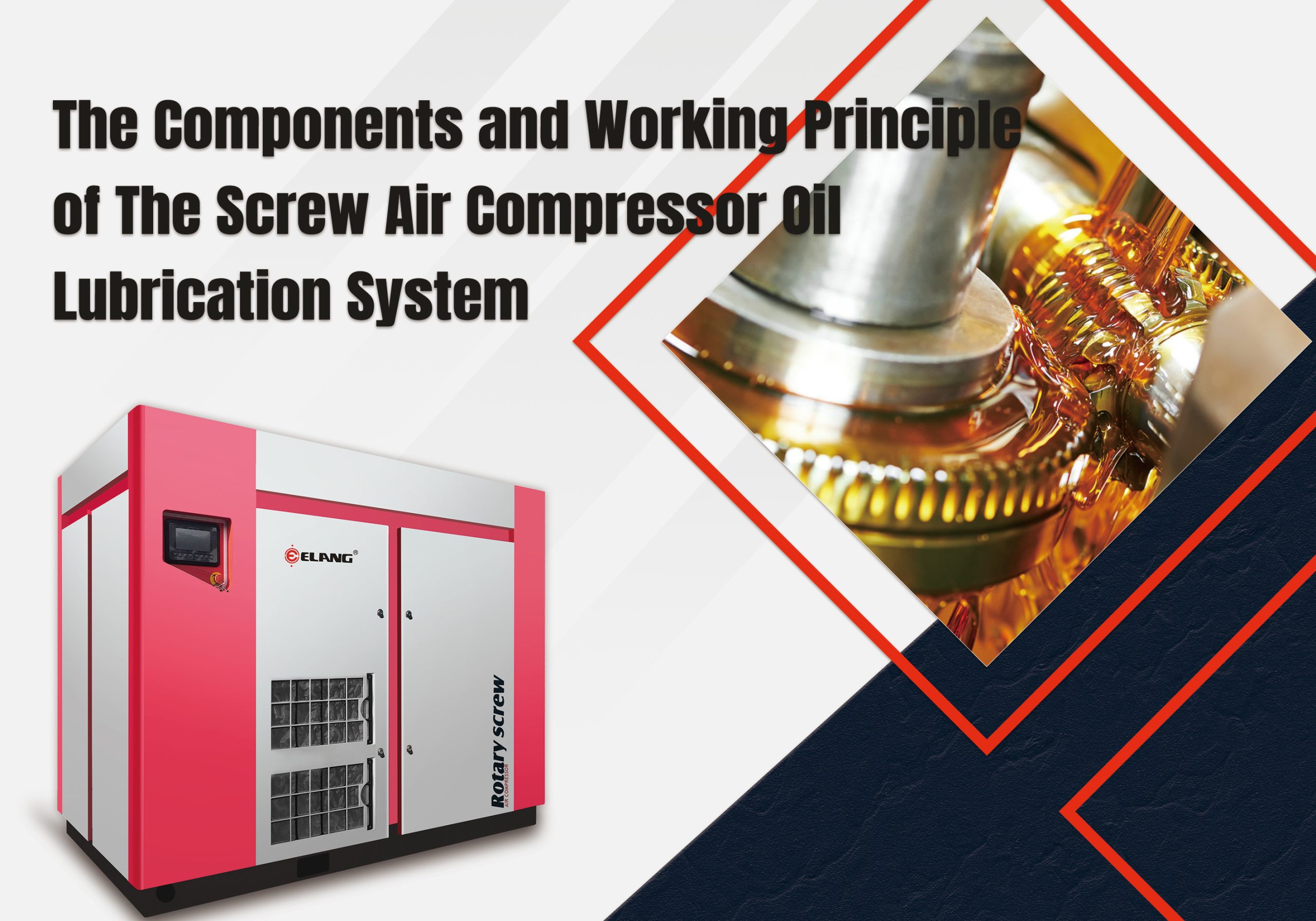
Because of the internal pressure of the oil-gas tank, the lubricating oil of the air compressor is directed into the cooler for cooling. The cooled lubricating oil enters the oil filter to filter impurities, and a part of the lubricating oil is sprayed into the main engine through the bottom of the main engine to cool the compressed air. The cooled lubricating oil enters the oil filter to filter impurities, and a part of the lubricating oil is sprayed into the air end through its bottom to cool the compressed air. Another part of lubricating oil enters both ends of the air end to lubricate bearings and transmission gears, etc., and finally all the lubricating oil gathers within the air end and is discharged along with the compressed air.
Oil Filter
The interior of the oil filter contains folded filter paper, primarily intended to eliminate impurities and metallic particles from the lubricating oil. Its filtration precision generally ranges from 5 to 10 micrometers, providing effective protection for bearings and rotors. When the pressure difference indicator light of the oil filter is illuminated, it signifies blockage and necessitates replacement. The first replacement time for newly purchased equipment is 500 hours. The later replacement cycle should be replaced according to the prompts of the differential pressure indicator. If the oil filter is not replaced for a long time and the clogging will result in insufficient supply of lubricating oil, it will cause the air compressor to shut down at high temperature.
Oil-Gas Separator
The oil separator element is primarily composed of multiple layers of fine glass fibers. It effectively filters out nearly all of the oil mist from the oil-gas mixture discharged from the air end. The service time of the oil separator element is generally 2000~4000 hours. The service life of lubricating oil mainly depends on factors such as the operational environment and quality of the air compressor. When selecting lubricating oil, it’s important to choose oil specifically designed for rotary screw air compressors.
At the top of the oil separator element, safety valves and minimum pressure valves are generally installed. The compressed air, filtered after passing through the element, is discharged from here and enters the cooler. The mist-like oil and gas, after filtration through the separator element, flows to the bottom of the element and then reenters the main unit through the return oil pipe. For detailed separation methods, you can refer to a previously written article on “Oil-Gas Separation Methods in Air Compressors.”
Temperature Control Valve
The temperature control valve is installed in front of the cooler and its primary function is to maintain the exhaust temperature at the dew point temperature of the pressure. After the air compressor is started, the lubricating oil temperature is generally lower. The temperature control valve will open the return circuit, allowing the lubricating oil to directly enter the air end without passing through the oil cooler. When the oil temperature reaches 70°C, the valve will slowly start opening until it’s fully open at 85°C. At this point, the lubricating oil goes through the oil cooler for cooling before entering the air end.
Air-cooled Type Oil Cooler
The cooling effect of the cooler is mainly related to the operating environment of the air compressor. If the fins of the cooler are easily covered by dust, which affects the cooling efficiency, the exhaust temperature might become too high and lead to compressor shutdown. Therefore, it is necessary to regularly clean the cooler or blow its surface with low-pressure air. If internal blockages occur, it may require soaking and cleaning with a cleaning agent.