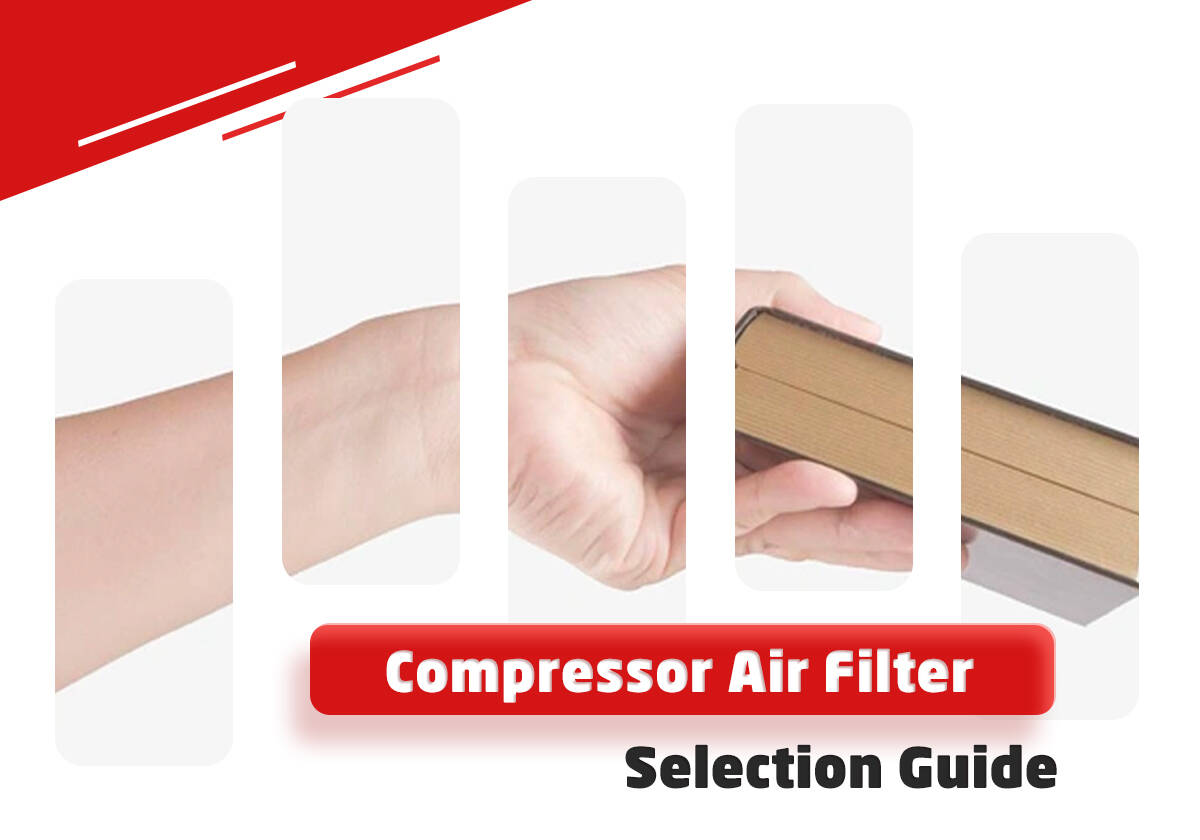
- Choosing the right air filter
- The compressed air drying and purification process
- 1. Single-stage filtration and purification system
- 2. Two-stage filtration and purification system
- 3. Two-stage filtration with refrigerated drying system
- 4. Three-stage filtration with refrigerated drying system
- 5. Three-stage filtration with adsorption drying system
- 6. Sterilization, deodorization filtration with refrigerated drying system
- 7. Ultra-clean compressed air drying and purification system
To achieve the expected effect of removing pollutant particles from compressed air, it is essential to design and select the filtration equipment correctly.
Choosing the right air filter
The main points of filter selection are as follows:
1. Precision Selection
In the selection of filters in the compressed air purification system, different types of filters should be chosen based on compressed air requirements of end-user. Exceeding the accuracy requirements, the selection of filters not only can not achieve the intended purpose of filtration, but also pay a costly economic price, so it is completely unnecessary.
The general trend is that the higher the filter accuracy, the higher the purchase cost, the shorter the service life, the greater the process pressure drop, and therefore the higher the operating cost. Therefore, The principle of selecting filter precision is to choose what is suitable.
2. Capacity Selection
The capacity selection of the filter should be selected according to the air flow that needs to be processed, and the filter with the corresponding specifications should be fully left room, which is the need to ensure the quality of the compressed air. With the extension of the use time, the performance of the filter will gradually age, such as the decrease of accuracy and the increase of pressure drop; Long-term full load use is particularly prone to premature aging, so a margin of 20% to 30% should be set aside when choosing.
