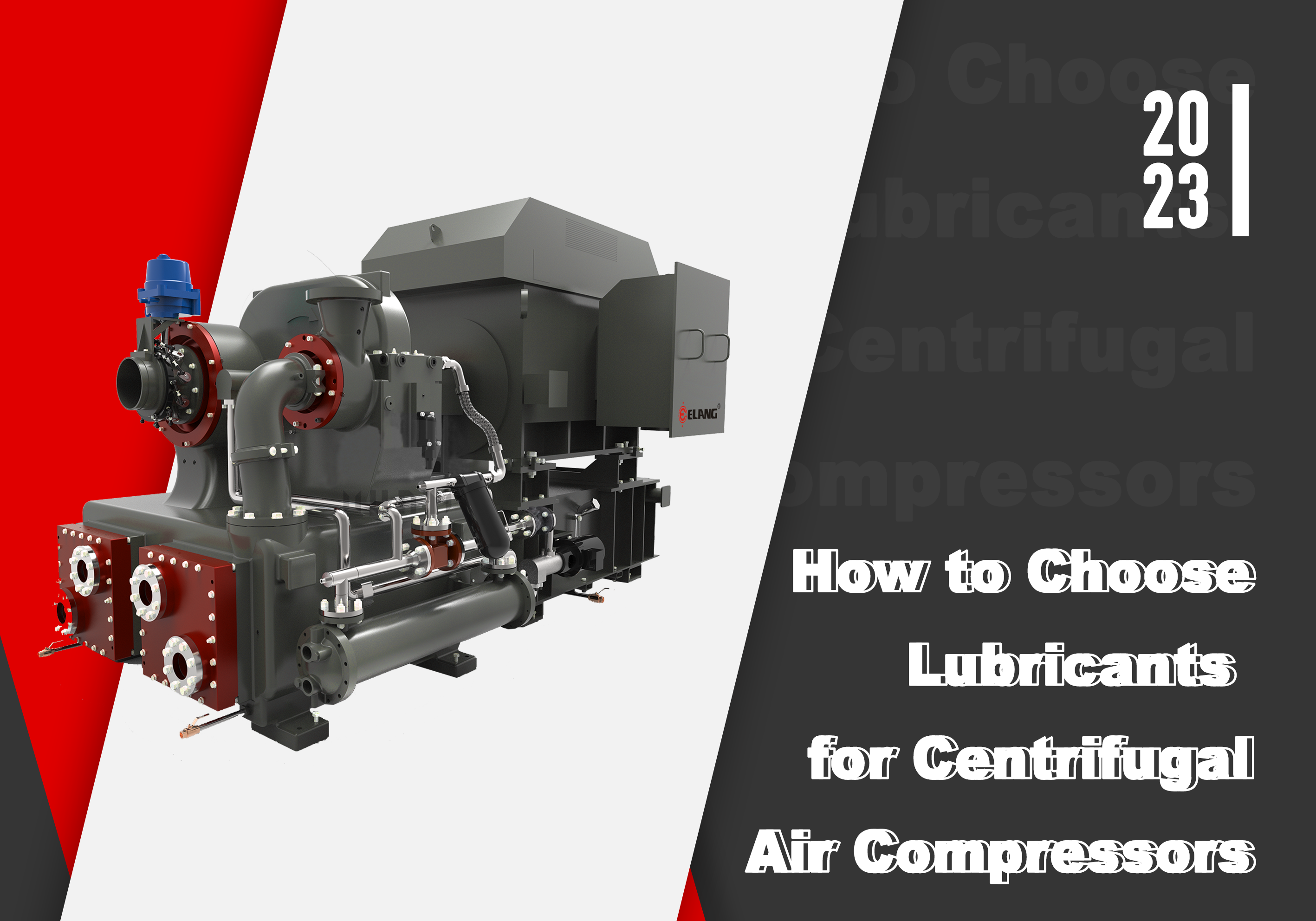
There is a wide variety of lubricating oil types with different performances. Therefore, users should choose appropriately based on the centrifugal air compressor's bearing type, operating speed, load size, and process environment.
The principles and criteria for selection are mainly as follows:
Working Temperature
Working temperature refers to the the ambient temperature bearing work in , and the temperature of this effect, if the ambient temperature is low, should be used with a small viscosity, low freezing point of the lubricant; higher ambient temperature, should be used with a large viscosity, high flash point of the lubricant; when the bearings are located in the working environment when the temperature changes are large, but also should be used with a good viscosity temperature performance, viscosity index of the lubricant is high. In short, in the selection of lubricants, according to the bearing operating temperature of the environment, so that it is reasonable, reliable work.
Working Load
The working load refers to the static and dynamic loads directly borne by the bearings (or friction pairs). When selecting lubricants, a comprehensive consideration of these loads is necessary. Under liquid lubrication conditions, oils with higher viscosity have greater load-bearing capacity. In the boundary lubrication regime, viscosity has limited effect on improving lubrication. Instead, oiliness and extreme pressure resistance become essential, making it necessary to choose lubricants with good extreme pressure resistance.
Motion Speed
The relative motion speed is an essential parameter in the design of bearings (or friction pairs) and is also a consideration when selecting lubricants. Generally, for bearings with lower relative motion speeds, lubricants with higher viscosity are suitable to facilitate the formation and maintenance of the oil film. On the other hand, for centrifugal air compressors, which typically operate at higher speeds, some reaching over 10,000 r/min, lubricants with lower viscosity are more appropriate choices.
Lubrication mode
Gap type oil lubrication or lubricant easy to lose parts, should be used with good adhesion, viscosity of the lubricant; centrifugal compressor is generally used in continuous, forced lubrication, so it should be used with a relatively small viscosity, good oxidation stability, rust, anti-foam and lubricating properties of the lubricant.
If air compressor compression medium has special requirements for lubricants, it should be used with the corresponding medium with resistance properties of the lubricant, such as ammonia compressor with anti-ammonia lubricants. In addition, the selection of oil should also refer to the equipment manufacturer recommended lubricants.
In summary, when selecting lubricants, one should consider both the equipment’s operating and environmental conditions. It is advisable to choose lubricants recommended by the equipment manufacturer to meet the operational requirements. Additionally, it is essential to minimize the variety of lubricants to facilitate their management.