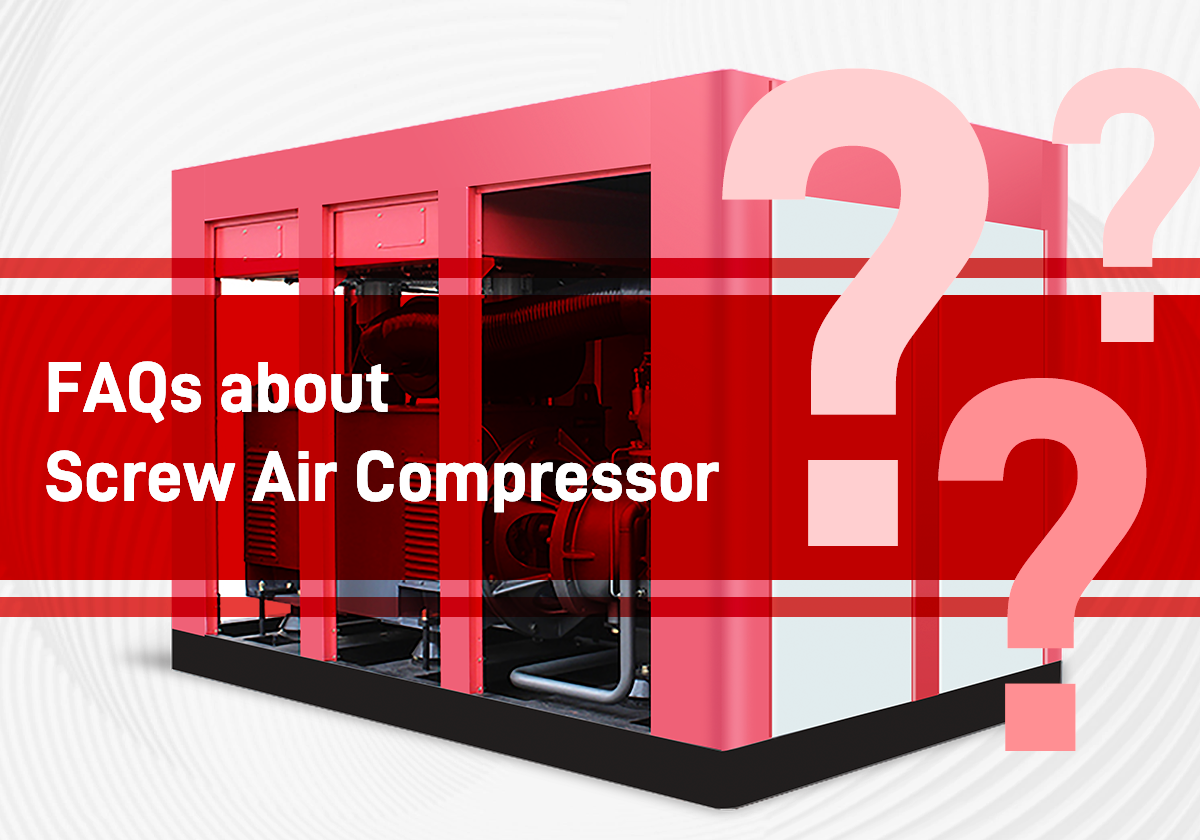
In our conversations with customers, we are well aware that they may encounter various problems and confusion when selecting, using, and maintaining screw air compressors. In order to provide better support and assistance to you, we have compiled a complete set of common technical questions and answers, hoping to solve your doubts and provide guidance.
Secondly, when the air compressor is in loaded state, the inlet valve closes, and pressure is released through the small hole to ensure smooth closure of the swing check valve.
- Air filtration. Dust particles carried in with the air intake thicken the oil, increasing the time of oil oxidation reaction, thus accelerating the formation of carbon deposits. Therefore, it is necessary to pay attention to the correct installation of the air filter, and if any damage is found during cleaning, it must be replaced.
