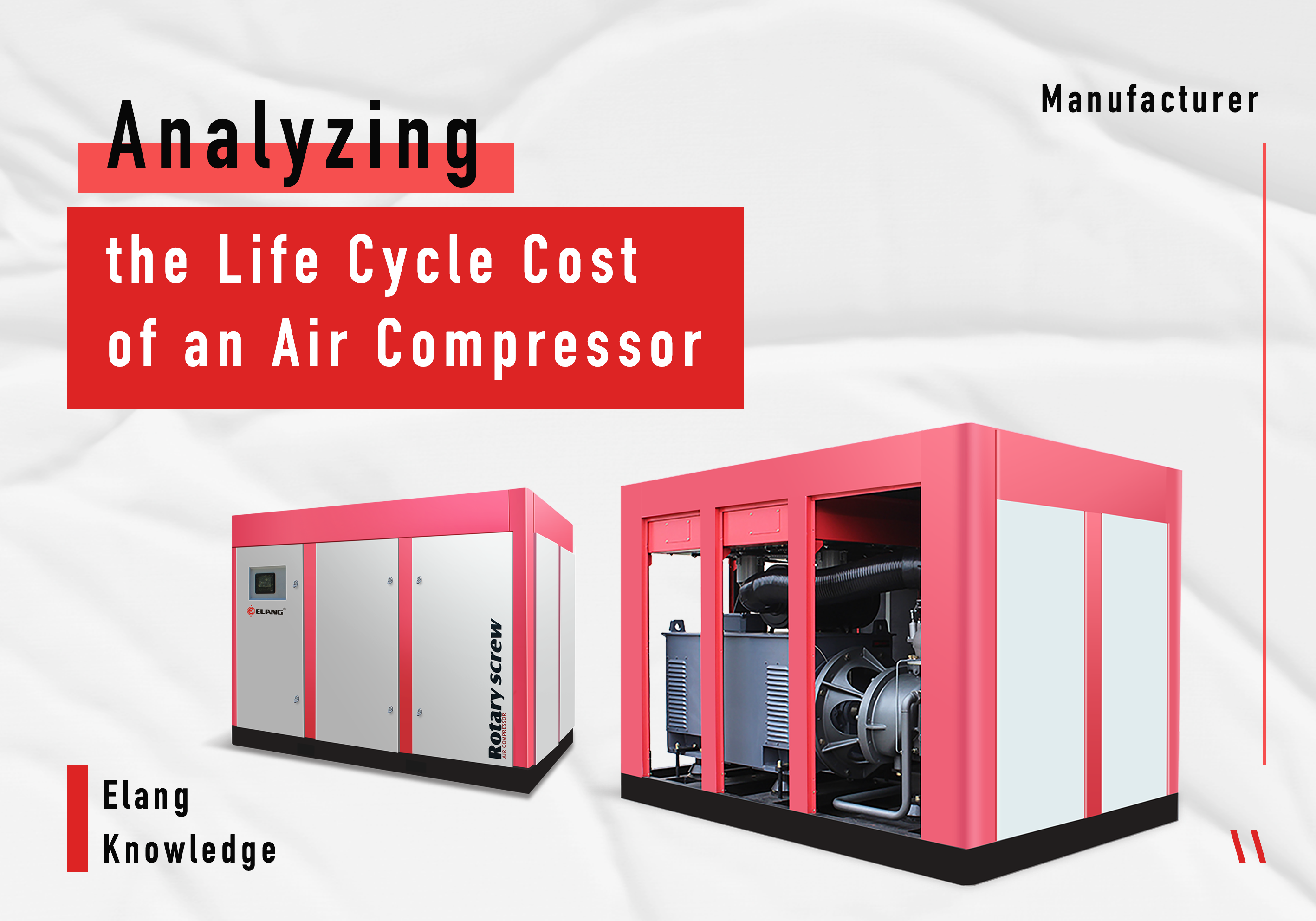
The life cycle of an air compressor refers to all the time from the beginning of the operation of the air compressor until the performance of the air compressor is reduced or can not be used.
