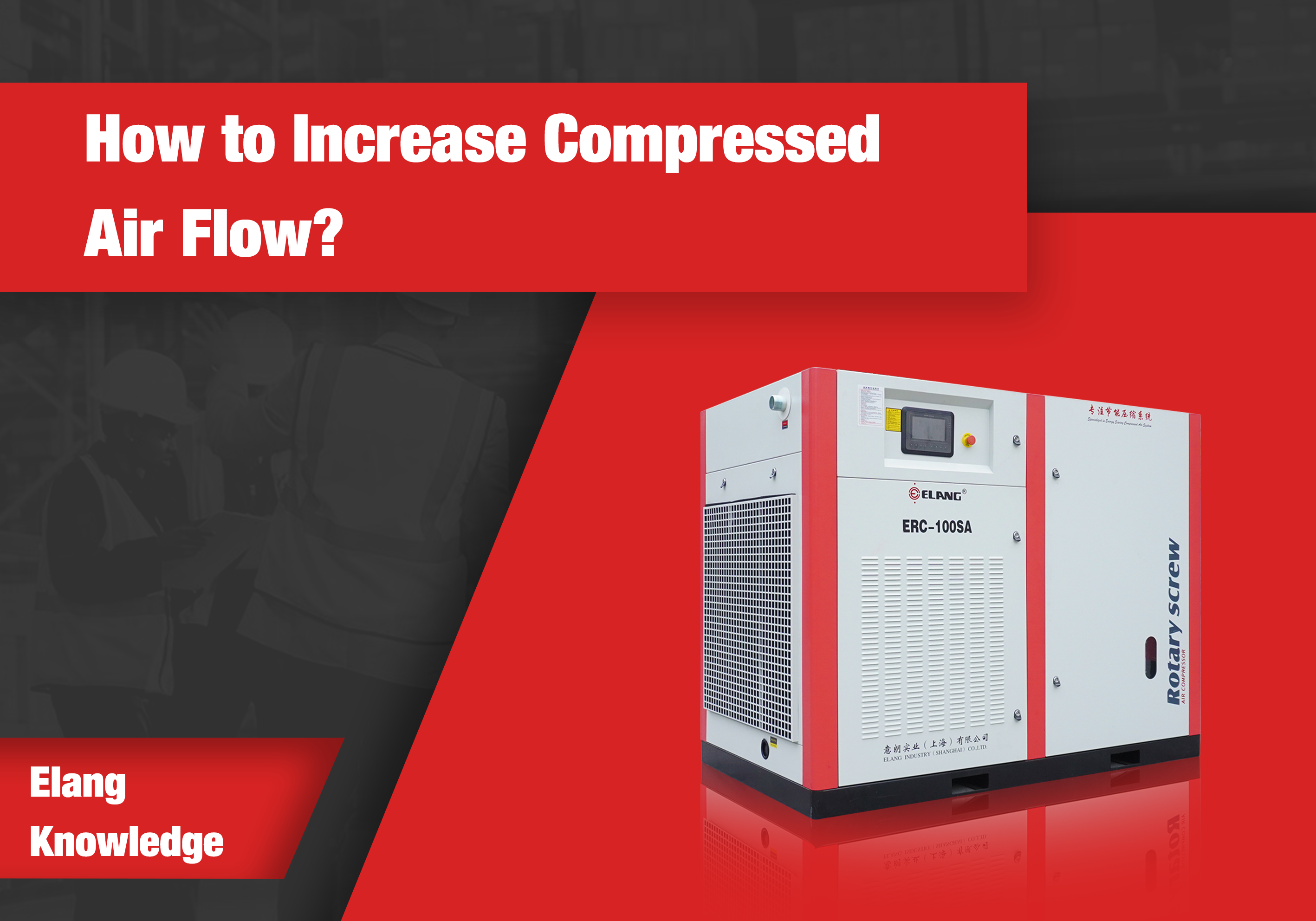
We often receive requests from a large number of customers who hope to add new compressor equipment. Many of these customers are prompted by internal clients, such as production workshops, presenting a pressing concern: poor air flow.
