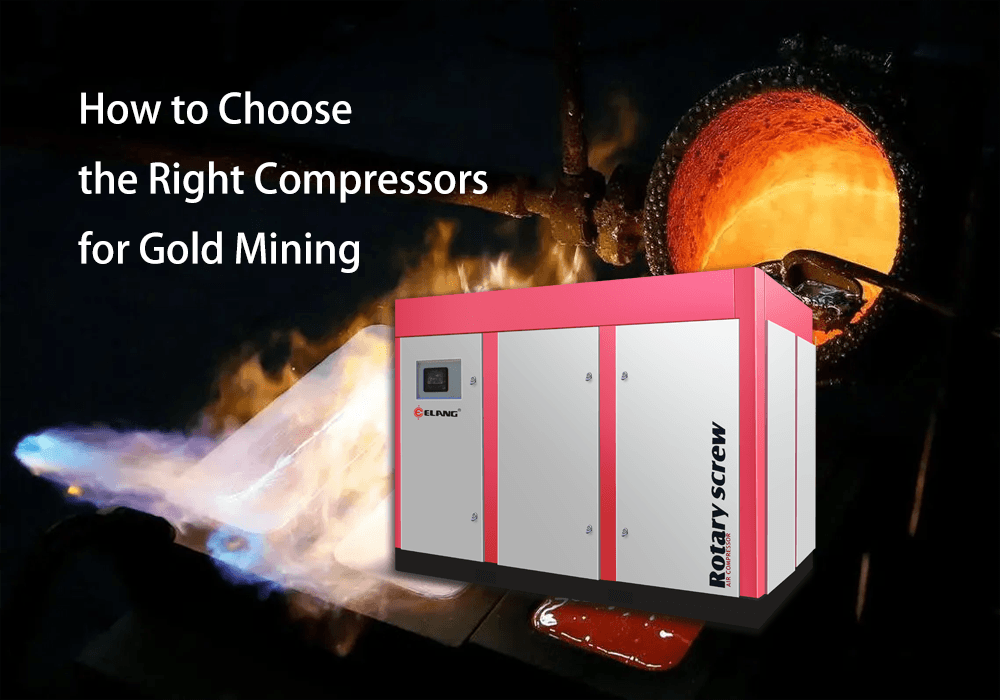
As an economical air compressor, this article focuses on introducing the supply air principle and the main features of twin-screw air compressors, including easy maintenance, low failure rate, and high level of automation.
In the past, reciprocating air compressors were widely used in gold mining operations. And Its main principle was to form suction and exhaust due to the reciprocating motion of the piston. However, in the process of using reciprocating air compressors, there are common issues such as frequent breakdowns, high energy consumption, excessive noise, complex structure, more wearing parts, intensive maintenance requirements, high maintenance costs. These compressors may not be able to effectively meet the air flow requirements of gold mining.
In gold mining enterprises, especially in gold ore beneficiation plants, the application of air compressors is widespread. In particular, in the cyanide leaching process of gold, the use of pneumatic agitation tanks has gained significant development in recent years. The pneumatic agitation tanks effectively increase the tank capacity with a high height-to-diameter ratio, thereby improving the processing capacity. The air pressure and air flow in the pneumatic agitation tanks directly impact the leaching efficiency. In the process of gold dissolution, the concentration of cyanide and oxygen needs to be in a certain proportion. When the cyanide concentration is constant, the dissolution rate of gold mainly depends on the concentration of oxygen (i.e., the degree of solution aeration). Insufficient air pressure and airflow can result in poor leaching efficiency and significant gold losses. Therefore, air compressors with low failure rates and low energy consumption are of great significance to gold beneficiation plants.
Reciprocating Air Compressor
Structure and Principle
Currently, oil-free reciprocating air compressors are commonly used in beneficiation plants. The basic structure consists of an electric motor driving a crankshaft through a belt, and the reciprocating motion of the piston is transmitted through the connecting rod. During operation, the working volume, formed by the cylinder wall, piston, and cylinder head, undergoes periodic changes.
When the piston starts moving from the cylinder head, the working volume of the cylinder increases. The intake valve opens, allowing gas to enter the cylinder until the piston reaches its lower limit, at which point the intake valve closes. The piston then reverses its motion, causing the working volume inside the cylinder to decrease and the gas pressure to rise. When the pressure inside the cylinder reaches slightly above the discharge pressure, the exhaust valve opens, allowing the gas to be discharged from the cylinder until the piston reaches its upper limit. The exhaust valve then closes, and the cycle repeats, continuously discharging high-pressure gas.
This cyclic operation ensures a constant supply of high-pressure gas from the compressor.
Disadvantages
1. During the use of reciprocating air compressors, there is a high requirement for equipment operators. Operators need to have a good level of mechanical expertise and be able to judge whether connecting bolts are loose based on operating sounds. Otherwise, accidents such as cylinder and piston rupture or crankshaft failure may occur.
2. The intake and exhaust valves are easy to damage in reciprocating air compressors. Once the damage is not found in time, it will lead to insufficient displacement, resulting in wasted electrical energy and overheated cylinder head. At the high temperature, the guide rings and piston rings will quickly wear out, leading to accidents such as piston seizure.
