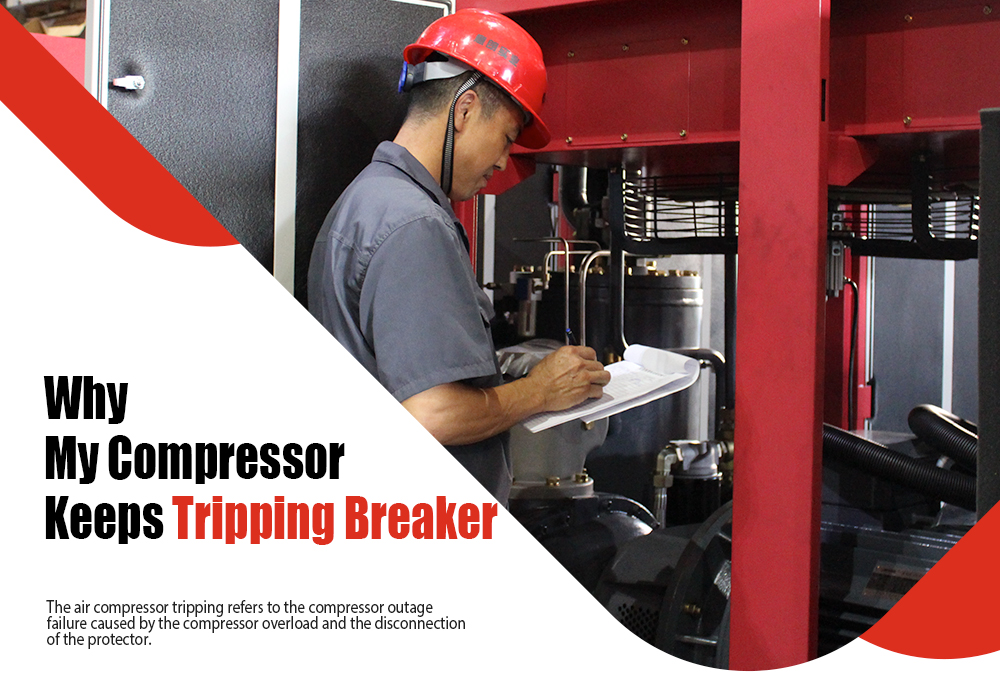
Tripping breaker refers to a situation where the compressor experiences an outage or failure due to overload conditions and the disconnection of the protector.
The air compressor is a fundamental product in industrial modernization, serving as a device for producing compressed air and a core component of pneumatic systems. It converts the mechanical energy of an electric motor into the pressure energy of gas. The normal operation of an air compressor relies on electrical power. However, if the compressor trips and fails to operate properly shortly after starting up, it can result in significant losses for the user.
What is the reason for tripping breaker, and how should we deal with it?
1. High Temperature Environment
(1)The operating environment has a high temperature, and relevant cooling measures have not been implemented, leading to abnormal internal conditions.
(2)Insufficient ventilation between the surrounding environment and the outside prevents timely heat dissipation.
2. Start with Pressure
Check the pressure guage of the oil and gas separator. If the pressure gauge indicates pressure, it is initially determined that there may be incomplete system depressurization, leading to a pressurized startup of the compressor. As a result, the excessive startup current triggers the air switch to protect the unit, causing it to trip. This situation often occurs in screw air compressors due to malfunctioning the minimum pressure valve or the blockage in the pressure relief system, which can result in residual pressure remaining in the system even after the compressor shuts down.
Checking the pressure gauge on site shows that there is pressure. Generally, there are two possibilities:
1. The system is under pressure.
2. The pressure gauge is damaged and unable to return to zero properly.
Judgment method: Open the device or valve that can relieve pressure in the system. When the pressure relief valve is opened and the pressure gauge in the oil and gas separator shows that there is still pressure, it can be concluded that the system is already depressurized and the pressure gauge is unable to return to zero. Conversely, if there is still pressure indicated on the pressure gauge, it indicates that the system is still under pressure.
3. Excessive Resistance of Air End
Excessive resistance of air end can cause the compressor to experience high startup current, leading to compressor overload and cause the air switch to trip.
There are three main situations that cause the resistance of air end to increase:
(1) The lubricating oil’s high viscosity can contribute to increased head resistance. In regions with significant temperature variations, such as the southern parts, ambient temperatures can reach as high as approximately 40°C in summer and drop below freezing in winter. As the viscosity of lubricating oil is inversely proportional to temperature, the oil’s viscosity increases significantly during winter compared to summer. Additionally, after winter shutdown, the presence of moisture in the equipment’s lubricating oil environment can lead to water freezing and obstructing the oil circuit’s circulation. Therefore, it is crucial to avoid directly starting the air compressor in winter and instead perform several cycles to facilitate the circulation process of the viscous lubricating oil.
(2) For single screw compressors, the screw and star wheel in the air end are coking. The work of the single-screw compressor is mainly completed by the engagement of the screw and the star wheel. The gap between the screw and the star wheel determines the work efficiency of the compressor. If the gap is too large, part of the gas will leak from the gap, and the compressor will have low work efficiency; if the gap is too small, the resistance between the star wheel and the screw will be large, the load will be large, and the motor will consume more energy. Coking in the air end can cause the gap between the star wheel and the screw to decrease, the frictional resistance in meshing is large, and the current of the compressor increases.