- Temperature. Different grades and types of lubricating oil have different initial oxidation temperatures. Long term operation of air compressors in high-temperature areas will accelerate the oxidation of lubricating oil. For compressors equipped with water coolers, it is recommended to use treated or impurity-free cooling water to prevent blockage of the water passages.
- Lubricating oil quality. The lubricating oil provided by air compressor manufacturers usually does not accumulate carbon within the specified service life. Currently, there are many procurement channels for lubricating oil, and its quality may inevitably vary. Some users use alternative oils, and carbon deposits is not uncommon in such cases.
- Lubricating oil is used beyond its expiration date. If the lubricating oil continues to be used after exceeding the specified service life, the air compressor will be unable to operate in a short period of time due to carbon deposits.
2. Method for cleaning carbon deposits on the air end: For carbon deposits in the oil circuit and air end, specialized cleaning agents (carbon deposit remover or bearing cleaner) can be used. Cleaning can also be performed without disassembling the air end. For small air ends, they can be directly placed in a container for soaking, and during soaking, the rotor should be rotated several times. For large air ends, after closing the outlet and oil pipelines, the cleaning agent can be poured in for soaking. The soaking time should be determined according to the instructions of the cleaning agent, generally 8 to 12 hours. For some cleaning agents with strong corrosiveness, the soaking time specified by them should be strictly followed. After soaking, rinse with pressurized water, and then blow dry with compressed air.
It has been verified that good design, lubrication, and maintenance can prevent ignition accidents in oil-injected rotary compressors. One of the recognized causes of ignition is the failure of the cooling system, resulting in a rapid increase in exhaust temperature exceeding the normal temperature of the compressor. One of the recognized causes of ignition is the failure of the cooling system, resulting in a rapid increase in exhaust temperature exceeding the normal temperature of the compressor. When the carbon deposition layer in the hot zone increases sufficiently thick, it triggers a fire. In addition, damage to the temperature control valve can also increase the exhaust temperature, leading to accidents.
Additionally, abnormal temperature increases caused by clogged oil filter core can accelerate oil oxidation and also pose a risk of fire. The three important factors to prevent oil ignition hazards are: ① reasonable design; ② Proper selection of oil; ③ Operation and maintenance of compressors. The following points are particularly important: maintaining low fuel consumption, regularly changing oil, and ensuring the normal operation of the oil cooling system.
- Check the carbon deposits on the rotor;
- Check the intake valve servo cylinder diaphragm;
- Check and tighten the screws in various parts;
- Clean the air filter;
- Solve the problems of air compressor and pipeline leakage and oil seepage;
- Clean the cooler and replace the faulty valve;
- Inspect the safety valve and pressure gauge.
In addition to do a good job of all light repairs, it is also necessary to dismantle, repair, and replace some parts of the machine, such as dismantling the oil-gas tank, replacing the oil filter and oil-gas separator, checking the wear of the rotor, inspecting and adjusting the thermal control valve and pressure maintenance valve to restore normal operation of the machine.