3. The Layout of The Filter
The filter should be arranged according to the compressed air process, from low to high filtration accuracy. In addition, for some equipment in the process, it should also be noted that its special requirements, for example, the front end of the adsorption dryer should be equipped with oil removal filters, and the back end should be equipped with dust filters. Moreover, it should be noted that the maximum penetration rate of the filter occurs on the particle swarm of a specific particle size (0.1 ~ 0.3μm), so using two filters of the same specification in series does not double the filtration efficiency, and the particles that can penetrate the first filter can also penetrate the second filter of the same specification, while the filtration resistance increases exponentially.
The compressed air drying and purification process
In order to avoid the waste of manpower, financial resources and time, it is necessary to fully understand the pollution status of the system, and reasonably configure the dust removal, oil removal, drying facilities in the utilized compressed air system to achieve the optimization of a clean compressed air supply system. After the air is compressed, it is cooled by the after cooler, and the high temperature compressed air is reduced to 104 ~ 122 F. About 60% of the oil and water in the air are separated and discharged after condensation, and the residual trace oil, water aerosols and solid particles need to be removed by filtration. In the modern filtration process, the division of labor is more clear, for different requirements and different places of use, the filtration process is not the same, the difference is that the traditional equipment, all at once to complete all the process separation tasks. For purification systems with high precision filtration requirements, multiple-stage filtration is often employed, gradually increasing the filtration precision at each stage. This is done to achieve the desired filtration efficiency and precision for users while protecting and extending the service life of fine filters. Additionally, the equipment volume is greatly reduced, convenient installation and maintenance.
The gas-liquid separation method is generally used as a pre-treatment method in the filtration process to further separate solid particles and large liquid droplets carried in compressed air. The gas-liquid separation method typically employs inertial forces (centrifugal force, impingement, gravity settling) in conjunction with wire mesh demisters, it has a simple structure, is easy to manufacture, and is considered an excellent pre-treatment method. Typically, the gas-liquid separation method removes the particle size of more than 5μm, and the efficiency is more than 98%.
The primary purpose of pre-filtration is first to filter the residual trace solid particles in the air to protect subsequent high-precision filter. The second is the separation of oil and water aerosol particles with a certain particle size in the air. In the market, pre-filters are available in grades such as 1μm, 5μm, 10μm, etc., with an efficiency exceeding 99%. The pre-filtered air can be separately supplied to systems with low requirements, such as general workshop and blow-cleaning applications.
Fine filtration is the complete removal of residual oil and water aerosol particles in the air. The highest filtration accuracy of the fine filter on the market is 0.01um, the filtration efficiency is up to 99.9999% or more. and the residual oil content after filtration is less than 0.01mg/m³. Fine filtration is generally used in conjunction with pre-filtration to protect and extend the life of the fine filter.
In addition, in certain specific situations and industries such as food, fermentation, chemical, natural gas, etc., activated carbon may be used to adsorb odors, absorption methods may be employed to remove hydrogen sulfide and carbon dioxide, and glycol dehydration may be used to dry natural gas, etc.
1. Single-stage filtration and purification system
The system consists of compressor, after cooling equipment, air tank and filter. The air tank can be selected according to the compressor type. The simplest purification system consists of only a single-stage filter. The filter typically chooses pre-filters, the performance indicators and typical applications of the filtered air are shown in the table below. This process is the most common purification method for general-purpose air.
Compressed Air Quality | Impurity in compressed air | Application Situation | |||
Water | Solid Particle | Oil | Smell | ||
There are trace amounts of dust, water and oil. | There is a trace of liquid water, and the relative humidity is 100%. | 5μm | 5mg/m3 | Has a strong oil smell | Heavy pneumatic machinery, cleaning; Purge, general workshop air |
2. Two-stage filtration and purification system
This system adds one stage fine filtration on the basis of single stage filtration process, achieving a higher level of filtering accuracy. It is widely applicable to occasions where there is no strict requirement for dryness. The fine filter is protected by the air line filter, which can significantly improve the service cycle and life.
Compressed Air Quality | Impurity in compressed air | Application Situation | |||
Water | Solid Particle | Oil | Smell | ||
Almost all solids (particles, liquid water and oil are removed) | Relative humidity 100% | 0.01μm | 0.1mg/m3 | Smell of oil | Air stirring, granular product transportation, food and beverage processing, general pneumatic components |
Performance index and application of the compressed air after two-stage filtration and purification system
3. Two-stage filtration with refrigerated drying system
This system has added a refrigerated dryer, which freezes and separates water vapor in the gas to achieve a certain level of dryness. After the gas is separated from the large solid and liquid particles by the pre-filter, it enters the refrigerated dryer. And the condensate oil and water separated out is automatically discharged outside the machine. The drier gas is output after the heat exchanger, and finally, the fine particles, oil, water and aerosol particles remaining in the air are filtered out by the fine filter to provide high quality compressed air.
