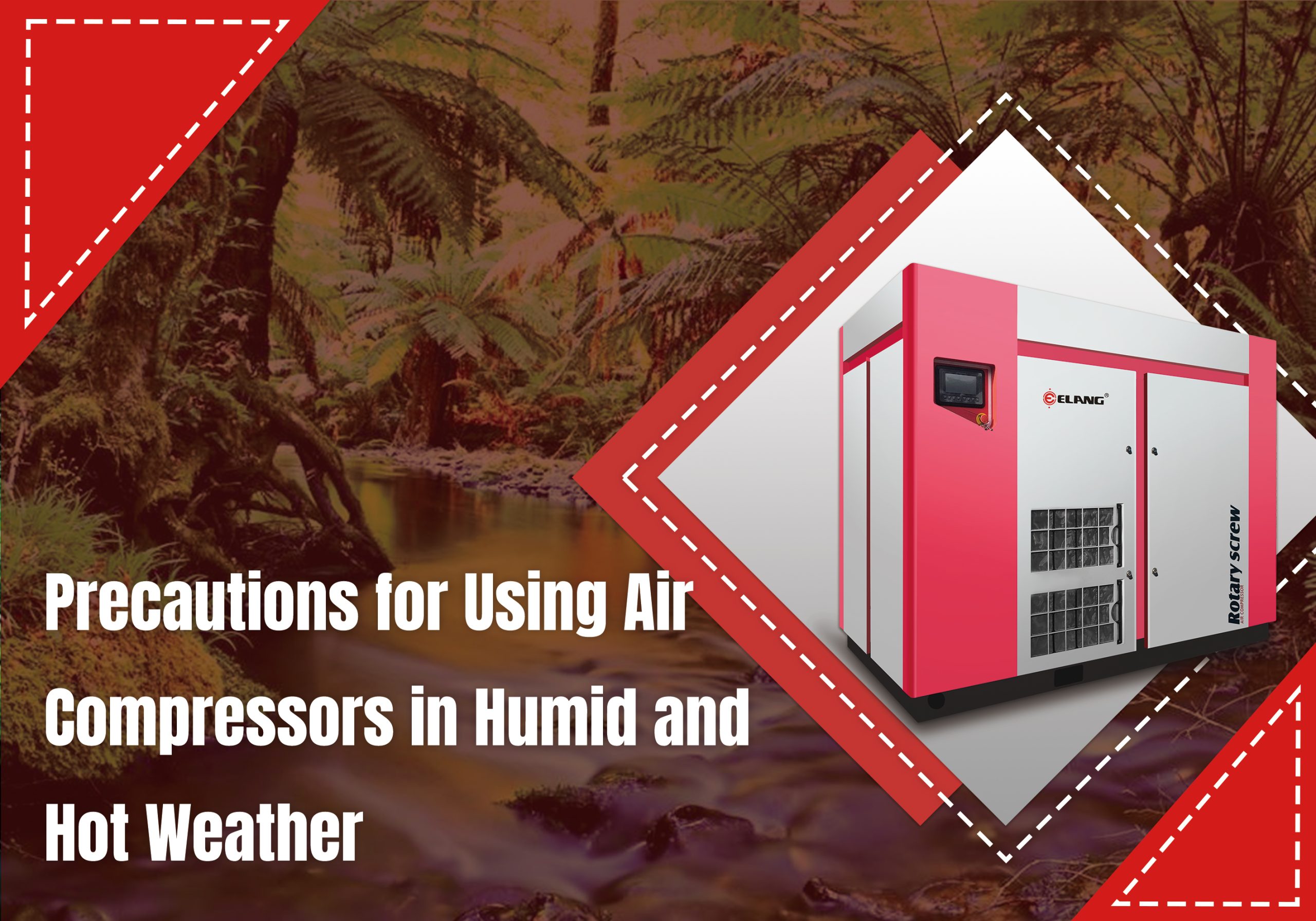
As the temperature gradually rises, humid and hot weather presents numerous challenges to the operation of air compressors. In such environments, ensuring the proper functioning and maintaining optimal performance of air compressors has become a focal point for many businesses.
This article will discuss the precautions for using air compressors in hot and humid weather to help you better maintain and manage air compressors.
Ventilation and Heat Dissipation of the Air Compressor
In hot and humid weather, the operating temperature of the air compressor is more likely to rise, which affects the stability and service life of the equipment. Therefore, it should be ensured that there is sufficient ventilation space around the air compressor to avoid overheating of the machine. Regularly clean the dust and dirt of the air compressor radiator, cooler and other components to maintain a good heat dissipation effect.
Control the Intake Temperature
In hot and humid weather, the moisture in the air is relatively high, and the intake temperature can cause moisture condensation during the compression process, affecting the operation effect of the air compressor. To ensure that the inlet temperature of the air compressor is within the allowable range, methods such as optimizing the layout of the air compressor room, increasing the length of the inlet duct, and using air pre cooling can be used to reduce the inlet temperature.
Check and Replace the Filter Element
In a hot and humid environment, components such as filters and oil separators in air compressors are susceptible to contamination, which can impact equipment performance. Regularly inspecting and replacing filter elements ensures the operational efficiency of air compressors and maintains the quality of compressed air.
Lubricating Oil Management
In humid and hot weather conditions, the performance of lubricating oil is easily affected, resulting in a decrease in the lubrication effect of the air compressor. Regularly check the oil level and oil quality of the lubricating oil, and replace the lubricating oil in time according to the cycle recommended by the manufacturer.
Cooling Water System Inspection
For water-cooled air compressors, regular checks of the cooling water system are necessary. This includes monitoring the water quality, quantity, and flow rate to ensure proper cooling effects. Additionally, pay attention to cleaning the cooling tower, cooler and other components to avoid the cooling effect being affected by dust and dirt blockage.
Preventing Electrical Equipment Moisture
Humid and hot environments can lead to moisture affecting the electrical components of air compressors, disrupting normal operations. Regularly inspect electrical equipment, including junction boxes, controllers, and cables, to ensure their seals are intact and prevent moisture ingress. If necessary, consider installing dehumidification equipment or improving ventilation facilities to reduce humidity levels in the air compressor room.
Adjust Operating Parameters
In humid and hot environments, the operating parameters of air compressors may need to be adjusted to adapt to climate changes. Depending on the compressed air demand and usage scenarios, configure the compressor’s load, unload pressure, temperature, and other parameters appropriately to maintain optimal operational performance.
Enhance Equipment Inspection
In humid and hot weather conditions, it’s essential to increase the frequency of air compressor inspections to promptly identify and address any abnormalities. Pay special attention to critical components such as bearings, belts, fasteners, and make adjustments or replacements as needed.
When using air compressors in humid and hot weather, particular attention should be given to managing aspects like heat dissipation, intake temperature, filter elements, and lubricating oil. Only by meticulously managing these details can air compressors maintain stable and efficient operations in challenging environments, thereby creating greater value for businesses.