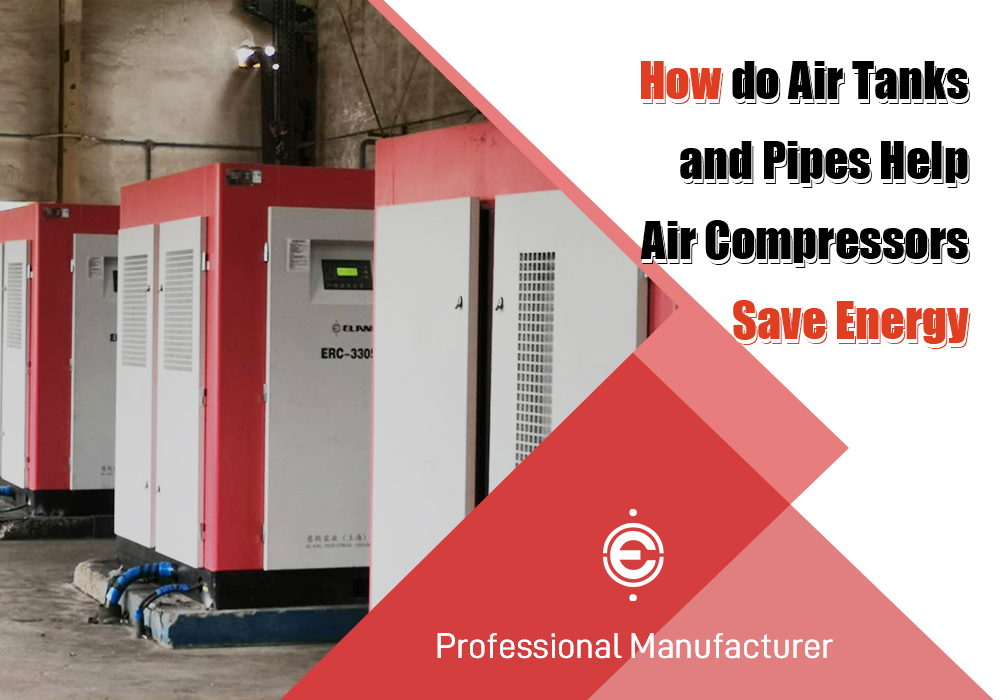
Energy saving in air compressors can be achieved not only by purchasing an energy-saving air compressor, but also by optimizing the air tank and pipeline.
After the compressed air is output from the air compressor, it needs to be transported to the using place through air tanks and pipelines. However, in practical applications, problems with air tanks and pipelines, such as air leakage, if not dealt with in time, will increase the energy consumption of the air compressor and lead to unnecessary waste of energy. Therefore, optimizing the design and use of air tanks and pipelines is also an important part of energy saving.
Due to the small capacity of the air tank, the volume of stored air is reduced, leading to frequent loading and unloading of the air compressor and a significant energy wasting. This issue can be effectively addressed by using a larger capacity air tank.
Bends in the pipeline increase the flow resistance of compressed air, creating additional energy consumption points. Additionally, bends generate gas impact, leading to localized pressure increases and causing the entire system to operate continuously at high pressure, making it prone to unloading. Therefore, optimizing the layout of the pipeline and minimizing the use of bends will reduce energy losses.
It is a continuously running system in the air compressor. Long-term operation may cause air leakage in various components and joints. Therefore, testing all points of the air compressor. When you discover inefficiency (leakage) points, replacing them in time will achieve maximum energy savings.
In a production line, different types of gas usage, such as continuous usage, small-scale pulse usage, large-scale pulse usage, open-air usage, etc., often share the same pipeline. Equipment for pulse gas usage requires a large amount of gas supply instantaneously, which may lead to a drop in pressure within the pipeline, preventing the continuous usage segment from obtaining sufficient pressure and thereby increasing the energy consumption of the air compressor. In response to this situation, it is necessary to configure air storage tanks reasonably, increase local energy storage and improve local pressure.
There are many possibilities for energy saving in air compressors. It’s important to recognize that the air compressor system is an integrated entity where the compressor, air storage tank, and pipelines are all integral components. During using, we need to remain vigilant, handle problems in time, reduce waste, and achieve true energy saving.
Related Reading
Firstly, we should understand the cost composition of compressed air: the first purchase cost only accounts for a small part of the total cost of compressed air. In fact, the full cost of compressed air includes three parts: “purchase cost,” “operating cost,” and “extra cost.”