Compressed Air Quality | Impurity in compressed air | Application Situation | |||
Water | Solid Particle | Oil | Smell | ||
Free of dust, oil and water, relatively dry | Dew point 35.6 – 50 ℉ | 0.01μm | 0.1mg/m3 | Smell of oil | Packaging, textile machinery, powder product transportation, precision pneumatic technology, spraying, sandblast |
Performance indicators and applications of the compressed air after 2-stage filtration with refrigerated drying system
4. Three-stage filtration with refrigerated drying system
This system is based on the two-stage filtration with refrigerated drying system to add a one-stage activated carbon adsorption filter, which is used to adsorb and remove oil vapor and other odors in the air, and can be directly used for breathing, food and medical industries.
Compressed Air Quality | Impurity in compressed air | Application Situation | |||
Water | Solid Particle | Oil | Smell | ||
Free of dust, oil and water, relatively dry, odorless | Dew point 35.6 – 50 ℉ | 0.01μm | 0.03mg/m3 | Odorless | Breathing gas, pharmaceuticals, food, filling, clean room, high-pressure chamber |
Performance index and application of the compressed air after 3-stage filtration with refrigerated drying system
5. Three-stage filtration with adsorption drying system
Through coarse and fine two-stage filtration, the air is initially purified by removing oil, water, and aerosol particles to ensure that the adsorbent is not polluted by oil and loses its adsorption performance. Secondly, the air enters the adsorption dryer for deep drying. Finally, the dried air passes through a dust filter (generally a pre-filter) to remove secondary pollution caused by the adsorbent powder and then is exported.
Compressed Air Quality | Impurity in compressed air | Application Situation | |||
Water | Solid Particle | Oil | Smell | ||
Free of dust, oil and water, deep dry | Dew point below -4 ℉ | 1μm | 0.1mg/m3 | Greasy | Control instrument, Electronics, printing and film processes, air refrigeration, air bearing, spray |
Performance index and application of the compressed air after 3-stage filtration with adsorption drying system
6. Sterilization, deodorization filtration with refrigerated drying system
The activated carbon filter is added to the end-user for odor removal, the sterilization and disinfection system is added to remove bacteria in the air, and periodically using high-temperature steam from a steam filter to sterilize and disinfect the sterilization filter, thereby providing sterile and odorless compressed air, meeting the requirements for sterile air. The dryness of sterile air can be determined according to the specific process requirements. This system adopts the refrigerated drying method. If higher dryness is required, adsorption dryers can be used.
Compressed Air Quality | Impurity in compressed air | Application Situation | |||
Water | Solid Particle | Oil | Smell | ||
Free of dust, oil, water and bacteria, with a certain degree of dryness | Relative humidity below 60% | 1μm | 0.1mg/m3 | Odorless | Pharmaceutical industry, bioengineering, beer, brewing, food processing, dental instrument |
Performance index and application of the compressed air after sterilization and odor removal filtration with refrigerated drying system
7. Ultra-clean compressed air drying and purification system
After coarse and fine filtration, the oil, aerosol particles and part of the liquid water in the air are removed, enter the refrigerated air dryer for preliminary water removal and drying, and then clear the gaseous oil mist twice through the oil precision filter to ensure that the adsorbent of the back-end adsorption dryer maintains surface activity, and then through the dust filter and activated carbon filter. Remove the adsorbent powder, trace oil mist and odor that may be produced during the adsorption drying process. The system is mainly aimed at the compressed air system of oil injected air compressor.
Compressed Air Quality | Impurity in compressed air | Application Situation | |||
Water | Solid Particle | Oil | Smell | ||
Free of dust, oil, water and odor, very high dryness | dew point below -40 ℉ | 0.01μm | 0.003mg/m3 | Odorless | Pharmaceutical industry, bioengineering, beer, brewing, food processing, dental instrument |
Performance index and application of the compressed air after ultra-high cleanliness drying and purification
The above is only a brief introduction to several typical purification process systems, and the actual application process should be specific to specific problems, flexible layout, and adhere to the principles of reasonable, reliable, economic and convenient.
Contact Us
If you need to purchase an air compressor with a heat exchanger, we have products that can meet your specific requirements.
Contact[email protected]Whatsapp+86 13501890887
Based in
No. 668. Delixi Road. Nanxiang Industrial Development Zone, Shanghai, PRC.
Contact[email protected]
Whatsapp+86 13501890887
Based in
No. 668. Delixi Road. Nanxiang Industrial Development Zone, Shanghai, PRC.