(3) Excessive lubricating oil in the air end can contribute to increased head resistance. When the oil stop valve at the air end outlet fails to close promptly after compressor shutdown, a substantial amount of lubricating oil is forced into the air end. This causes excessive starting resistance during the startup process, leading to increased current and tripping of the overload protection.
Solution Options:
- Manual cranking:
1.1. Perform manual cranking of the compressor before starting to ensure the free rotation of power components, transmission components, and linkage components.
1.2. Observe any increase in resistance during manual cranking, which may indicate issues that need further inspection and maintenance. - Addressing oil coking in the air end:
2.1. Improve the quality of lubricating oil used in the compressor and ensure it is suitable for high-temperature conditions.
2.2. Implement regular maintenance and cleaning procedures to prevent oil coking and remove any existing deposits.
2.3. Monitor and adjust the clearances between screws or between the screw and the star to maintain optimal performance. - Resolving excessive lubricating oil in the air end:
3.1. Inspect and repair the oil cut-off valve on the oil injection pipe to ensure proper functioning.
3.2. Release excess lubricating oil from the air end by opening the end cover and draining the oil to the recommended level.
3.3. Consider replacing the oil cut-off valve if it is found to be faulty or ineffective.
4. Electrical Device Failure
(1) Electrical failure related to star-delta conversion:
-
- Check the star-delta switch and ensure its proper functioning. Repair or replace it if necessary.
- Verify the correct sequence and timing of the star-delta conversion process during motor startup.
Inspect the air switch for any vibration-related issues and adjust its set start time if needed.
(2) Differentiating between electrical and mechanical failures:
- Separate the motor from the air end by removing the coupling or belt connecting them.
- Manually rotate the main compressor and motor to identify and eliminate any mechanical issues.
- If the motor runs normally without load, it indicates a problem with the electrical components.
(3) Motor-related issues:
- Check for motor bearing problems or misalignment between the motor and the compressor host.
- Ensure the motor operates smoothly under load and investigate any overload or tripping problems during operation.
(4) Electronic control system failures:
- Inspect the temperature probes, relays, and circuit breakers in the electronic control system.
- Address any false alarms, over-temperature trips, or malfunctions by repairing or replacing faulty components.
5. Unloading Valve Failure
The unloading valve plays a crucial role in controlling the loading and unloading of a screw compressor, specifically regulating the air intake. The unloading valve is opened in advance is a type of failure that is not easy to find. Normally, the unloading valve remains closed before starting the compressor and gradually opens during the startup process or fully opens after startup completion. If the unloading valve opens too early, it indicates excessive loading during compressor startup, resulting in an increased starting current and causing the compressor to trip.
The most intuitive way to judge whether the unloading valve is closed or not to remove the air filter and visually inspect the position of the air intake baffle on the unloading valve. It should be clearly visible whether the baffle is in a closed or open state. Common unloading valve failures involve the intake flap becoming stuck on the guide rod. In such cases, the piston’s position should close the intake flap, but it remains open due to the obstruction. Mechanical impurities can also cause the intake baffle to become stuck, preventing proper closure of the unloading valve.
After removing the air filter, if the intake baffle is stuck due to mechanical impurities, cleaning it will enable smooth operation. If the intake baffle is stuck on the guide rod, using sandpaper to grind the guide rod and applying a small amount of grease can resolve the issue. In severe cases of unloading valve damage, replacement is necessary.
To judge whether the unloading valve opens in advance, it is essential to precisely track the compressor’s start time and compare it with the time the unloading valve opens. If the unloading valve does not open in advance, it indicates normal operation; otherwise, it suggests that the unloading valve is prematurely opened.
6. High Temperature Trip Caused by Temperature Control Valve
Some instances of high-temperature trips are not due to external temperature or inadequate unit heat dissipation but rather stem from improper operation of the temperature control valve.
The temperature control bypass valve incorporates a temperature-sensing component, typically paraffin, which regulates the valve core through its probe. Over prolonged usage, the efficiency of the valve core diminishes, rendering it unable to function at the designated temperature threshold. Consequently, hot lubricating oil from the air compressor body either cannot be cooled or is returned directly to the compressor body via the oil cooler, resulting in ineffective temperature control.
Additionally, lubricating oil containing impurities can cause the sliding core of the temperature control valve to become obstructed, preventing the valve core from fully closing. As a result, a portion of the oil bypasses the intended route and flows directly to the machine, compromising the cooling effect.
7. High Temperature Trip Caused by Lubricating Oil
The failure of lubricating and cooling oil is a significant factor in compressor tripping. Lubricating oil in the air compressor serves the dual purpose of providing lubrication to moving parts such as the high-speed rotating rotor and sliding vane, as well as dissipating heat generated during the compression process. This includes frictional heat resulting from the high-speed movement of friction pairs and heat generated during air compression.
The air being compressed often contains dust, water, and corrosive gases like hydrogen fluoride and sulfur dioxide, which have a detrimental effect on the lubricating oil, rendering it ineffective. When lubricating oil fails, it fails to form an oil film on the moving parts, leading to increased frictional heat and reduced cooling capacity. Consequently, the temperature of the air compressor rises excessively during operation.
Furthermore, failures in the air cooler, water cooler, and three filters can also contribute to high-temperature tripping, and their effects are more pronounced. However, these specific causes have been previously discussed.
In summary, compressor tripping can result from various causes and factors. By gaining a comprehensive understanding of compressor operation principles and component functions, we can proactively prevent compressor tripping failures.