How to solve the problem when customers complain about insufficient air flow?
Although the quality of compressed air may be influenced by various factors, the frequently mentioned problems might not be immediately evident. When a compressed air system experiences pressure drops during high-flow and intermittent applications, pinpointing the root cause is often challenging; instead, we tend to react to and mitigate this impact. A typical (and often incorrect) assumption is inadequate air supply.
A common method to solve this problem is to adjust the supply air pressure of the entire system to be sufficiently high, ensuring that during the mentioned process operations, the pressure won’t drop to a critical level that hampers normal use at key points. As a result, many customers opt for high-pressure compressors exceeding their actual needs and configure an ample number of backup machines. Some experienced customers who have conducted compressed air system calculations might consider this and plan the quantity of compressors and backup units accordingly. However, regardless of the approach chosen, in most cases, the result will be unnecessary high operating costs. Many people emphasize the energy consumption issue of compressed air systems, but by improving our understanding of compressed air systems or with the help of compressed air equipment suppliers, we can identify the root cause of the problem and solve the problem of high operating costs.
Storing clean compressed air to meet the demands of transient events is a highly effective solution. In essence, this involves adding sufficiently large storage tanks near these transient events. This ensures that you can always meet demands at lower pressures. By independently controlling these demands, you can operate the supply at appropriate independent pressures, thereby optimizing the performance of compressors and the entire compressed air system. Through precise compressor selection, design, pressure settings, and good supply performance, you can achieve the required compression with lower demands. This approach can even improve the quality of usage points, allowing the entire air system to operate efficiently.
Leakages, clogged filters, and increased airflow during component installations can all lead to a decrease in pressure at production equipment. Even small leaks can result in pressure losses that subsequently affect production quality. After 500 hours of operation,Filters at most are often overlooked and their filter elements are rarely replaced. In fact, many factories and warehouses don’t even keep spare filter elements on hand. When we talk about filters, we may consider whether the instability of the equipment is related to the need for maintenance or replacement of the filters. Unfortunately, it’s common for this problem to be diagnosed as insufficient air supply, and an immediate request is made to turn on the backup machine.
Sometimes, even when a customer’s air system doesn’t have compressed air applications with instantaneous high flow rates, the overall compressed air pressure will still decrease. This may be due to the aging of gas consuming equipment or the simultaneous use of multiple gas consuming points, resulting in an effect similar to “instantaneous” gas consumption. To solve these problems, it is necessary to conduct a detailed evaluation of each compressed air usage point on the production line and conduct professional calculations to identify the problem.
Each compressor manufacturer has sales or technicians, but their problem-solving methods may be different. Those who can make good use of various measurement tools and see the performance of the entire system have the opportunity to make satisfactory solutions for customers. Only those who truly identify the root cause of customer distress can gain customer’s recognition and approval.
Different compressor configuration choices will bring different effects. By increasing understanding of compressed air systems or seeking assistance from compressed air equipment suppliers, customers can obtain better solutions with less investment. Otherwise, we will fall into an endless price war, where customers may save some initial investment but pay a price ten or even a hundred times higher in energy costs.
By comprehensively considering factors such as the design and management of air tanks, leak detection and repair, filter maintenance and replacement, we can minimize problems in the compressed air system and ensure that customers receive sufficient and stable compressed air supply. Only in this way can customers obtain efficient production and reliable operation of air systems, while reducing energy consumption and maintenance costs, and achieving long-term energy conservation and economic benefits.
Contact Us
If you need to purchase an air compressor with a heat exchanger, we have products that can meet your specific requirements.
Contact[email protected]Whatsapp+86 13501890887
Based in
No. 668. Delixi Road. Nanxiang Industrial Development Zone, Shanghai, PRC.
Contact[email protected]
Whatsapp+86 13501890887
Based in
No. 668. Delixi Road. Nanxiang Industrial Development Zone, Shanghai, PRC.