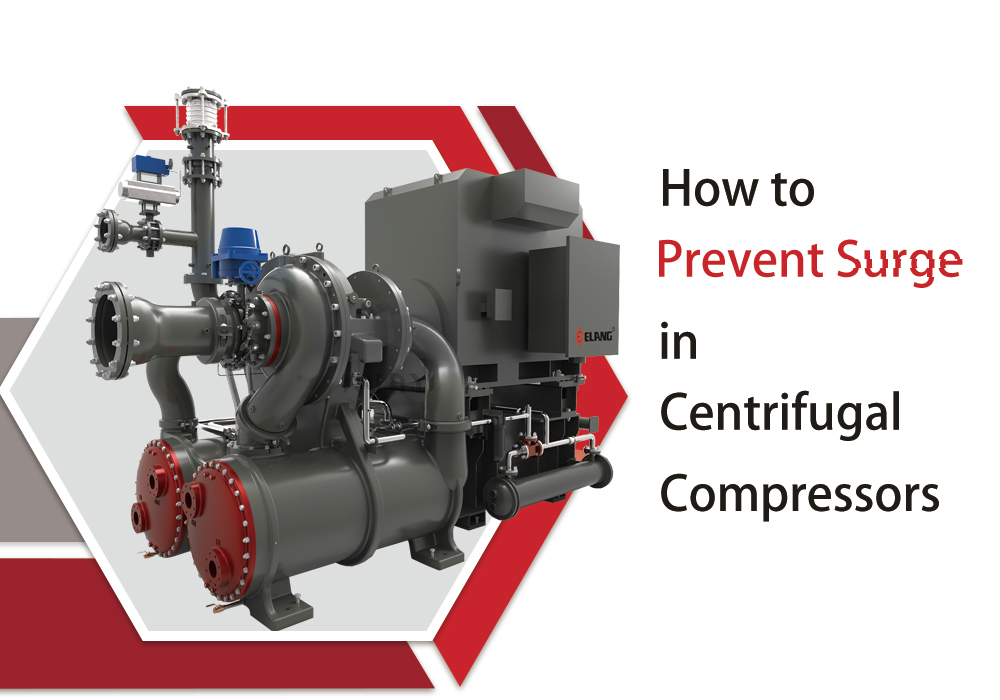
Surge is an inherent characteristic of centrifugal compressors, and the sole direct cause of surge is a reduction in the inlet flow rate.
What is surging in centrifugal compressors?
Surge is an inherent characteristic of centrifugal compressors, and the sole direct cause of surge is a reduction in the inlet flow rate.
When the flow rate decreases to a certain extent, rotational detachment may occur. Further reduction in flow rate leads to the formation of a large vortex region on the backside of the blades. The flow separation layer extends throughout the entire passage, blocking the flow passage, and the airflow cannot smoothly pass through. At this point, the flow severely deteriorates, and the outlet pressure of the compressor suddenly drops significantly. As the compressor always works in conjunction with the pipeline system, the pressure in the pipeline does not immediately decrease. Therefore, the air pressure in the pipeline becomes higher than the outlet pressure of the compressor, causing the air in the pipeline to reverse flow towards the compressor until the pressure in the pipeline drops below the outlet pressure of the compressor. The reverse flow stops, and the compressor resumes supplying air to the pipeline. With the increased flow through the compressor, it returns to normal operation. However, when the pressure in the pipeline returns to its original level, the flow through the compressor decreases again, causing reverse flow in the system. This cycle repeats, creating a periodic phenomenon of airflow oscillation throughout the entire system, known as “surge”.
The surge phenomenon is not only related to severe rotational detachment in the compressor but also to the characteristics of the pipeline system. The larger the capacity of the pipeline system, the larger the amplitude and the lower the frequency of surge. The frequency of surge is roughly inversely proportional to the square root of the pipeline capacity.
Phenomenon and judgment of surge
When the unit experiences surge, a low-frequency, high-amplitude pressure fluctuation occurs between the compressor and its downstream pipeline system. The entire unit undergoes intense vibration, emitting severe noise, and causing significant fluctuations in the control system. Typically, the determination of surge conditions is based on the following methods:
- Monitoring the airflow noise in the compressor outlet pipeline. Under normal conditions, the outlet noise is continuous and relatively low. However, when approaching surge, the airflow in the entire system experiences periodic oscillations, resulting in a cyclic variation in sound at the outlet pipeline. During surge, the noise intensifies, and explosive sounds may even occur.
- Observing changes in the airflow and outlet pressure of the centrifugal compressor. In stable operation, the outlet pressure and inlet flow of the centrifugal compressor exhibit small pulsations. When approaching or entering surge conditions, both variables experience significant changes with periodic, large-scale pulsations.
- Monitoring the vibration of the unit and shaft. As surge conditions are approached or entered, there is a pronounced increase in the intensity of vibrations in both the compressor body and shaft. The amplitude of these vibrations is substantially greater than during normal operation.
Dangers of Surge
Surge is an unstable operational state characterized by abnormal performance in centrifugal compressors. When surge occurs, the entire unit’s pipeline system experiences periodic airflow oscillations. This not only significantly deteriorates the performance of the compressor but also leads to substantial fluctuations in airflow parameters (pressure, flow). It subjects the rotor and stator components of the compressor to alternating dynamic stress, leads to strong vibrations due to inter-stage pressure imbalances, damages seals and bearings, and may even result in severe events such as rotor and stator components colliding, leakage of compressed air, and explosions. Therefore, it is crucial to avoid operating under surge conditions during operation.
Basic Causes of Surge
In actual operation, there are many reasons that can cause surge in compressors, but fundamentally, they can be categorized into the following two types:
The first situation: Actual operating flow is less than the surge flow. This may be due to factors such as excessive production reduction, insufficient intake air supply, clogged inlet filters, high pipeline resistance, blockage in impeller or airflow passages, etc.
Another situation: The outlet pressure of the compressor is lower than the pipeline pressure, such as increased pipe network resistance, low intake pressure, changes in compressor speed, etc. If the outlet pressure of the compressor is lower than the pipeline pressure, it will cause the operating point of the compressor to move towards the low-flow region, leading to surge conditions. This is not contradictory to the earlier statement that the only direct cause of surge is a reduction in the inlet flow to a certain value.
Related Reading
There is a wide variety of lubricating oil types with different performances. Therefore, users should choose appropriately based on the centrifugal air compressor’s bearing type, operating speed, load size, and process environment.