3. During operation, reciprocating air compressors can produce significant noise. In a particular factory, when three 60m3 oil-free reciprocating air compressors are running, the noise level in the compressor room reaches 93.5-97.4 dB.
4. The reciprocating filter press has a low degree of automation and complex structure. It’s not easily disassembled, and takes 3-5 working days to replace spare parts such as cylinder heads, pistons, or crankshafts, severely limiting production efficiency.
Twin-screw Air Compressor
The twin-screw air compressor is a new type of air compressor that has been improved based on the single-screw design. Compared to reciprocating air compressors, twin-screw air compressors have several advantages such as low noise levels, simplified maintenance, low failure rates, and a high level of automation.
Structure and Principle
The twin-screw air compressor consists of components such as the air end, motor, oil-gas separator, cooler, and electric control system. The air end is an important component of the compressor. There is a pair of interconnected rotors in the air end that rotate at high speed driven by the electric motor. As the volume between the teeth decreases, the inhaled air is continuously compressed, while lubricating oil is continuously injected into the working chamber of the air end. When the volume between the teeth is connected to the exhaust port of the air end, the oil-gas mixture is discharged through the exhaust port. The oil and gas are separated through the oil-gas separator, removing the lubricating oil from the air. The lubricating oil returns to the oil-gas separator after being cooled, while the air flows through the separator and enters the after cooler until it reaches the desired discharge temperature.
Working Principle
The screw air compressor is a positive displacement air compressor, which means it reduces the volume of air to increase the pressure. The working cycle can be divided into four processes: suction, enclosure, compression, and exhaust. As the rotor rotates, each pair of intermeshing screws completes these four steps:
1. Suction process: When the rotors pass through the inlet, air is drawn into the air end axially. The intake volume is regulated by the intake control valve, which consists of a butterfly valve and a cylinder adjustment mechanism.
2. Sealing process: After passing through the inlet, a certain volume of air is sealed in the compression chamber formed by the two rotors.
3. Compression and delivery: As the rotors rotate, the volume of the compression chamber decreases, resulting in creasing the air pressure.
4. Exhaust process: The compressed air reaches the outlet at the other end, completing the compression process and being ready for use or further treatment.
Advantages
1. Simple structure: The screw air compressor has fewer components and less maintenance. The rotors do not come into contact with the casing, and only the bearings are the worn parts. The compressor has a long service life and only requires regular replacement of filters and lubricating oil.
2. Stable: Unlike piston air compressors, there is no reciprocating motion mechanism, no unbalanced inertial force, smooth operation, low noise, and no more than 85db (A).
3. Long lubricating oil life: The lubricating oil used in screw compressors can last up to 8000 hours. Moreover, the oil consumption during operation is low, and there is no need to replenish it.
4. Automatic adjustment: The air flow can be automatically adjusted according to demand. When the air flow or pressure exceeds the required level, the intake valve automatically adjusts to save energy.
5. High level of automation: Screw compressors have built-in safety features that automatically shut down the compressor in case of a malfunction, preventing further damage to the equipment. The requirements for equipment operators are relatively low, and operators only need to regularly monitor pressure and temperature, avoiding major accidents similar to reciprocating air compressors caused by operators not discovering problems timely.
6. Energy-efficient motor: Compared to reciprocating air compressors, screw compressors have higher efficiency, especially under the same load conditions. They achieve the highest energy savings when operating at full load.
7. Low failure rate: In a specific factory where the compressor room is unattended, the maintenance and repair time for piston compressors was 153.6 hours per unit annually. After using twin-screw air compressors, the maintenance and repair time reduced to 11 hours per unit annually, mainly for regular maintenance. This significant reduction in downtime ensures continuous production.
Analysis of the Application Effects of Twin-screw Air Compressors
In a gold metallurgical plant, the compressor room initially had three 250 kW reciprocating air compressors, supplying 130 m3/min of air flow at 0.20 MPa. By replacing two of these compressors with 367kw twin-screw air compressors, the air flow capacity can reach 140-150 m3/min at 0.24 MPa. Assuming the plant operates for 350 days a year, 24 hours a day, and the cost of electricity is 0.8 CNY per kilowatt-hour, without considering the excess airflow or the automatic adjustment function of the twin-screw air compressors, the cost savings can be calculated as follows:
(250 * 3 – 367 * 2) * 24 * 350 * 0.8 = 108,000 CNY
Additionally, the plant can save maintenance costs for the three reciprocating air compressors, estimated at 100,000 CNY. Moreover, the recovery of additional gold amounts to approximately 700,000 yuan. Therefore, the plant can save a total of 910,000 CNY per year, and the conversion cost can be recovered within two years.
The application of twin-screw air compressors in the leaching process of gold concentrator not only ensures stable air flow, but also avoids noise pollution in the plant. This is playing a significant energy-saving effect and obvious environmental benefits. They are considered typical energy-efficient air compressors and an ideal replacement for older reciprocating air compressors. They are well-suited for widespread adoption in various applications.