machines, and processes that use compressed air.
2. Compressed Air Solutions and Equipment Selection
When users request compressed air, it is essential to comprehensively consider their requirements, production processes, investment scale, engineering conditions, and other factors in order to propose appropriate selection solutions. This enables the design of compressed air systems that are best suited to the customer’s own project requirements.
2.1 Determine Compressed Air Solution
Based on factors like project scale, distribution of usage points, supply pressure levels, and the quality requirements of compressed air, several compressed air solutions are generally considered for their cost-effectiveness:
-
- Centralized compressed air supply solutions involve establishing dedicated compressed air stations. These are mainly suitable for small to medium-scale factories or those with concentrated compressed air needs in large factories.
-
- Regional compressed air supply solutions are often adopted in projects with large scales, high compressed air demand, and dispersed major users to reduce pressure loss in the pipeline network and ensure supply to critical points.
-
- Local compressed air supply solutions can be considered when a factory has low compressed air demand, few end-user points, and those are scattered. Compressors can be placed near these points.
-
- Combined centralized and decentralized compressed air supply solutions are suitable for some large and medium-scale factories. This is particularly applicable when the main air consumption points are concentrated, while the secondary air consumption points are scattered, especially with lower air consumption points during the night.
-
- Tiered compressed air supply solutions are suitable when different pressure levels of compressed air are required, and there are significant demands for both high and low pressures. Using air compressors of varying pressure levels while avoiding pressure reduction can help prevent energy wastage. Ideally, the supply pressure should be limited to two levels.
- Centralized compressed air supply with local enhancement solutions involve ensuring high-quality air supply at specific points through the use of high-quality compressed air equipment (such as oil-free air compressors) or advanced after-treatment equipment located nearby. The choice among these solutions should be based on a comprehensive comparison of air consumption and the locations of end-user points.
In summary, determining the compressed air solution requires comprehensive consideration, including factors such as users’ initial investment, production process management, particularly for users expanding production and increasing air consumption or end-user points. In addition, the original compressed air system design (layout) needs to be taken into account, e.g. electrical wiring, airways. It is important to note that certain types of air compressors may require specific installation bases or compressor stations. Therefore, these solutions require specific analysis for each unique situation.
2.2 Determine The Air Consumption
There are two ways to determine the air consumption.
-
- Building a New Compressed Air System
For new factories or newly constructed compressed air systems, determining the air usage mode is relatively straightforward. It involves calculating the total air consumption based on the requirements of end-user equipment. However, it’s crucial to differentiate between the demand pressure and the quality requirements of the compressed air. Air consumption patterns can generally be categorized into three types: continuous, intermittent, and instantaneous usage. Continuous usage implies constant air utilization, with the total consumption being easily calculated by summing up the usage. Intermittent usage refers to periodic short-term air usage. Instantaneous usage represents an extreme case of intermittent usage, characterized by long intervals between uses but requiring a large amount of air at once. Typically, to meet such demand, a larger air tank is needed. Estimating the required compressed air flow rate involves dividing the single-use air consumption by the interval time.
- Building a New Compressed Air System
- Increased Compressed Air Demand After Capacity Expansion
There are two situations to consider: significant and slight increases in air consumption. The former may result from the addition of multiple identical production lines, directly impacting air consumption per production line or according to new processes. The latter typically necessitates a new compressed air system due to insufficient air pressure. This could stem from the addition of extra pneumatic equipment, reduced compressor performance, or increased equipment air consumption due to wear and tear.
2.3 Selection and Combination of Air Compressor Models
This mainly involves two parts, one is the selection of air compressors, and the other is the selection of after treatment equipments. These two parts are pretty connected, often hand-in-hand. Basically, the selection of compressed air equipments will affect the selection of after treatment equipments.
- Technical indicators that the product should achieve
It mainly includes air flow, pressure, power and application range of variable conditions, safety and so on. Safety’s usually not a big concern with air compression. The first thing to consider in the selection of models is whether the pressure meets the demand, followed by the air flow (here involves the configuration of the size and number of models, the main consideration is to adapt to different flow requirements through reasonable model configuration), for the powered compressor, it is more necessary to consider the load reduction, the compressor’s ability to change the working condition. - The Requirements of Compressed Air Quality
The initial investment of compressed air system only accounts for a small part in the whole service life cycle of equipment, with approximately 70% being energy consumption. Therefore, the efficiency of the compressor is crucial to the investment cost. The energy efficiency level is determined based on the specific power of the unit, in kW /(m3/min), and the smaller the value, the better the energy efficiency. Unit specific power value is divided into 1, 2, 3 energy efficiency levels, level 1 is the best energy efficiency level.
Note: in addition to the energy efficiency level of the air compressor itself, factors such as appropriate model configuration, selection of after-treatment equipment, pipeline configuration, and operating modes also affect the overall energy efficiency level of the compressed air system. - The Combination of Different Models
For the model selection of the new demand, special consideration should be given to the cooperation with the existing models, and the overall level of the compressed air system should be considered from the whole plant. If necessary, it is a responsible attitude to the user to upgrade the original system. When the original air compressor is installed in the same station, attention should be paid to the airflow pulse problem of the reciprocating air compressor, and the reciprocating compressor outlet pipe should be installed with a check valve, which is connected with other compressor pipes after passing through the air tank. If the original compressed air pipe is still used, attention should be paid to whether the pipe diameter is sufficient. Similarly, the power load is also a factor that needs to be considered, and the station low-voltage switchgear hollow open should correspond to the compressor equipment one by one, not allowed to share.
