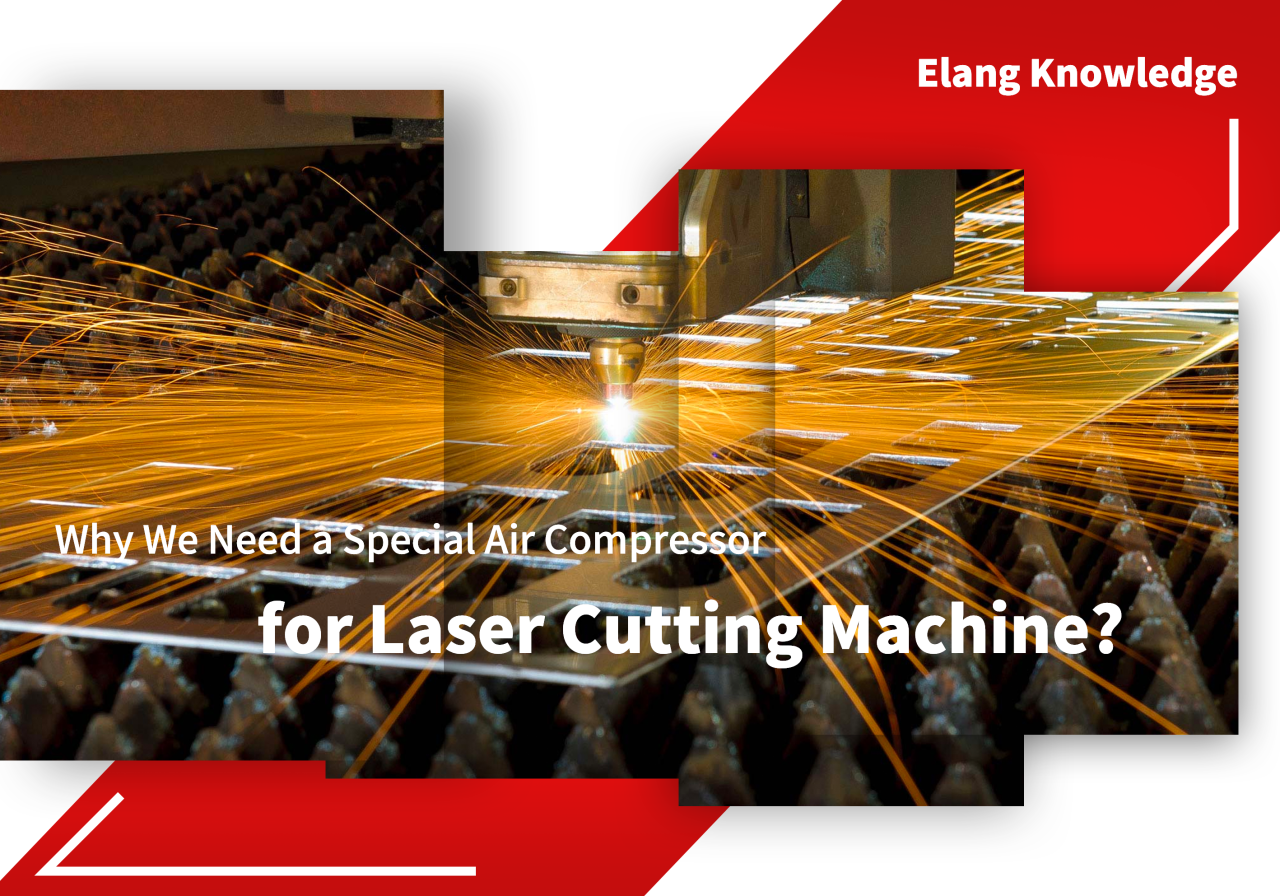
As we all know, to improve the processing efficiency of a laser cutting machine, it is necessary to introduce auxiliary gases during the processing, such as air, oxygen, nitrogen, and other gases. Among these auxiliary gases, air is the most cost-effective option and is preferred by most customers. Therefore, to improve cutting performance, it is essential to have a special air compressors for laser cutting machine.
The Performance of Air Compressors in Laser Cutting
Air compressors are mainly used to compress air and provide high-pressure air. The gas from the cutting head of the laser cutting machine is mainly used to blow away burrs and residue, as well as to purge and clean the optical path system. The compressed air is discharged, passes through an air tank and a dryer, and then enters the air control cabinet. Through a precise processing system, it is transformed into clean and dry gas, which is used as cutting gas, cylinder power source, and positive pressure dust removal gas to improve the operational efficiency and service life of the laser cutting machine.
So How to Choose a Right Air Compressor for Laser Cutting Machines?
1. Stable Pressure: Laser cutting requires precise cutting depth and speed, so it requires an air compressor to maintain stable air output and pressure output. Laser cutting machines have relatively high quality requirements for compressed gas. The pressure generally requires 10-16 bar, and the air compressors used in laser cutting can basically meet this standard.
2. Filter Device: There may be a large amount of dust and oil smoke in the air, which is very detrimental to the operation of the laser. Therefore, the air compressor needs to have its own filter device to ensure the cleanliness of the air.
3. Compact and Small Size: Laser cutting requires a relatively small air flow, so it is necessary to choose a compact and small size air compressor.
Purchase Suggestions:
1. Choose a suitable model: Select a right air compressor model based on the air supply requirements of the laser cutting machine.
2. Confirm the working pressure and air flow: Choose an air compressor that meets the working pressure and air flow required by the laser cutting machine.
3. Consider noise level: Since laser cutting requires a relatively small air flow, you can opt for an air compressor with lower noise levels to reduce noise pollution.
4. Attention to filter element replacement: Regular replacement of the air compressor filter element can ensure the cleanliness of the air and reduce damage to the laser.
How to use an air compressor better for laser cutting machine?
1. Manually exhaust and drain the air tank before starting the machine every day;
2. After turning on the refrigerated air dryer for 3 minutes, start the compressor when the pressure inside the pipeline is above 0.5 Mpa, and then activate the adsorption dryer.
3. When shutting down, it is essential to ensure that the pipeline pressure is above 0.5 MPa before turning off the adsorption air dryer.
4. Ensure that the compressor fan starts and stops correctly and that the temperature is within normal range.
5. Strictly follow the air compressor maintenance guidelines to perform regular maintenance on the air compressor.
Recommendations for Elang Air Compressor in Laser Cutting:
Power: 7.5 – 22 kw
Working Pressure: 7 – 16 bar
Air Delivery: 0.5 – 3.8 m3/min