During this period, problems such as decommissioning, aging, and continuous failures in the air compressor lead to increased maintenance costs and, ultimately, stop using.
The return on investment of different life cycles of air compressors
The air compressor is put into operation and begins to use. At different stages of its service cycle, the operating status of the air compressor is different for its value return.Air compressor just started to put into use may have a high failure rate, the main reason is because the equipment installation is unreasonable;The air compressor user is not familiar with the equipment and the air compressor mechanism manufacturing process defects.The air compressor supplier will provide quality assurance services within a year to give customers production security and value return.If the air compressor is at the end of its life cycle, its failure rate will naturally increase and energy consumption will increase, at this time, you can consider replacing the new air compressor equipment.
When the air compressor is put into operation, the air compressor needs regular maintenance during this period.Although the air compressor is in a stable operation stage during this period, its power conduction, mechanical components and electrical components will be worn.It may cause the failure of the air compressor to shut down, and eventually the value return of the air compressor will be impressed. Therefore, the air compressor must do preventive maintenance.
Whether the manufacturer’s after-sales service can meet customer demands
Customers hope that the life cycle of the air compressor has a good operating stability and low maintenance cost. Perfect after-sales service can analyze the customer’s industry, gas requirements, air compressor type and others to achieve the customer’s ideal goal.
1. Life cycle cost control
We all know that the electricity cost during the lifecycle of an air compressor accounts for approximately 70%, which is why energy efficiency needs to be controlled. The “specific power” that everyone often talks about is actually the customer’s energy efficiency detection and control. Energy efficiency control is mainly to optimize gas production pressure and gas pipeline leakage while meeting gas consumption requirements. At the same time, a centralized control system can be used to centrally control air compressors of different sizes, variable frequency air compressors, etc. 5-10% energy saving effect can be achieved through centralized control. Additionally, the waste heat recovery system can also be used to supply heat to reduce energy costs. If it is a centrifugal air compressor, it can save energy by three-stage pressure reduction, changing the three-stage to two-stage, etc.
2. The benefits that better control of energy consumption brings to companies
Companies that control energy consumption well have the characteristics of good efficiency, high added value, and continuous production. Typically, such companies have professional air compressor maintenance providers to provide services, providing customers with various maintenance plans, including a commitment to a 99.5% intact rate, responsibility guarantees, and standard maintenance content. Of course, the maintenance costs for these services are generally relatively high. However, many companies have intermittent production, low added value, and unstable benefits. They are generally oriented towards cost control. However, many companies have intermittent production, low added value, and unstable benefits. They are generally oriented towards cost control. The cost of this type of service is controllable and it is enough to ensure that the equipment does not malfunction during production. The cost of such services can be managed, with the primary goal of ensuring equipment reliability during production. Typically, this can be structured as ‘actual charges for maintenance consumables + systematic execution of equipment maintenance content as planned.’
Basic customer demands for air compressors
1. Low life cycle cost
The total cost incurred from the purchase of an air compressor to its service life, including maintenance expenses, electricity costs, installation, and all related costs, is referred to as the life cycle cost. Generally, in the life cycle of an air compressor, the procurement cost is 15%, the maintenance and management cost is 15%, and the electricity cost is 70%. So, if you want to reduce life cycle costs, the focus is on energy efficiency control.
2. The intact rate of an air compressor
In simple terms, it refers to the proportion of days when the air compressor is in normal operation (excluding downtime due to faults and other factors) over the course of a year. Increasing the intact rate by 1% can reduce downtime by 3.7 days, which is also very meaningful.
Contact Us
If you need to purchase an air compressor with a heat exchanger, we have products that can meet your specific requirements.
Contact[email protected]Whatsapp+86 13501890887
Based in
No. 668. Delixi Road. Nanxiang Industrial Development Zone, Shanghai, PRC.
Contact[email protected]
Whatsapp+86 13501890887
Based in
No. 668. Delixi Road. Nanxiang Industrial Development Zone, Shanghai, PRC.