3. After Treatment Equipment
After Treatment Equipment mainly includes dryers, filters, air tanks, etc.
- dryers
Including refrigerated drying machine and adsorption drying machine two kinds, its role is to separate the gaseous moisture in the compressed air, the principle of action is equivalent to the air conditioning, will be highly heated compressed air through the refrigerant compressor down to the dew-point temperature, to release the compressed air in 99% of the water. - filters
The function is to filter out the maximum amount of dust and oil from the compressed air.
Set up these devices, the final compressed air is very clean, very dry, to meet more than 90% of the enterprise’s air needs, if special industries, such as medical food and other imported products, then you need to be equipped with a full oil-free air compressor, or add a multi-filtering device, such as de-bacteria, deodorant, and so on.
4. Selection of Compressor Station and Pipeline
When determining the compressed air solution, it is necessary to consider whether to use an air compressor station, which is not free to design, but has the agreement of relevant standards and specifications.
- An air tank should be installed behind piston air compressors and diaphragm air compressors, with an aftercooler positioned between the air outlet and the air tank. It’s important to note that piston air compressors or diaphragm air compressors should not share aftercoolers and air tanks. Additionally, besides any special temperature requirements from the user for the compressed air, an aftercooler should be installed at the exhaust port of the centrifugal air compressor.
- When the air compressors of different pressures are operated in series, an air tank should be installed between the two compressors, with another air tank placed downstream of the last compressor. The volume of the air tank should be matched based on the balance of inlet and exhaust flow between the high and low pressure compressors.
- A check valve must be installed between the piston air compressor, diaphragm air compressor, and the air tank. Additionally, a vent pipe should be provided between the air compressor and the check valve, with a muffler installed on the vent pipe. The piston air compressor, diaphragm air compressor, and the air tank should not have shut-off valves installed between them. If a shut-off valve is required, it must be installed between the air compressor and the safety valve.
- The exhaust system of the centrifugal air compressor should include both a check valve and a one-way valve. These components must be positioned between the air compressor and the one-way valve. Additionally, the vent pipe should be fitted with an anti-surge valve and a silencer for optimal operation.
- The centrifugal air compressor should be set up with a high-level oil tank or other facilities that can ensure that the oil supply of the machine is changed.
- A safety valve must be installed on the air tank. A one-way valve should be installed between the air tank and main air supply pipe.
- In a compressed air station with a working pressure of ≥10MPa, the air distribution table, air tank, and bottle filling device should be placed in separate rooms, with no unrelated equipment allowed in those rooms.
- The coupling and belt drive part of the air compressor unit must be equipped with safety protection facilities.
- When a compressed air station with a working pressure of ≥10MPa is adjacent to other buildings, the dividing wall should be a reinforced concrete protective wall without any doors, windows, or openings. The thickness of this protective wall should be no less than 200mm.
- The doors leading to the outside between the machines of the compressed air station should ensure safe evacuation, easy access to the setting and operation management. The safety exit of the centrifugal air compressor station should not be less than 2, and there must be 1 direct outdoor; When the double-layer arrangement, the operating layer should lead to the outdoor ground safety ladder.
- The voltage of the hand lamp used in the compressed air station should not exceed 36V; The voltage of the hand lamp used on the metal platform of the air compressor inside the air tank should not exceed 12V.
- The thermal alarm signal and automatic protection control device of the compressed air station should be installed according to the regulations. When there is a central control room, the thermal alarm signal should be connected to the centralized control room. The emergency stop button for air compressors should be set up in the control room and beside the machine.
- The centrifugal air compressor should be set up the following control system: intake air regulation control system; Unit anti-surge control system; Exhaust pressure control system or steady flow control system.
- Compressed air stations with a working pressure ≥3.2MPa should not be located in basements, semi-basements, or within floors of buildings. The machinery and air tanks should be arranged on a single level, and no unrelated equipment or facilities should be installed within the same area.
5. Installation Notes
When installing an air pressure station, there are two points that require special attention, the first being the air compressor, storage tank, dryer, and filter. The distance between each piece of equipment must be placed, the distance between the air compressor and the storage tank is best not less than 50 cm, because the connection method of the storage tank follows the reason that the low mouth in, the high mouth out, then, the distance between the storage tank and the primary filter is best not less than 40 cm, between the primary filter and the drying machine is not less than 40 cm, and the drying machine and the back of the fine filters are also best to reach 40 cm or more, because the distance is too small, will give the future maintenance of the equipment to bring trouble; the second point is to place these devices, and the air compressor room on all sides of the wall of the straight line distance to save at least 100 cm, which is also for the convenience of the future maintenance of the equipment to stay at least the distance of the space, as well as the air compressor room to maintain good ventilation, when necessary, add an exhaust fan, to do all this is in order to maximise the play of the air station’s All these are done to maximise the role of the air compressor station and to ensure the maximum service life of the air compressor.
Our Case
Related Reading
Under the background of the increasing awareness of global environmental protection, how to achieve high efficiency and energy saving of industrial production has become an important issue faced by the majority of enterprises.
An air compressor room that meets the standards needs to include multiple factors such as fire prevention, environment, and layout.