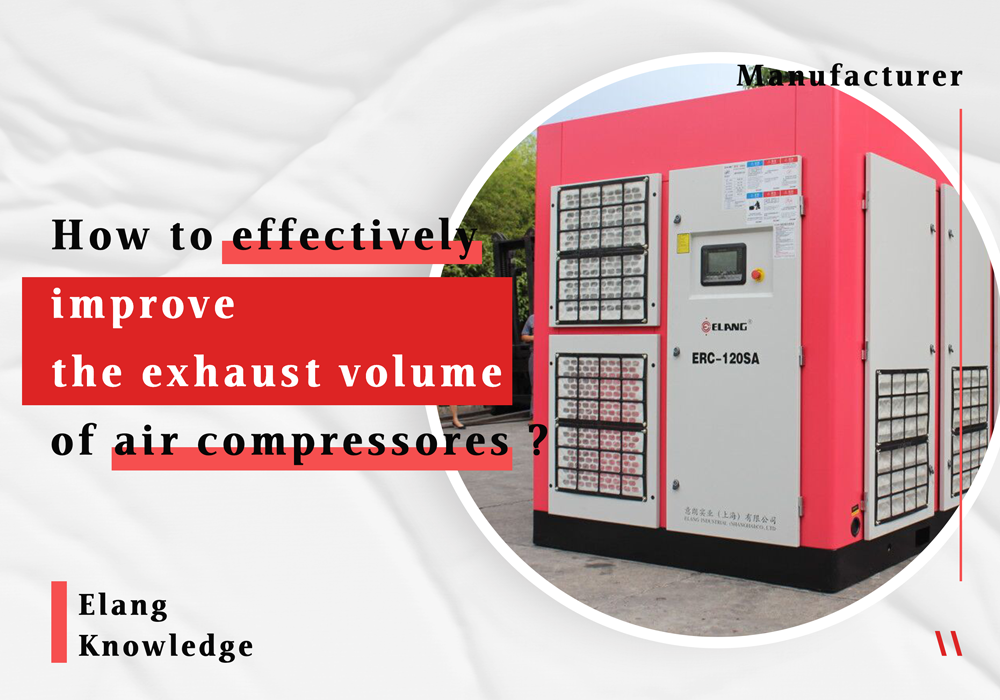
In the application of air compressors, the issue of compressor exhaust has always been a major concern for users.
Factors Affecting The Exhaust Volume of Air Compressors
To effectively increase the air compressor’s exhaust volume, several factors affecting the exhaust volume should be considered, including speed, leaks, cooling efficiency, and suction conditions, which are detailed as follows:
1. Rotor Speed
The air compressor’s exhaust volume is directly proportional to its rotor speed. The speed often varies with the voltage and frequency of the power supply. When the voltage (for asynchronous motors) or frequency decreases, the speed will also decrease, leading to a reduction in the air compressor’s exhaust volume.
2. Leaks
Air compressors have gaps between the rotors and between the rotors and the casing during operation, resulting in air leaks. When the compressed air leaks back to the suction pipeline or the engaged grooves during compression, the exhaust volume of the air compressor decreases. To reduce leaks, seal teeth are used on the driven rotor’s tooth tips, and seal grooves are created on the driving rotor’s tooth roots. If these sealing features wear down, the leak will increase, and the exhaust volume of the air compressor will decrease.
3. Cooling Efficiency
During the compression process, the air temperature increases, raising the temperature of the air compressor’s rotors and casing. As a result, the suction air will be heated and expanded during the intake process, leading to a reduction in the suction volume. Proper cooling using oil cooling for rotors and water cooling for the casing is essential to maintain the exhaust volume.
4. Suction Conditions
For positive displacement air compressors, the suction volume remains constant. When the suction temperature rises or the suction pipeline encounters excessive resistance, leading to reduced suction pressure, the air density decreases, resulting in a decrease in the air quality and exhaust volume.
Common Methods to Regulate The Air Flow of Air Compressors
1. Increase Rotor Speed
Properly increasing the speed of the air compressor can enhance its exhaust volume and compression efficiency, leading to higher air output.
2. Pipeline and Equipment Sealing
Maintaining the air tightness of the output air compression system’s pipelines, intake valves, air receivers, and coolers to prevent air leakage, ensuring continuous and efficient air flow.
3. Valve Sensitivity
Ensuring the sensitivity of the air compressor’s intake and exhaust valves, enabling quick and reliable opening and closing actions to maintain high compressor efficiency.
4. Reduce Suction Resistance
Minimizing the resistance during air suction by using larger-diameter intake pipes, well-designed intake systems, etc., can improve air flow rate and compression efficiency.
5. Air Drying and Cooling
Ensuring that the air compressor intakes dry and cool air, avoiding moist and hot air, helps enhance the compressor’s work efficiency and lifespan.
6. Advanced Cooling Systems
Adopting advanced cooling systems can effectively lower the air compressor’s operating temperature, improve thermal efficiency, and thereby increase the output air volume and compression efficiency.
7. Clearance Volume
Choosing the appropriate clearance volume size is crucial for the stable operation and air volume adjustment of the air compressor. Properly adjusting and controlling the clearance volume can affect the compressor’s compression ratio, thus regulating the output air volume.
By employing these adjustment methods, it is possible to effectively control the air compressor’s air flow output, meet air demands under different conditions, and enhance the compressor’s work efficiency and stability.