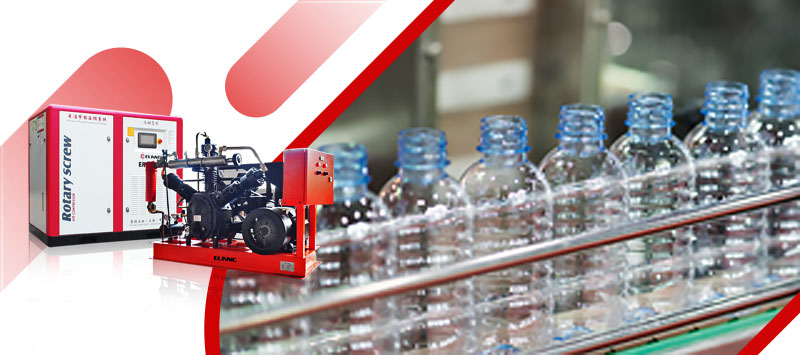
Pet is the most widely used beverage packaging material. PET bottle originated in the early 1980s. Because of its light weight, easy forming, low price and easy mass production, it has developed rapidly since it was invented. In just 20 years, it has become the most important beverage packaging form in the world. PET is not only widely used in packaging of products such as medicine, carbonated drinks, bottled water, condiments, cosmetics, Baijiu, dried fruit candy, edible oil, pesticides and detergents, but also specially used for filling fruit juice and tea beverage.
How is PET made into plastic bottle?
It is roughly divided into two steps: injection molding and blow molding.
First, PET particles were melted at high temperature to make preforms. The preform is like a test tube with a bottle mouth. There is a protruding ring on the bottle mouth, which is called a brace ring. This part is very important in the blow molding process. The support ring can be used to block the preform. After blowing out the bottle, the filling machine also needs to rely on the support ring to fix the bottle for filling.
The process of blow molding can be thought of as blowing a balloon, clamping the heated preform into the mold, inserting a metal rod into the preform, instantly injecting high-pressure air into the bottle, blowing up the preform until it gets stuck at the edge of the mold and forms a specified shape. After demoulding, a plastic bottle is completed.
High pressure air is needed to blow up the tube like pet preform instantaneously. Therefore, the matching air compressor must be medium and high pressure series, and the recommended pressure is 3-4mpa. If PET bottles are used for filling food, medicine and drinks, there will be higher requirements for air cleanliness – aseptic, dust-free and oil-free.
Elang air compressor has always been known in the industry for its energy-saving, low noise, environmentally-friendly, high quality and stable running.
The Elang water lubricated oil-free screw air compressor uses pure water as the medium for lubrication, sealing and cooling of the main engine, which can ensure that the air produced does not contain a drop of oil. Before entering the compressor chamber, the air will pass through the air filter element to remove most of the dust. The higher requirements of sterility and dust-free can also be achieved through the supporting post-treatment equipment. Elang medium pressure oil-free screw air compressor series has a pressure of 4MPa and a displacement range of 6m ³/ min—42m ³/ Min, to meet the needs of most blowing industry.