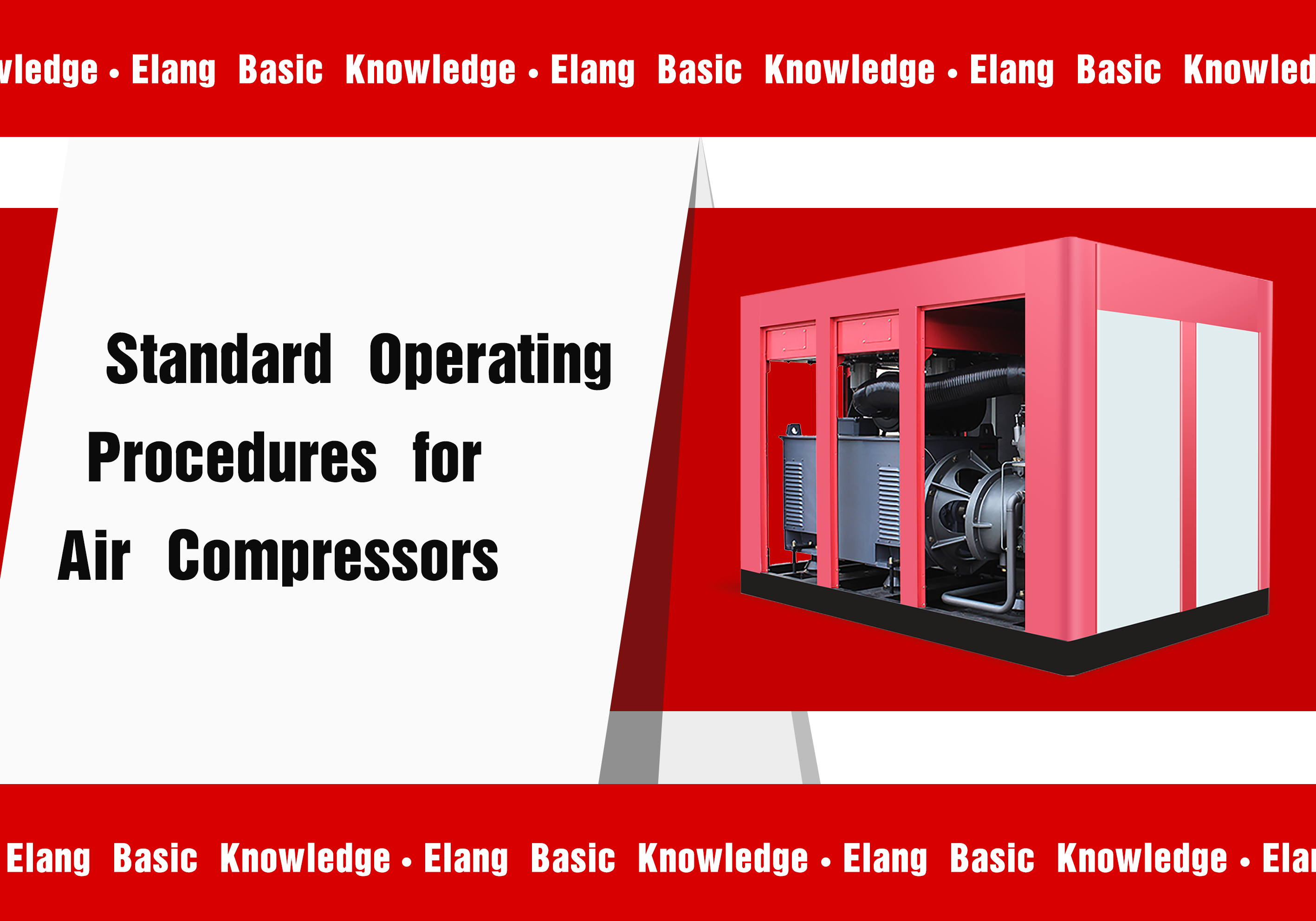
In order to ensure the safe and efficient operation of the air compressor, each operator must first have a thorough understanding of the working principle, performance characteristics, and equipment structure of the air compressor. In addition, it is also crucial to always follow the safe operating regulations related to the use of air compressors.
Preparations Before Starting The Air Compressor
1. Firstly, it is essential to make sure that there are no unrelated items present on the equipment itself or in its immediate surroundings.
2. Check whether the cable is connected to the electric control box, the ground wire is connected normally, and the measured voltage is normal, to ensure that the 3 phase power supply is correct. Also, check the wiring in the control cabinet.
3. Manually rotate a few times in the direction of the motor arrow to avoid reverse rotation.
4. If the shutdown time of the air compressor is relatively long (usually exceeding 4 months), it is necessary to pour 3L of lubricating oil into the air end before starting up and then manually rotate the air end for a few turns to avoid failures caused by lack of oil inside the air end due to long-term shutdown. Lubricating oil should be added from the air inlet of the air end. When the intake valve is removed, take care to prevent foreign matter from entering the air end, which could lead to be stuck. Ensure that the added lubricating oil matches the type used inside the air end, and it should be clean and free of impurities.
