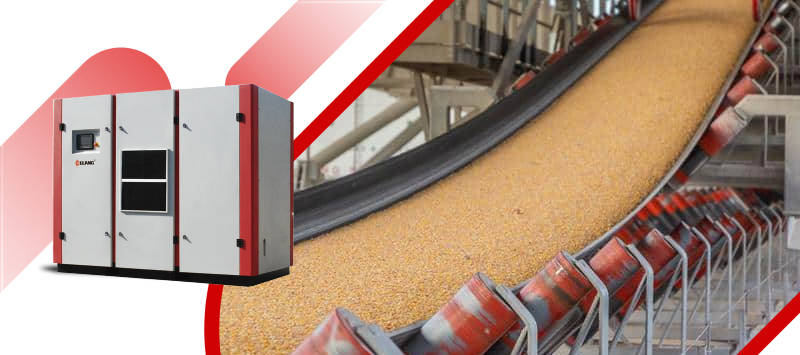
There is a large amount of grains that need to be moved around the world every day, including transferring them from silos, internal transfers within processing facilities, and loading onto trucks, trains, and ships. In recent years, pneumatic conveying systems have become the preferred method to handle this huge task, because they not only offer cost-effectiveness but also demonstrate high efficiency and reliability during operation.
How to Transport Grains
Pneumatic conveying systems are ideal for transporting bulk materials, including grains. However, not all grains are the same. The size, weight, and type of grains can affect the required flow rates and pressures, which in turn determine the specifications of the required blowers or compressors. Due to the existence of various types of pneumatic conveying systems, the most efficient system can be chosen based on the type of grains that need to be transported.
For example, for grains, options like dilute phase or dense phase pneumatic conveying can be selected, which is another reason why pneumatic conveying systems have become an ideal technology for grain transportation.
Designing a suitable pneumatic conveying system not only requires knowing which phase to transport materials in, but also considering the specifications of new equipment or the performance of existing equipment. This is done to ensure that the flow rates and air pressures match the type of grains that need to be transported. Choosing the right system specifications can create an efficient and smooth transportation process. Inappropriately selecting the specifications of blowers or compressors may lead to high energy consumption, frequent blockages, and extended unloading times.
Safety and Quality Factors in Grain Transportation
In the process of grain transportation, certain food safety standards need to be met. Additionally, due to the highly combustible nature of grain dust, the physical safety of production and processing facilities must also be considered.Therefore, the transportation temperature of grains should not exceed 40°C, as temperatures beyond this range can potentially lead to explosions or reduce grain quality. Furthermore, since the air comes into direct contact with the transported material, the use of oil-free blowers and compressors during this process is crucial to ensure that the product remains free from oil contamination.
Building an Ideal Grain Pneumatic Conveying System
Designing a suitable system can solve all the above problems, thereby achieving efficient and safe transportation of large amounts of grain without affecting grain quality.
The use of oil-free blowers and compressors in grain transportation can ensure the effectiveness of the system. Determining the correct specifications may require specialized software. Even when dealing with existing equipment, directly replacing old equipment is often not the most effective solution. Therefore, before purchasing a new blower or compressor, a specification check should be carried out.
In addition to this, the compressors or blowers in an ideal grain pneumatic conveying system need to provide oil-free or Class 0 certified air. Class 0 certification ensures that no oil is introduced into the air during the compression process.
Another important point to note is that certain types of grains may require certified equipment to operate in high-risk environments to prevent explosions. It is essential to check local and national regulations to ensure that the equipment meets all relevant requirements.
In addition to compressors or blowers, an after-cooler is also necessary to maintain the air temperature below a specific level, typically not exceeding 40°C, for most types of grains. The after-cooler ensures that the grains are not scorched, preserving their quality, and preventing combustion. Some compressors are equipped with an integrated after-cooler, but if it is a blower, a separate after-cooler needs to be installed.
The after-cooling process may generate moisture, therefore, the system also needs to add a water separator or dryer to ensure grain quality. Most integrated after-coolers have integrated water separators, but in some cases, a dryer can be used instead of a water separator to remove moisture from the air.
Compressed air can also be used in the fluidization process within silos, which is a method of injecting low-pressure air into the bottom sidewalls of the silo to ensure that grains do not adhere to the silo walls, making them easier to transport and reducing energy costs.
However, for food-related materials such as grains, which need to meet international quality standards and require cooling and the removal of moisture from compressed air, additional equipment such as after-coolers and water separators or dryers is necessary when fluidizing grains inside the silo.
If you have any questions about optimizing your pneumatic conveying system or are unsure about replacing an old compressed air system, please feel free to seek our assistance. Choosing the right equipment specifications is crucial for saving energy costs, reducing unloading times, and preventing blockages. We can help you find the ideal pneumatic conveying system by providing specification calculations.
Contact Us
If you need to purchase an air compressor with a heat exchanger, we have products that can meet your specific requirements.
Contact[email protected]Whatsapp+86 13501890887
Based in
No. 668. Delixi Road. Nanxiang Industrial Development Zone, Shanghai, PRC.
Contact[email protected]
Whatsapp+86 13501890887
Based in
No. 668. Delixi Road. Nanxiang Industrial Development Zone, Shanghai, PRC.