Equipment Specifications | ||
Project | Unit | Technical Parameter |
Model | ||
Rated Displacement | m3/min | |
Rated exhaust pressure | MPa | |
Motor Speed | r/min | |
Shaft Power | kW | |
Spare Parts and Materials Required for Maintenance | ||
Spare parts | bearings, oil seals, O-rings, shaft sleeves, carbon cleaning agents, and oil pipes that need to be replaced | |
Materials | sealant, calico, lead tetroxide, machine cleaning cloth, sandpaper (# 0, # 1, # 2), gasoline or kerosene | |
Tools | ||
ring wrench, hex key, socket wrench, pipe wrench, copper rod, feeler gauge, hydraulic puller (self-made fixing plate), lifting shackle, steel wire rope, and pin puller (self-made) | ||
Safety Notes | ||
1. Take anti slip measures on site, avoid open flames when using gasoline, and use special tools to disassemble bearings; 2. When disassembling the male and female rotors, be careful to pull gently to prevent damage to the rotor; 3. After disassembling the male and female rotors, place them horizontally to prevent damage; 4. When reinstalling, use compressed air to clear and inspect the oil circuits of each part of the machine to prevent foreign objects; 5. When disassembling the gearbox, pay attention to lifting slowly to prevent gear damage. |
||
Process 0: Preparation work before maintenance 1.Understand the existing defects of the equipment and conduct pre repair identification; 2.Prepare to replace the wearing parts and tools for maintenance, lifting, cleaning; 3.Apply for maintenance work tickets.Process 1: disassembly 1. Contact the thermal process engineer to inspect each instrument and remove the instruments connected to the main body; 2. Drain all the lubricating oil inside the machine body; 3. Remove the air filter; 4. Remove the intake valve; 5. Remove cooling water pipes, oil pipes, measuring points and other fittings; 6. Remove the protector flywheel cover or flywheel V-belt; 7. Remove the motor anchor bolts; 8. Hang the machine body with a hoist, remove its anchor bolts, and lift it out.The following work is carried out in a clean maintenance site: 1. Rotate the rotor, inspect the appearance and wear of the male and female rotors, measure the axial and radial clearance between the male and female rotors and the machine body. 2. Remove the axle. 3. Remove the inlet end cover. Some models have a speed increasing gear mechanism. At this time, the gearbox should be removed; 4. Remove the inlet end cover and prepare to inspect and disassemble the bearings; 5. Remove the bearing bracket at the inlet end; 6. Install a puller at the exit end, separate the male and female rotors from the outlet end bearings, apply gentle force during disassembly, and rotate the rotor; 7. Take out the male and female rotors in sequence. Process 2: inspection and repair stage 2. Maintenance of male and female rotors 3. Maintenance of the machine body 4. Gear box maintenance 5. Bearings maintenance 6. Maintenance of shaft seal The following work should be done before assembly:
Process 3: assemble Quality Standard 2. Quality standards for fitting clearances of air compressors 3. Adjustment method for rotor axial clearance 4. Gearbox 5. Axis bending measurement Process 4: run-in |
If the working environment of the air compressor is humid with a lot of dust, the air filter will quickly become clogged. If the air filter of the air compressor is damaged during installation, transportation, or cleaning but continues to be used, the oil filter of the air compressor will soon become clogged. Additionally, The working environment temperature of the air compressor is high, and due to equipment reasons or failure to switch the air compressor in a timely manner, the air compressor will be shut down for a long time (such as about a month), which will cause the adhesive particles on the oil filter or oil-gas separator to dry up, block the filtering holes, and shorten the service life of the filters.Therefore, relying on running time as an unique standard for replacing the filters may lead to problems such as delayed replacement or waste.
Top 10 most-read technical articles
How to Select an Air Compressor for PET Bottle Blowing Machine?
Analysis and Solution for Frequent Loading and Unloading of Air Compressor
Exploring The Repair and Maintenance of Screw Air Compressors
- How does a Rotary Screw Air Compressor Work?
- 7 Tips for Choosing The Right Air Compressor
- How to Design a Compressor Room?
- Working Principle and Application of Oil Free Scroll Air Compressor
- Screw Air Compressor Troubleshooting Guide
- How to Design a Compressed Air System?
- How to Prevent Surge in Centrifugal Compressors?
Good News: We’ve set up a knowledge base offering more detailed information on the working principles, maintenance methods, and applications of screw air compressors. Click HERE to learn more!
-
4 Typical Types of Compressed Air Heat Recovery SystemsJanuary 30, 2024
-
How to Design a Compressed Air System?February 21, 2024
-
Elang Nantong Factory has been Completed SuccessfullyMarch 15, 2023
-
2024 International Machinery Exhibition UZ (Uzbekistan)August 28, 2024
-
Beyond Filtration: Why Textiles Demand Oil-Free AirAugust 15, 2025
-
Dry screw vacuum pumps in the ceramics industryJuly 4, 2025