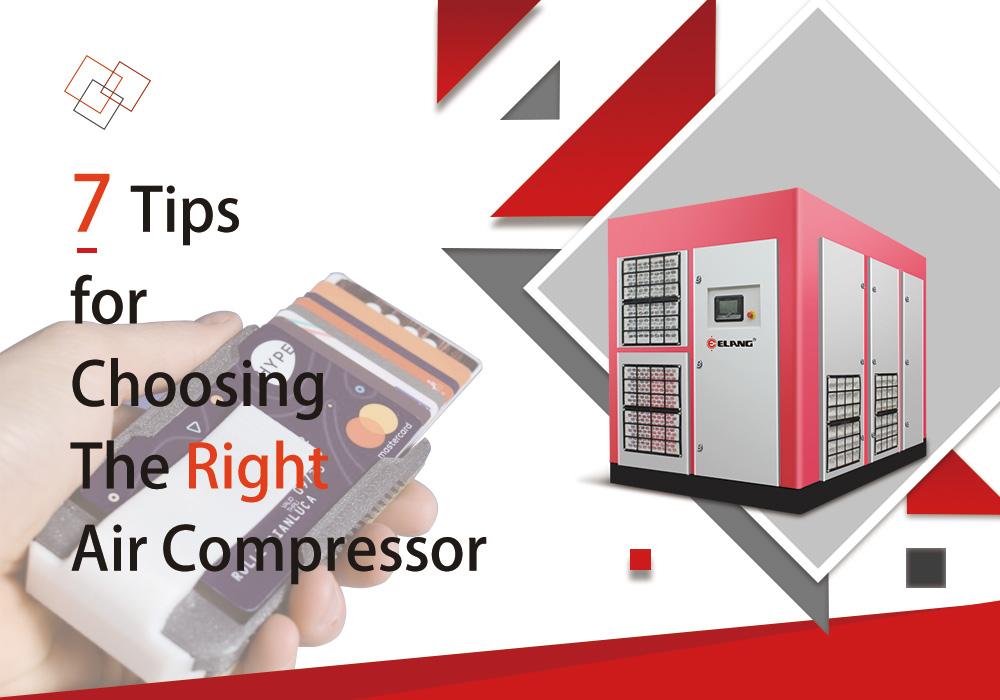
When purchasing an air compressor, many customers often consider whether the equipment’s performance can meet their compressed air needs. There are actually many air compressors available in the market, and at this time, they don’t know how to choose. We have summarized 7 points for purchasing an air compressor.
1. Air Flow
Firstly, you need to consult with the equipment manager or a technical engineer to determine the air flow required for a gas end equipment, commonly referred to as m3/min (units). To choose a right air compressor, you need to know the air flow, and then add 20% – 25% to the current air flow as a backup to account for gas pipeline losses and future increases in air flow. It is the most basic selection factor for selecting an air compressor.
Calculation:
Total air flow = (Equipment 1 air flow + Equipment 2 air flow + Equipment n air flow) *1.25
2. Working Pressure
Just like the air flow, it is necessary to determine the terminal working pressure with the engineer.
Calculation:
Working pressure = end-user + final filter + pipeline system + dust filter + dryer + compressor adjustment range
3. Electrical Network
Once the working pressure of the equipment is confirmed, the next step is to verify the electrical requirements. You can ask the electrician to check the factory’s electrical network to determine whether it is single-phase or three-phase power. It’s also essential to confirm if there are any changes in the compressed air demand at the end-user. If there are variations in the air flow, and if the air compressor’s load time exceeds 5 minutes, it’s advisable to choose a VSD air compressor. In many cases, the air flow of air compressors is not continuous, and using a VSD air compressor can increase motor efficiency and save electricity.
4. Noise Level
The noise level of the air compressor is another important consideration. If the company has an independent air compressor room, the noise requirements for the air compressor can be reasonably reduced. However, if the working environment of the air compressor is close to your workspace, then you should consider the noise level of the air compressor. In such cases, a silent or low-noise air compressor should be considered.
5. Auxiliary Equipment Configuration
It is essential to determine the need for after-treatment equipment and air tank. If the end-user has high-quality requirements for compressed air or if the compressor operates in a high humidity environment, it may be necessary to install a dryer or pipeline filter. An air tank can be used to ensure the working pressure.
6. Convenient Service
Ensure the convenience of after-sales service for the air compressor to guarantee the long-term stable operation of the equipment.
7. Compressed Air Cost
In addition, when a factory is selecting an air compressor, it needs to consider costs from three parts: purchase cost, electricity cost and maintenance cost. If you want to learn more about the compressor cost, click the article named “Analyse The Cost of Compressed Air”.
Air compressors are essential equipment in industrial production, and the selection process should be based on the requirements of the production process to determine the most suitable model. When selecting an air compressor, factors to consider include working pressure, output, energy consumption, noise level, maintenance costs and more. Additionally, one should pay attention to factors such as the equipment’s brand, model, quality, and maintenance status. Only by choosing the right air compressor and adopting appropriate maintenance measures can the normal operation of the air compressor and increased production efficiency be ensured.
FAQ
1. What can I do if the noise from the air compressor is too loud?
Air compressors will produce noise when working, but if the noise exceeds a certain level, it will affect the working environment and the health of employees.
Solution: Choose a low noise level air compressor; Install a soundproof cover to reduce noise; Reasonably arrange the working time and location of the air compressor.
2. What should I do if the compressed air produced by the air compressor smells strange?
If the compressed air produced by the air compressor has an unusual odor, it could potentially affect the quality of the products.
Solution: Regularly clean the filters, install auxiliary equipment such as dryers and oil-water separators to improve air quality, and check for any air leaks.
3. What should I do if the efficiency of the air compressor is low?
Low energy efficiency in the air compressor can increase production costs, so measures need to be taken to improve efficiency.
Solution: Select models with higher energy efficiency, regularly clean the filters, install energy-saving devices such as inverter to reduce energy consumption, and schedule the air compressor’s operating time and cycles to avoid idling and unloaded operation.
4. Does the air compressor require regular maintenance?
The air compressor does require regular maintenance to ensure its proper operation and extend its service life.
Solution: Regularly replace filters and lubricating oil, perform periodic inspections, and clean the coolers and radiators, as well as inspect and clean wearing parts such as cylinders and valves.
5. How long is the service life of an air compressor?
The service life of an air compressor depends on factors such as its brand, model, quality, and maintenance. Generally, the service life of an air compressor is between 5 to 15 years. To extend the air compressor’s service life, it is essential to take appropriate maintenance measures and pay attention to the usage environment and conditions.