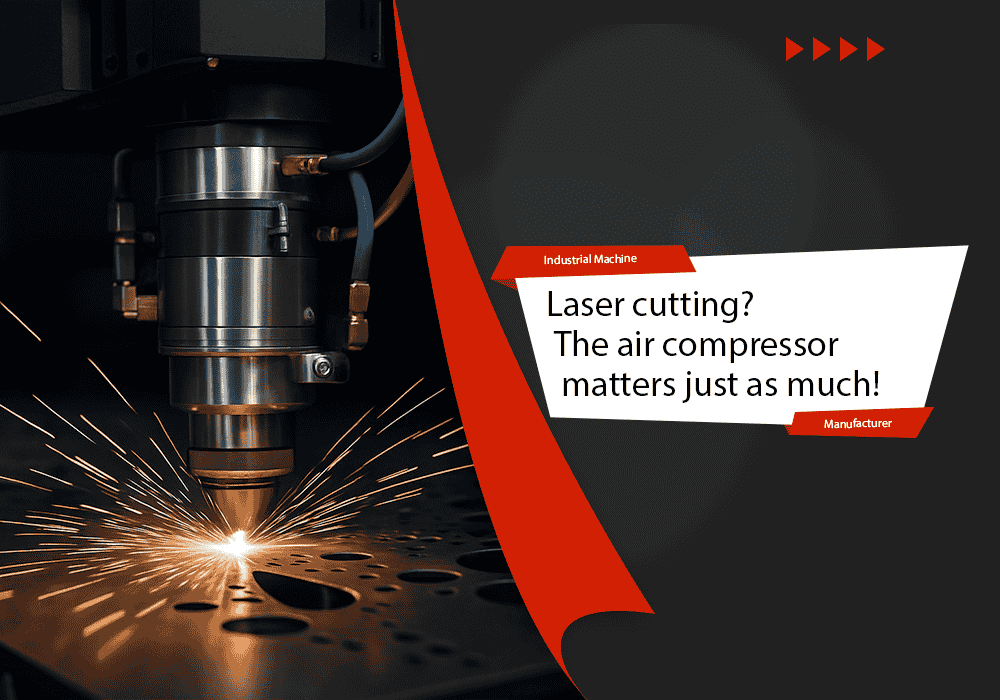
Laser cutting is the most widely used technology in laser processing applications. Laser cutting machines that use compressed air as an auxiliary gas for metal cutting are a common, economical, and practical processing method. This paper proposes a method for selecting air compressors and discusses issues to consider when using compressed air as an auxiliary gas for laser cutting.
Why is laser cutting related to air compressors?
Laser cutting machines utilise high-power, high-density lasers focused onto the material, causing it to melt, vaporise, ablate, or reach its ignition point. Simultaneously, a high-speed gas flow coaxial with the laser beam removes the molten material, thereby achieving the cutting of the workpiece. Laser cutting is one of the thermal cutting methods.
In this process, laser cutting requires auxiliary gases; these gases also serve to aid combustion, dissipate heat, and blow away molten residues generated during cutting, thereby protecting the laser cutting machine’s nozzle, focusing lens, and other components. However, oxygen and nitrogen in auxiliary gases either react chemically with the material or are expensive and difficult to extract. The most economical and practical option is compressed air produced by an air compressor.
How to choose the right air compressor for a fragile laser cutting machine?
Step 1: Compressed air quality
The quality of compressed air produced by air compressors and systems has a direct impact on laser cutting quality.
If compressed air contains oil and water mist that has not been properly treated, it will be sprayed onto the protective lens of the laser cutting head at high pressure, seriously affecting beam transmission, causing the focus to scatter, and significantly increasing the scrap rate. High-power laser cutting machines may even damage expensive laser head components.
Therefore, the quality of compressed air is extremely important. Elang’s expert consultants will carefully design compressed air systems for each customer’s project to ensure that the customer’s project runs smoothly.
Step 2: Air Compressor Pressure and Airflow Rate
The pressure of compressed air has little effect on the cutting thickness capability of laser cutting. As long as the laser power is sufficient, the higher the compressed air pressure, the better the cutting quality and efficiency. With the advancement of technology, the power of laser cutting machines has increased, and the pressure of the air compressors used with them has also risen accordingly, from the initial 8 bar to 13 bar, 16 bar, and even 20 to 30 bar.
Compressed air is divided into three components: cutting air, cylinder power source, and positive pressure dust removal gas for the optical path. Cutting air accounts for 80%–90% of total consumption. Even laser cutting machines that use nitrogen or oxygen as auxiliary gases still require a small air compressor with a pressure of 6–7 bar as the cylinder power source.
Airflow volume requires professional formula calculations, which are not detailed here, but the calculation method is provided for reference:
Q: Air flow rate, S: Effective area of the nozzle;
μ: Flow coefficient μ<1, generally taken as 0.92~0.94
A: Nozzle area d: Nozzle diameter, m
p: Absolute pressure in front of the nozzle, Pa
T: Gas stagnation temperature in front of the nozzle, K
QN: Actual exhaust volume
Step 3: Air compressor selection and system design
As mentioned earlier, the quality of compressed air directly affects the quality of laser cutting. Due to continuous operation to increase production capacity, the compressor must be located near the laser cutting machine. Therefore, the air compressor must be equipped with a good dryer and be able to quickly cool the compressed air to room temperature.
Although piston air compressors can easily achieve high pressures, they are noisy and do not handle oil well. Therefore, for pressures below 1.6 MPa, it is recommended to choose a screw air compressor equipped with a cold dryer and a precision filter. Using a permanent magnet variable frequency air compressor can maintain stable working pressure and ensure the best cutting results.
Since most users lack knowledge of air compressors and compressed air purification, if they were to purchase air compressors, air tanks, refrigerated dryers, and filters individually and install them themselves, it would not only be troublesome but also likely result in the entire system failing to meet the required compressed air quality standards.
Elang’s Belt Driven Combined Screw Air Compressors, specifically designed for laser cutting, combine the compressor, air tank, refrigerated dryer, and filter into one unit. This eliminates the need for users to source their own air tanks, refrigerated dryers, and filters, avoids the hassle of on-site installation and piping, and eliminates the need to coordinate services from multiple suppliers. The PMERC series provides continuous, stable, and clean compressed air, making it an ideal choice for high-power laser cutting machines.
Conclusion
Laser cutting machines that use compressed air as an auxiliary gas have a wide range of applications. They can replace oxygen for cutting thin carbon steel plates and replace nitrogen for cutting stainless steel, galvanised plates, aluminium alloys, and copper alloys. Correctly selecting and using an air compressor not only ensures laser cutting quality but also achieves good cutting efficiency and significant savings in processing costs.