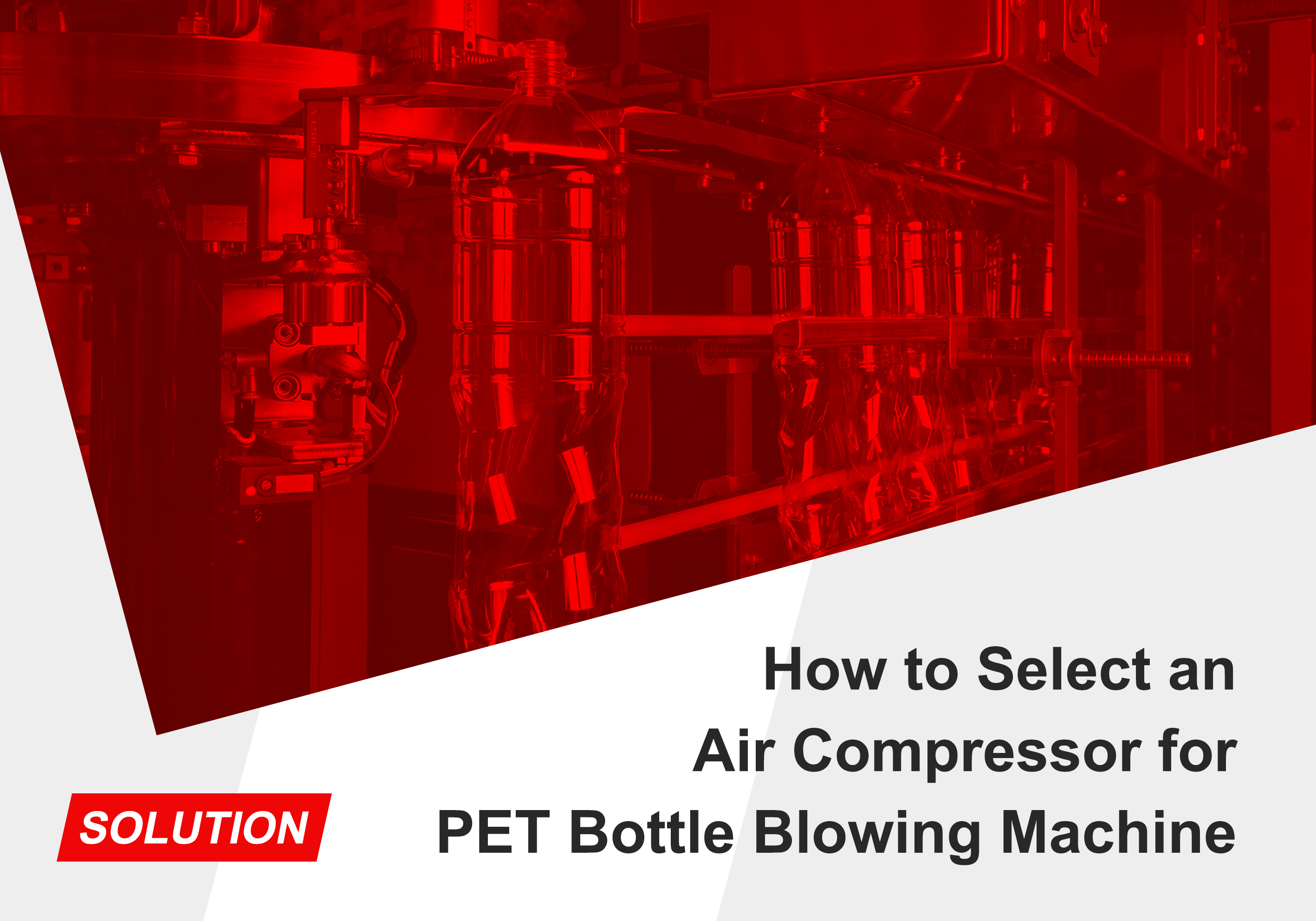
Bottled water, various beverages, cooking oil, condiments, and more are ubiquitous in our daily. Many of these products are packaged in PET plastic bottles. In this article we are about to explore the process of producing these bottles, the production machinery and how to choose the right PET bottle blowing compressor.
PET Blow Moulding Process
The superheated plastic is injected into a preform mould in the production line and then cooled quickly to form the preform for the next step. The preforms are heated and placed into container moulds where compressed air (hot air) produced using an air compressor is blown into the preforms to stretch them into the shape of a bottle. After cooling, the mould is opened and the final shaped bottle is removed.
Equipment for PET Bottle Blowing
The answer lies in the PET bottle blowing system. In the process of PET bottle manufacturing, in addition to a blowing machine that can meet the economic efficiency and production needs, a PET high pressure oil-free air compressor is also required to provide the necessary air supply.
In the field of bottle blowing, PET compressor as a core air supply device, converts mechanical energy into compressed air pressure. It is a pressure generating device specifically designed for stretching and forming PET bottles, matching with a special bottom blowing machine. PET compressors play a key role in the auxiliary equipment of blow moulding machines.
The Right PET Bottle Compressor
Firstly, it is necessary to determine the required gas consumption and pressure based on the production capacity of the bottle blowing machine and the design of the bottles, and to appropriately reserve some margin. Different models of matching air compressors produce different airflow outputs and pressures. In general, the higher the exhaust pressure of an air compressor, the higher the energy consumption. When making a purchase decision, users need to consider the operational pressure of the machine, pipeline resistance, and pressure loss of auxiliary equipment, using these as selection standards. It is important to choose an air compressor that matches the pressure of your equipment, as excessive gas demand can lead to wasted energy and increased energy consumption during compressor operation.
Secondly, when choosing suitable supporting air compressors for bottle blowing machines, it is important to ensure they meet the specific requirements of different production process equipment on compressed air pressure. In addition, the quality of the compressed air is crucial as it directly affects the quality of the product. When choosing a special air compressor for bottle blowing machines, you should select a brand that suits the production needs of the factory according to the characteristics and requirements of the air compressor. Major PET bottle manufacturing plants worldwide prefer water-cooled reciprocating piston oil-free air compressors that adhere to the ISO 8573-1 oil-free standard as their primary air compressor support equipment. These compressors has high gas production, high efficiency, oil-free compressed gas output, high stability, low failure rate, and employ high-temperature wear-resistant materials for extended durability of spare parts, ensuring continuous high-speed operation for 24 hours.
PET blowing air compressor is divided into: low pressure blowing machine (15-25 bar), medium pressure blowing machine (25-35 bar), high pressure blowing machine (35-40 bar). There are many types of blowing air compressors, which are classified according to their working principle as reciprocating compressors, screw compressors and centrifugal compressors. Reciprocating compressors increase the density of gas molecules by compressing the volume of the gas, thus increasing the pressure of the compressed air. Screw compressors increase the pressure of compressed air by converting the kinetic energy of the gas in the compressor chamber into pressure energy through twin-screw compression. Centrifugal compressors utilize the high speed rotation of the impellers to convert the gas into kinetic energy at high centrifugal speeds, thereby providing compressed air pressure. These compressors are available in different models such as portable and stationary.
Recommendation for PET Bottle Blowing Air Compressor:
Power: 9 – 22*3 kw
Working Pressure: 30 – 50 bar
Air Delivery: 0.6 – 6.0 m3/min
Motor Power: 11 – 250 kw
Working Pressure: 30 – 40 bar
Air Delivery: 1 – 21 m3/min
Motor Power: 45 – 355 kw
Working Pressure: 16 – 40 bar
Air Delivery: 5.2 – 35 m3/min