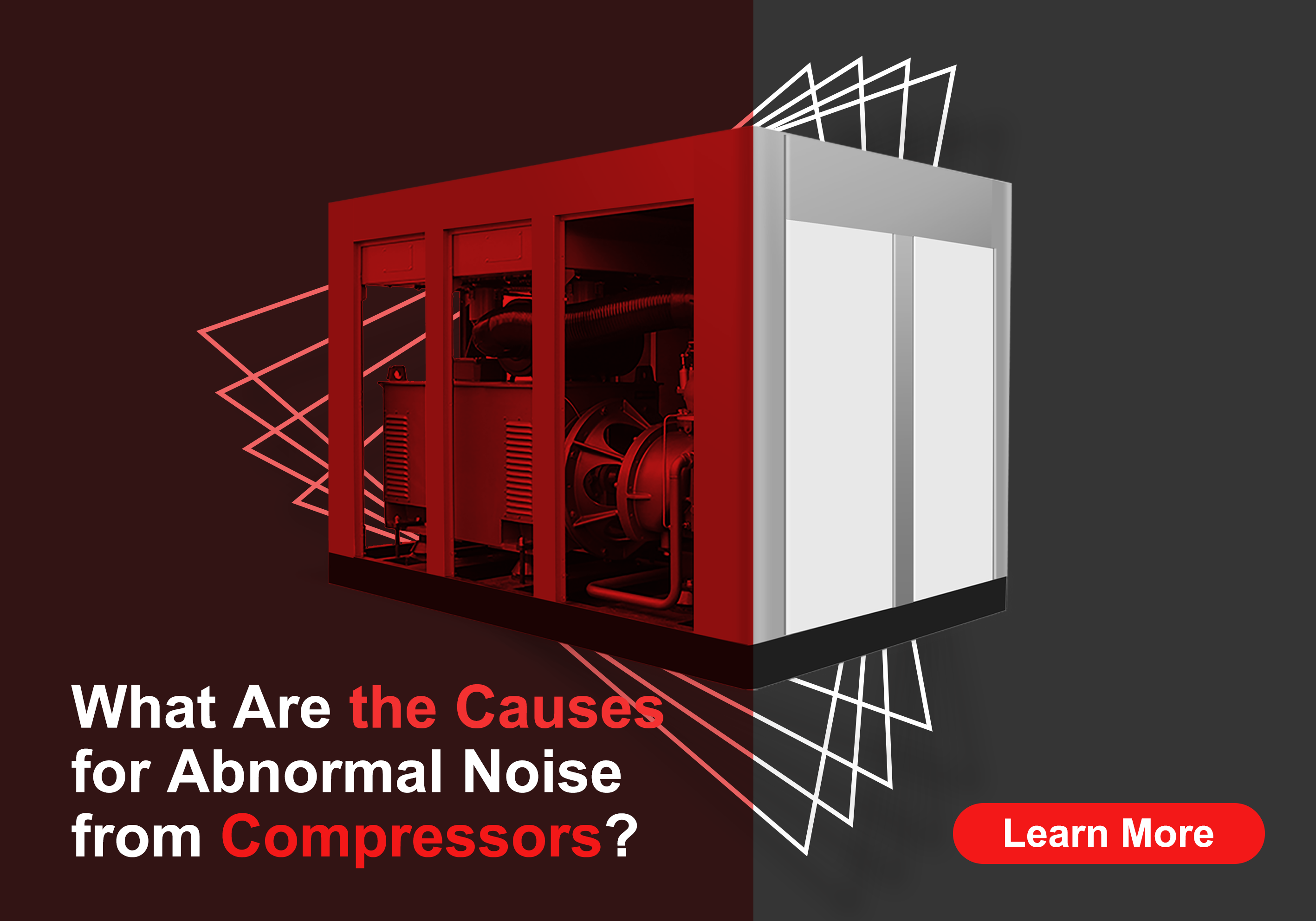
During the operation of a screw air compressor, we will meet various abnormal noises, such as metallic impacts, uniform knocking, or harsh noises, which are quite annoying. To solve these problems, we must find the causes and take appropriate measures.
Here are some aspects to consider when dealing with abnormal noises in air compressors:
Cause 1: Malfunction of the Silencing System, which mainly consists of brackets, sealing strips, door panels, and sound insulation cotton.
Treatment: Check the above components for any damages and ensure that the fixing bolts are tightened securely. During the operation of the air compressor, vibrations can occur due to inertia and frictional forces. Failure to conduct regular inspections or maintenance can lead to abnormal noises.
Cause 2: Motor Bearing Malfunction, which can be identified by listening for rolling or vibrating sounds, indicating excessive clearance or wear in the bearings. If the noise is hoarse or relatively heavy, it means that the motor grease has not been replaced for a long time or is caused by impurities. If the noise resembles a knocking sound, it could be caused by bearing damage, requiring replacement. If the noise is similar to a whistling sound accompanied by rolling noise, it is generally due to a lack of motor lubricating grease or improper use of lubricating oil. Adding lubricating grease or replacing the lubricating oil is necessary.
Cause 3: Malfunction of the air end, where foreign objects have entered the air end, causing the rotors to become stuck, collide, and friction, ultimately resulting in excessive clearance and damage to the bearings.
Treatment: Repair the rotors, readjust the rotor clearance, and perform dynamic balancing and verification again.
Cause 4: The intake valve can’t be fully closed, and air leakage occurs, or the check of the intake valve vibrates. The check valve noise is primarily caused by the lifting check valve, which is installed at the outlet of the air end to prevent compressed air from flowing back.
Treatment: Check the contact between the intake valve disc and the valve seat, clean the intake valve thoroughly, or replace it with a new one.
Cause 5: The lack of oil in the air end causes the male and female rotors to mesh without proper lubrication, resulting in a harsh noise during friction.
Treatment: Add screw air compressor lubricating oil.
Cause 6: The drive belt is loose and slipping to produce whistling sound (this is mainly the belt drive air compressor), and the uneven load operation of the machine leads to large current fluctuations;
Treatment: Check if the drive belt shows signs of wear or a burnt smell. In this case, adjust the tension of the belt to an appropriate level or replace it with a new V-belt. It is essential to replace all belts simultaneously, as replacing only one belt can cause different tension levels, leading to premature wear of the newly replaced belt.