5. Check if the lubricating oil level is between the two marks on the oil level sight glass. If it’s Insufficient, add oil up to the minimum mark. The type of oil added should match the one used in the air end. Do not mix different types of lubricating oil.
6. Check all Connections on the air compressor for tightness. If there is looseness, it needs to be tightened to avoid oil leakage and air leakage during work.
7. For water-cooled air compressors, check if the inlet and outlet valves are blocked. Ensure that the water pressure is maintained between 2 to 4 Bar.
8. Use a multimeter to test the incoming voltage to ensure that the cable meets the specified requirements.
Precautions for Starting an Air Compressor
1. Close the power switch and open the discharge valve at the same time.
2. Check if the rotation direction of the air end is correct. If the direction is incorrect, stop the machine immediately for inspection.
3. After the air compressor successfully starts, check whether there is a fault signal on the control panel to ensure that there is no abnormal sound or vibration. If none of the above conditions occurs, the working pressure will gradually rise to the rated pressure.
4. When the air compressor works normally, it is necessary to check and record the operating parameters of the air compressor regularly.
Condensate Discharge
When the compressed air enters the oil-gas tank, moisture may condense at the bottom, especially during rainy seasons or humid weather, where the exhaust temperature is easily lower than the pressure dew point, making it easy to produce condensate. Excessive moisture in the oil will cause the emulsification of the lubricating oil and affect the normal operation of the air compressor. The main impacts are that the parts on the equipment are corroded, the pressure difference of the oil separation element becomes larger, the oil-gas separation effect becomes poor, and the rotor is insufficiently lubricated.
Cooling Water Discharge Method
After the air compressor is shut down, ensure that there is no pressure in the system and sufficient cooling is obtained. After the cooling water settles, discharge it before starting. Firstly, open the bolts in front of the ball valve, then open the ball valve to discharge water until lubricating oil flows out and close the ball valve, and finally screw on the ball valve bolt.
Method of Changing Lubricating Oil
1. Precautions: Before replacing the lubricating oil, the air compressor should be shut down and replaced without pressure in the system.
2. First, run the air compressor for a period of time until the exhaust temperature reaches 60 ℃-80 ℃, and the lubricating oil is fully preheated, and the internal pressure of the system is discharged when the air compressor is shut down.
3. Slowly open the ball valve to release the lubricating oil.
4. For water-cooled air compressors, first open the oil cooler drain bolt to drain the lubricating oil completely.
5. After the lubricating oil is discharged, close the ball valve and screw on the bolts, and finally dispose of the discharged waste oil properly.
Method of Adding Lubricating Oil
1. Open the oil filling port on the oil-gas tank, and add lubricating oil until it reaches between the two scale lines of the oil level sight glass.
2. For water-cooled air compressors, the oil drain bolt of the oil cooler should be tightened.
3. After filling it up, tighten the oil filling bolt. Then, start the compressor and let it run for 3 to 5 minutes under load. Afterward, once again observe the oil level in the sight glass to ensure the correct lubricating oil level—adding more if it’s too low or adjusting if it’s too high.
Precautions for Lubricating Oil
The lubricating oil used must be the screw air compressor lubricating oil produced by the authorized manufacturer, and it should be replaced according to the manufacturer’s requirements. Avoid using low-quality lubricating oil in pursuit of cheaper options. The use of low-quality lubricating oil will damage the air compressor, the main effects are:
1. Reduced the service life of compressor spare parts.
2. Damage the separation effect of the oil gas separator and oil filter, reducing the service life of the oil separation element and oil filter.
3. Poor quality lubricating oil is more prone to carbon accumulation and emulsification, which can block the oil system, leading to various valve failures, and even causing serious system blockage and air end lockup.
A special reminder: When replacing or adding lubricating oil, always use the same brand and the same type of lubricating oil. Avoid mixing different brands or types of lubricating oils.
Replace Oil Filter
After 500 hours of operation, the air compressor’s oil filter should be replaced. Subsequently, during later stages of usage, the oil filter should be changed every 3000 hours. If the pressure differential across the oil filter reaches 2 bar, it should be replaced immediately. The replacement steps are as follows:
1. After shutting down, completely release all the pressure within the air compressor.
2. Use a belt wrench to turn the oil filter counterclockwise and remove it and check if the new oil filter and sealing ring are in good condition.
3. Replace the old oil filter with a new one and tighten it clockwise. After starting the compressor, check if the machine operates normally.
Replace Oil-gas Separator
The replacement cycle of the oil-gas separator is generally around 3000 hours, and Its separation efficiency determines the oil content in the compressed air. The replacement steps are as follows:
1. After shutdown, completely release the pressure within the air compressor.
2. Remove the piping of the minimum pressure valve, the return oil line, and the oil-gas separator cover.
3. Remove the old oil separator element and replace it with a new one.
After replacing the oil separator with a new one, it is necessary to insert the return pipe into the bottom of the oil separator to ensure that all the deposited lubricating oil can be extracted. Also, make sure that the sealing gasket with the metal copper piece on the oil separator element is intact. This metal copper piece is used to avoid the accumulation of a large amount of static electricity on the oil separation element, which could lead to oil and gas combustion or explosions.