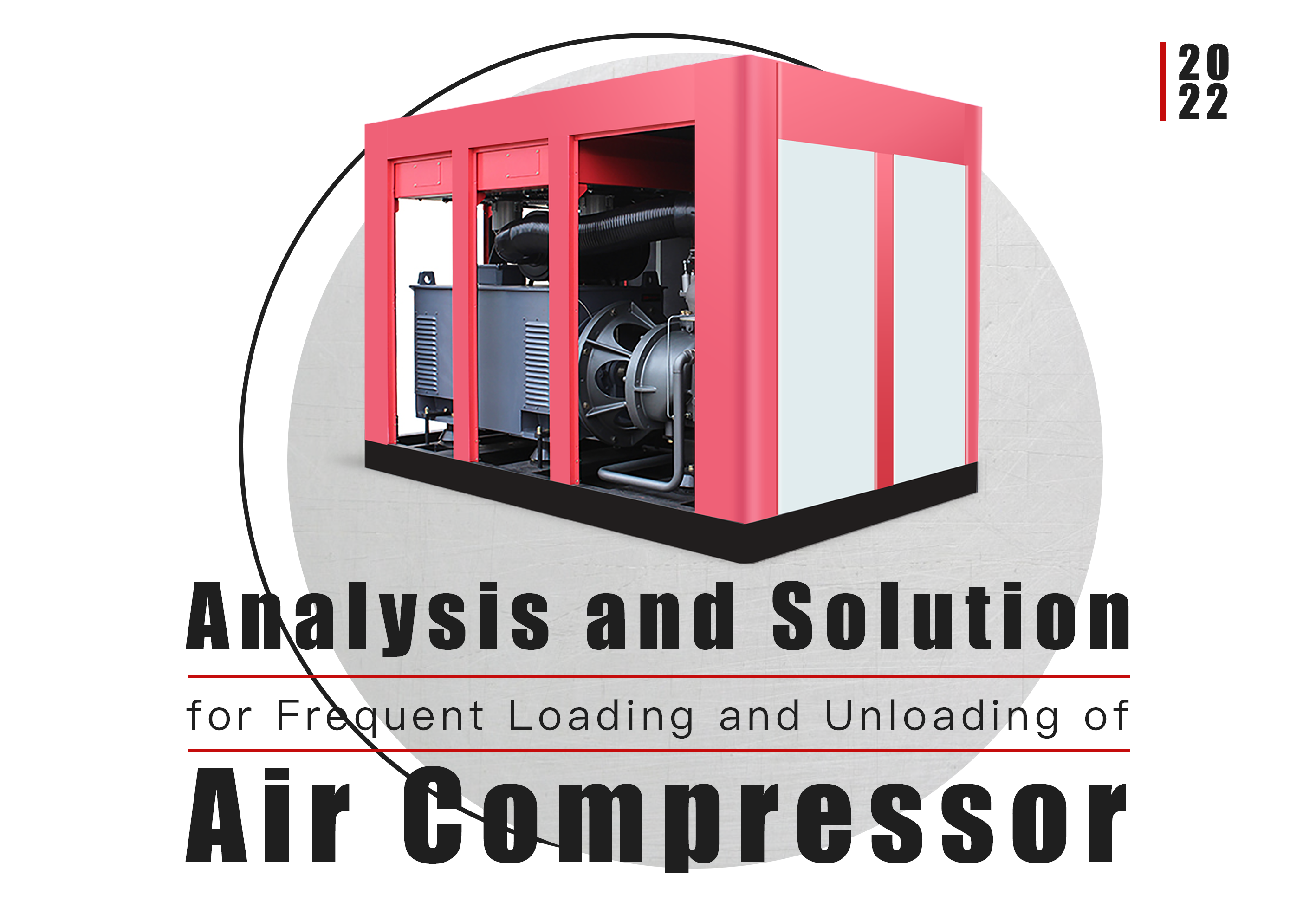
Frequent loading and unloading means that the screw air compressor has a very short interval from loading to unloading, and this cycle is frequent.
The consequences of frequent loading and unloading of air compressors
The fault performance is lower than the loading pressure, the air compressor begins to load and exhaust, the pressure rises rapidly, and the set unloading pressure is reached in a few seconds to ten seconds,the air compressor unloading stops the exhaust, the pressure drops rapidly, the pressure drops to the set loading pressure for a few seconds to ten seconds, the air compressor begins to load the exhaust, and the cycle is carried out.
If the problem can not be solved in time, it is easy to reduce the efficiency of the air compressor and damage the equipment.In particular, the frequent loading and unloading of air compressors not only shortens the life of the solenoid valve, air compressor entrance door and unloading valve, but also seriously threatens the safe operation of the air compressor.
The reasons for frequent loading and unloading of air compressors
1. Reason of control
It is well known that that the exhaust pressure of an air compressor is the main parameter for controlling its loading and unloading. If the difference between loading pressure and unloading pressure Settings becomes smaller, it may lead to frequent loading and unloading. When the loading pressure value of the unit increases while the unloading pressure value decreases, or when only the loading pressure value increases and the unloading pressure value decreases, it will result in a shorter loading and unloading cycle of the unit. In other words, when the loading and unloading pressure values are closer to each other with a constant air consumption, the frequency of loading and unloading increases, posing a greater risk to the safe operation of the equipment.
2. System reasons
If the air compressor’s loading and unloading pressure setting value is normal, we can consider whether there is pipeline blockage between the air compressor outlet and the gas storage tank.If the pipeline is blocked but not completely cut off, the compressed air flow will be seriously hindered, the gas pressure between the blockage point and the air compressor is difficult to be released quickly during the loading of the air compressor, resulting in the unloading pressure value being reached in a very short time.Due to the limited air volume between the blockage point and the outlet of the air compressor, coupled with the system loss (such as the filter drainage with gas, the regeneration of the cold and air dryer) and a small part of the flow to the gas storage tank, the pressure is quickly reduced to the loading pressure value, the air compressor is reloaded, and so on.
Treatment method when air compressor frequent loading and unloading
1. Treatment methods for frequent loading and unloading caused by control issues
This cause can be directly identified through the pressure display during the loading and unloading of the unit. If any changes are observed, they can be resolved through online calibration or by removing the pressure sensor for detailed inspection and reinstallation. However, it is quite common for measurement errors to occur due to blockages in the pressure sensor measurement lines. In such cases, our usual approach is to use compressed air for blowing and sampling the lines.
2. Treatment methods for frequent loading and unloading caused by system issues
Dealing with system-related causes is more complex, and it can be determined by the difference between the air compressor outlet pressure and the refrigerated dryer outlet pressure. If there is a significant difference or if the difference is too large (generally ≤0.6 bar for filters and ≥0.2 bar for the refrigerated dryer), it can be concluded that there is a blockage in the pipeline or equipment. After long-term maintenance and observation of this pipeline system, it has been found that the following equipment is prone to blockage:
- Oil and water filters
- Switching valves at the inlet of adsorption dryers A and B
- Poor temperature adjustment of the pre-cooler and evaporator inside the refrigerated dryer
- Incorrect installation of one-way valves at the outlet of dust filters or detachment of valve stems from the valve bodies.
For more technical content about unloading and loading of air compressors, please refer to the source, if you need, please contact our Elang professional after-sales team, 24 hours to provide support!